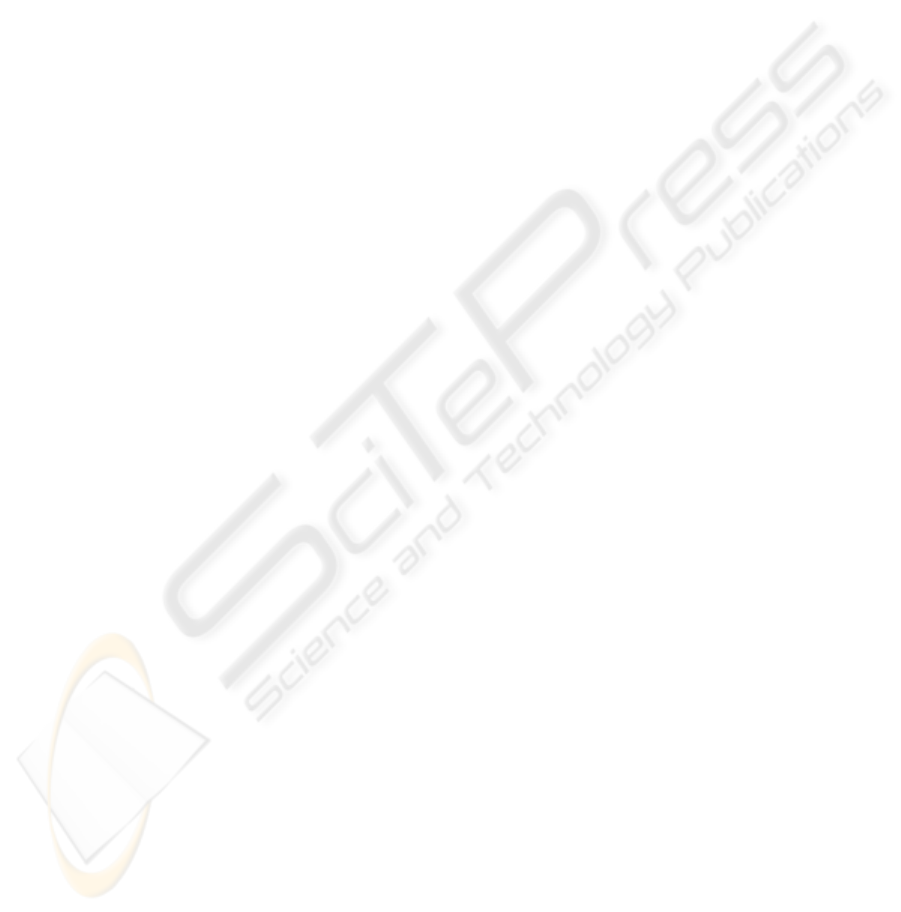
HIGHLY ACCURATE INTEGRATION OF TRACK MOTIONS
Michael Kleinkes, Angela Lilienthal, Werner Neddermeyer
University of Applied Science in Gelsenkirchen
Neidenburger Str. 43, 45897 Gelsenkirchen
Keywords:
Industrial Robots, 7
th
axis, linear track, offline programming.
Abstract:
According to the largeness of the workpieces in several industrial environments, a great number of industrial
robots is placed on external track motions, so called 7
th
axes, as for automotive or aircraft industries. Flexible
automation today requires absolute high accuracy. For example modern robotics deals with offline program-
ming, copying programs between similar working cells, reflecting programs or image processing for 3D-pose
estimation. All these tasks need absolute high accuracy and in fact, there have been many investigations for
increasing the accuracy of single robots in the past few years.
In contrast to that the use of track motions will dramatically increase the position error and badly influence
the static behaviour of the robot system. The main reasons for these additional errors are the incorrect identi-
fication of the main track direction and furthermore, very crucial, the non-linearities of the TCP (Tool Center
Point) during the robots motion on the track. This article will introduce a new method of identification and
mathematical integration of linear tracks. At first we present the method for measuring and generating profiles
of single tracks by making use of the discrete fourier transformation (DFT) and cubic spline interpolation.
Then a method for recalculating offline generated programs for real environments is presented, followed by a
method for copying programs taking two profiles of track motions into consideration. Finally some measure-
ment results are shown.
1 INTRODUCTION
Increasing demands on the flexible automation, e.g.
offline programming of robot motions or the applica-
tion of more and more complex tasks like sealing of
carbodies, require robot systems with absolute high
accuracies. In the past there was done a lot of re-
search work and investigations to increase the accu-
racy of robots by an individual identification (Denavit
and Hartenberg, 1955), (Maas, 1997) of internal para-
meters, so that robots with a high accuracy option are
available (Nitschke, 2002). From the experience the
inaccuracy of these robots is almost less than 1 mm.
In many cases of the automotive industry, the ro-
bot’s workspace is extended by external track motions
which deteriorates the accuracy of the system in a
significant manner about several millimetres or more.
This alarming fact is not compatible to the demands
on the flexible automation at all and additionally is ne-
glected by scientists and robot manufactorers as well.
Offline programming, copying or reflecting pro-
grams or 3D pose estimation requires a coordination
of the track and the robot motion, that means an inte-
gration into the robots coordinate system. The meth-
ods of measurement, identification and mathematical
integration of track motions are shown exemplary for
an ABB robot. Similar computations for other types
of robots, e.g. KUKA or FANUC, are possible as
well. Figure 1 will give you an overview of the im-
portant robot coordinate systems.
The alignment frame, as shown in figure 1, pro-
vides the connection of the track motion to the robot.
The ABB controller is computing the main track di-
rection from a frame containing quaternions (Convay
and Smith, 2003), which indicates the rotation from
the robot’s world frame to the track. It is obvious,
that the similar parameters for the track integration
have to be worked out for each type of robot, e.g.
KUKA, COMAU or FANUC. It is an essential knowl-
edge, that any type of controller unit is modelling
tracks as straight lines, where the incorrect identifi-
cation of the main track direction and - very crucial
- the non-linearities of the robot’s TCP during a mo-
tion on the track, the so called robot’s twist, are not
11
Kleinkes M., Lilienthal A. and Neddermeyer W. (2005).
HIGHLY ACCURATE INTEGRATION OF TRACK MOTIONS.
In Proceedings of the Second International Conference on Informatics in Control, Automation and Robotics - Robotics and Automation, pages 11-15
DOI: 10.5220/0001169100110015
Copyright
c
SciTePress