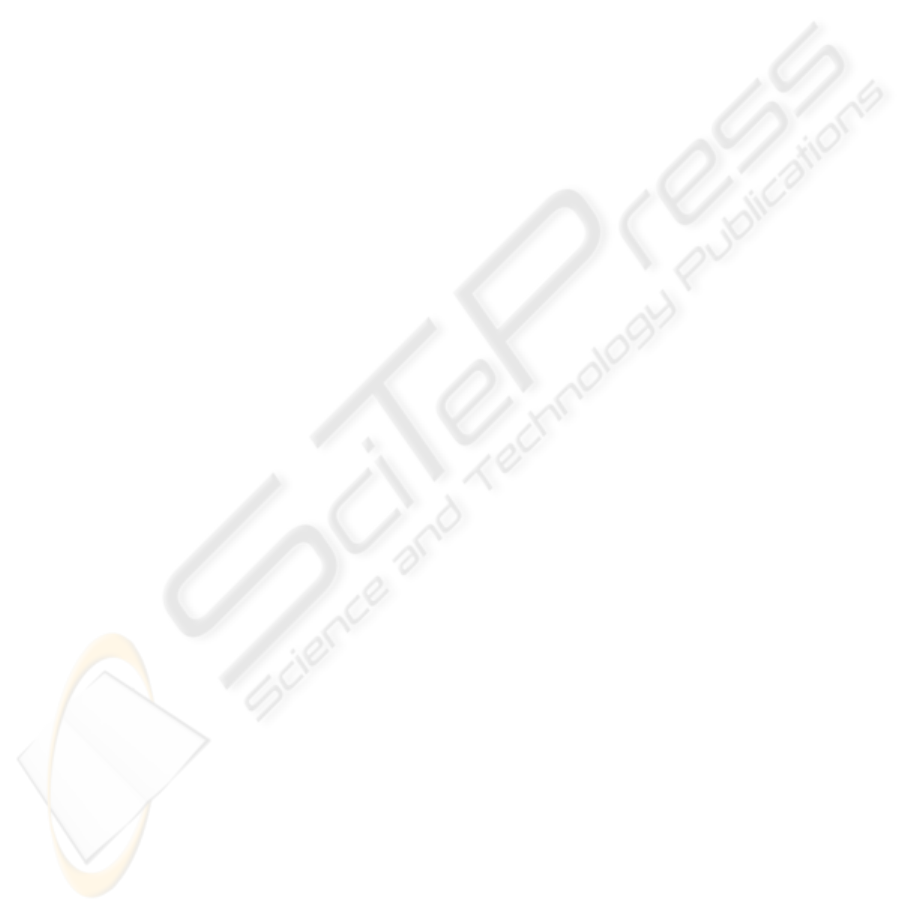
• Oil properties: viscosity, Total Base Number
(TBN) and detergency.
• Oil contaminants: Insoluble compounds, fuel dilu-
tion, soot, ingested dust (silicon), water and glycol.
• Metallic elements: iron, copper, lead, chrome, alu-
minum, tin, nickel, sodium and boron.
Other measurements could be performed upon the oil
sample, but with these basic parameters a good diag-
nosis can be achieved. Systems developed for other
types of engines could choose other parameters tak-
ing into account the particularities of these types of
engines.
Let us consider, as an example, the kind of knowl-
edge involved on the dust contamination detection.
Silica and silicates are present at high concentra-
tions in natural soils and dusts. It is for this reason that
silicon is used as the most important indicator of dust
entry into an engine. There have been several studies
done on the causes of premature wear in components
and results vary from study to study but one thing is
clear: external contamination of lube oil by silicon is
a major cause of accelerated wear. Particles of air-
borne dust vary in size, shape and abrasive properties
and in an engine the ingress of atmospheric dust takes
place primarily through the air intake. Those parti-
cles, not retained by filters, and similar in size to the
oil film clearance in main lubricated parts of the en-
gine do the maximum damage. Once the dust particle
has entered an oil film it forms a direct link between
the two surfaces, nullifying the effect of the oil film,
thus, the immediate consequence is a ”scratching” of
the surface as the particle is dragged and rolled across
the surfaces. The second and potentially more serious
problem is that once the dust particle is introduced
in between the two surfaces, it changes the loading of
the surface from an even distribution to a load concen-
trated on the particle with a huge increase in pressure
at this point. The increase in pressure causes a de-
flection of the surface, which will eventually result in
metal fatigue and the surface breaking up. As soon as
a dust entry problem occurs there is an increase in the
silicon concentration into the oil and an acceleration
of the wear pattern. As long as the oil samples are
being taken at regular intervals in the correct manner,
the dust entry will be detected at a very early stage. If
an effective corrective action is taken, the life of the
component will be significantly increased, reducing
maintenance costs.
Diagnosis of silicon contamination (dust inges-
tion):
• If normal wear patterns combine with high silicon
readings in oil analysis, there are three possibilities:
a silicone sealant, grease or additive is in use mix-
ing with engine oil, an accidental contamination of
the sample has occurred or dust ingestion is in the
first stage and no others wear patterns are present
yet (too lucky situation). Action recommend to the
maintenance technicians must be to check if an ad-
ditive, grease or sealant has been used recently on
the engine and make sure that the correct sampling
technique was used. An inspection of the air ad-
mission system on the engine will be necessary if
previous action results negative.
• Increased engine top-end wear (iron, chromium, or
aluminium concentration rises up). This increased
engine top-end wear is caused by airborne dust that
has been drawn into the combustion chamber being
forced down between the ring, piston and cylinder.
Dust origin is caused by a defective air cleaner or
a damaged induction system. Actions to be taken
by maintenance technicians are inspect the air filter
element thoroughly, and check its seals and support
frame for damage and distortion and check too the
pleats for damage. If there is any doubt about a
filter element, it should always be changed. If the
leak was found, it is necessary to repair the leak and
determine the condition of the engine by checking
compression or blowby.
• Increased engine bottom-end wear (lead, tin or cop-
per concentration rises up). This situation indi-
cates that dirt is basically getting into the lube oil
directly and not past the pistons and rings. The
likely sources are: leaking seals, defective breather,
damaged seal on oil filler cap or dipstick, or dirty
storage containers and/or top-up containers. Rec-
ommended action to be taken by technicians must
be that any dust that is in the oil will be pumped
through the oil filter before entering the bearings.
Therefore, the first step is to examine the oil filter
looking for dust contamination or bearing mater-
ial. If excessive dust is found, thoroughly check all
seals and breathers, etc. Check the oil storage con-
tainers and top-up containers for finding the source
of contamination.
In the syntax of implemented prototype tool, the
rules are:
CONTS1 SI NOT NORMAL END
WEAR_1 IF
FE NOT NORMAL or CR NOT NORMAL
or AL NOT NORMAL
WEAR_2 IF
PB NOT NORMAL or SN NOT NORMAL
or CU NOT NORMAL
CONTS2 IF CONTS1 and WEAR_1
CONTS3 IF CONTS1 and WEAR_2
SILICON_CONTAMINATION IF CONTS1
DUST_INGESTION IF CONTS2 or CONTS3
As another example, water problems can be divided
into two different sources: an external water contam-
ination or refrigerant leakage, in each case a different
FUZZY DIAGNOSIS MODULE BASED ON INTERVAL FUZZY LOGIC: OIL ANALYSIS APPLICATION
89