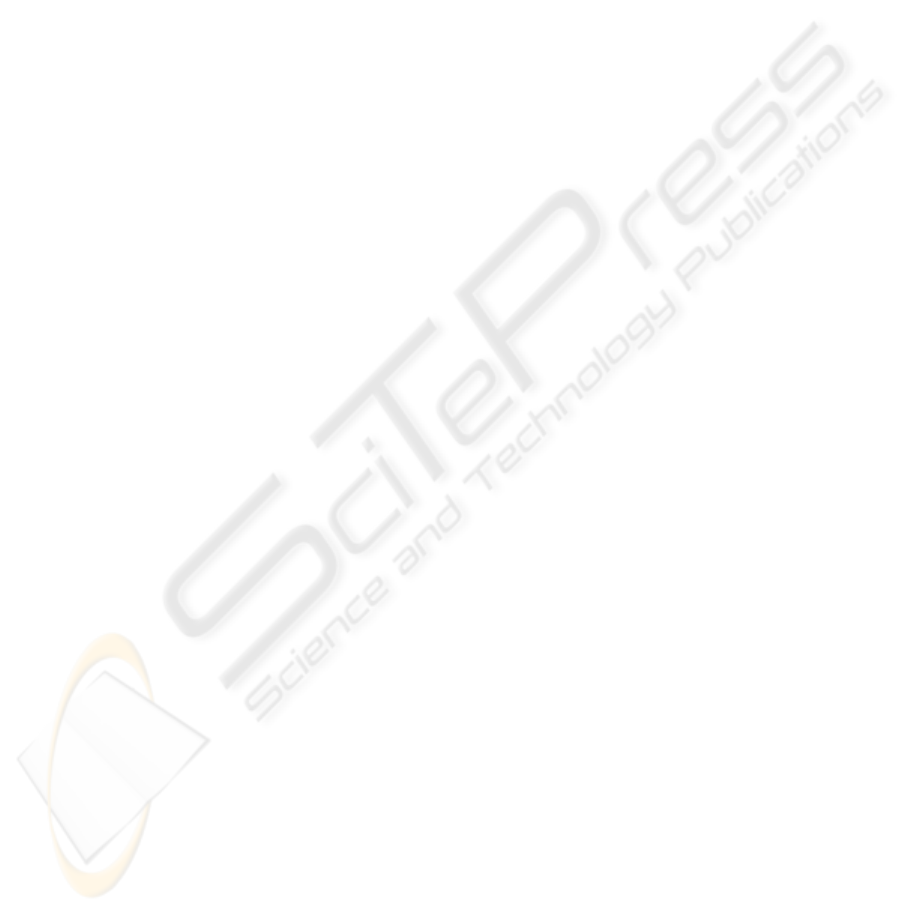
generate commands to the CCAS. Integration
between these commands and the operator
commands is resolved by an arbitrator in the UIS.
The execution platform is an on-board
embedded PC. The PC/104 bus (PC104, 2004) is a
widely used industrial standard with many
advantages, such as vibration-resistance, modularity,
mechanical robustness, small form factor (96 x 115
mm), low power consumption, etc. Moreover, it can
be easily extended with boards that provide the kind
of functions needed by robots (digital and analogue
I/O, motion control, PCMCIA expansion, etc). The
chosen OS is RTLinux (Baravanov, 1997), with
which makes it is possible to have a real-time
application running while retaining all the power of
a Linux distribution (though with some restrictions)
underneath.
6 CONCLUSIONS AND FUTURE
WORKS
The use of a common architecture for a domain or
family of systems allows rapid developments and
the reuse of components. This paper has presented a
common architectural framework for the
development of teleoperated service robots control
units (ACROSET), and also two application
examples in the context of the EFTCoR project that
show the ability of ACROSET to cope with the
needs and requirements of very different systems.
The separation of the conventional functionality of
the systems (CCAS) from the intelligent behaviours
greatly facilitates the addition of new functionalities
and the maintenance of applications. The main
drawback is the lack of language support for
expressing a component-oriented style of
programming.
ACKNOWLEDGMENTS
The DSIE wishes to thank the Spanish Government
(CICYT) and the Regional Government of Murcia
(Seneca Programmes) for their support: TIC2003-
07804-C05-02 and PB/5/FS/02.
REFERENCES
Barabanov M.. "A Linux-based Real-Time Operating
System". Master Thesis, New Mexico Institute of
Mining and Technology, Socorro, New Mexico, June
1997.
Bruyninckx, H., Konincks, B. and Soetens, P., “A
Software Framework for Advanced Motion Control”,
Dpt. of Mechanical Engineering, K.U. Leuven.
OROCOS project inside EURON. Belgium. February
2002. Retrieved October 12, 2003 from
http://www.orocos.org
Coste-Manière, E. and Simmons, R., “Architecture, the
Backbone of Robotic System”, Proc. of the 2000
IEEE International Conference on Robotics &
Automation, San Francisco, April 2000.
EFTCoR - Environmental Friendly and Cost-Effective
Technology for Coating Removal. V Framework
Program GROWTH G3RD-CT-00794. 2002-2005
Gamma E., Helm R., Johnson R., Vlissides J., “Design
Patterns: Elements of Reusable Object Oriented
Software”, Addison Wesley, Reading Mass. 1995.
Hofmeister, C. Nord, R., Soni, D., “Applied Software
Architecture”, Addison-Wesley. ISBN 0-201-32571-3.
USA. January 2000.
Iborra, A. Pastor, J.A., Álvarez, B. C. Fernández and
Fernández-Meroño J. M., “Robots in Radioactive
Environments”, IEEE Robotics and Automation
Magazine, vol. 10, no. 4, pp. 12-22, December 2003.
Nesnas, I. et al, “CLARAty: An Architecture for Reusable
Robotic Software”, Jet Propulsion Laboratory, NASA,
Carnegie Mellon University, March 2003.
Ortiz, F.J. et al “GOYA: A teleoperated system for
blasting applied to ships maintenance”. 3rd
International Conference on Climbing and Walking
Robots. CLAWAR´2000. October, 2000.
Scholl, K.U. Albiez, J. and Gassmann, B. “MCA – An
Expandable Modular Controller Architecture”,
Karlsruhe University, Germany, 2001.
Selic, B. Gullekson G., Ward P.T., “Real-Time Object-
Oriented Modeling” (ROOM). John Wiley and Sons,
New York. 1994.
SIMATIC - Working with STEP 7 5.2. ref. 6ES7810-
4CA06-8BA0. SIEMENS manuals. 2002.
PC104. Retrieved May 1, 2004, from
http://www.pc104.org
ICINCO 2005 - ROBOTICS AND AUTOMATION
328