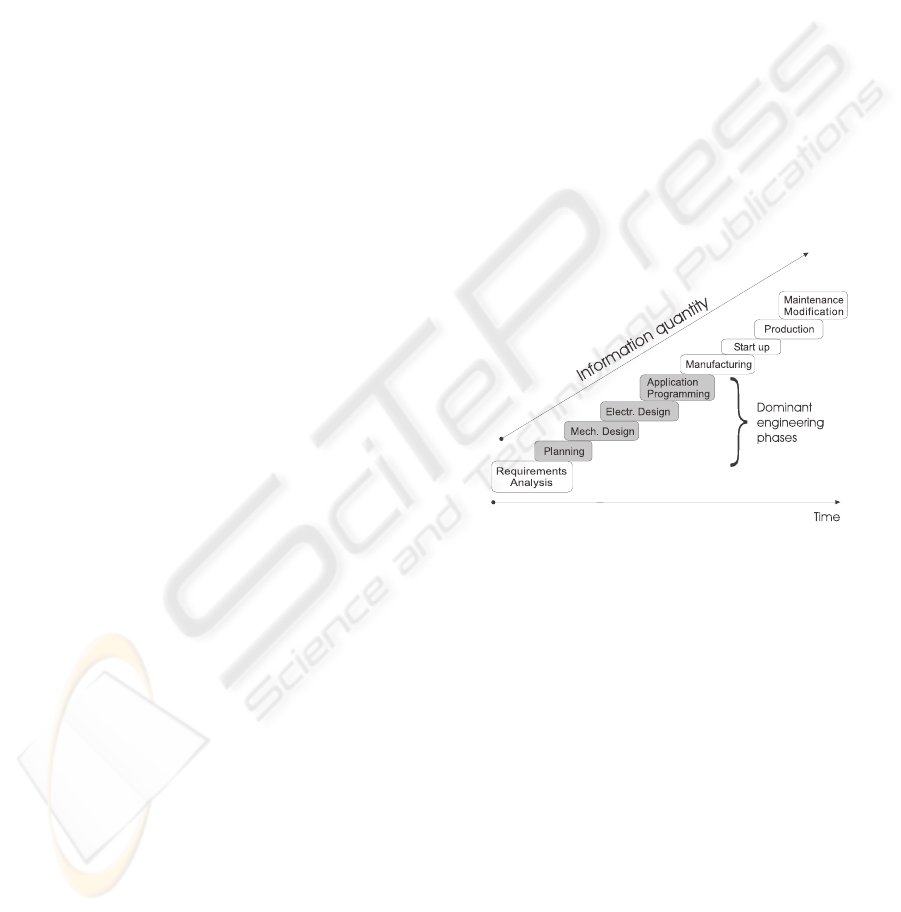
ing:
1.
Availability of the engineering data across multiple
engineering phases
A machine will be developed step by step through
the following phases: planning, mechanical design,
electric/electronic design until programming. The
engineering in each phase produces new data based
on the data of earlier engineering phases. The avail-
ability of data from earlier phases is essential to
continue the engineering sucessfully.
2.
Reuse of the phase-independent engineering data in
each phase
In the field of special purpose machine develop-
ment, engineers take advantage of standard ma-
chine components. A component in one machine
can also be used in other machines. Reusing these
standard components and their data reduces cost
and shortens developing time.
3.
Redundance-free and coherent data modelling
This means that the same data should appear only
once in the data model. This facilitates the change
management and data update.
4.
Extensibility of data structure
The requirements of engineering expand from day
to day. More and more new types of engineering
data will be created and processed. Corresponding
to these new requirements, engineering tools need
to be developed and integrated with new function-
alities. The current data structures of these software
tools must have the extensibility to respond to these
changes.
In the part 2 the different data models used in spe-
cial purpose machine engineering are analyzed. At
the end this paper presents the general engineering
data model and how to improve cooperation and com-
munication between engineering software tools.
In principle a special purpose machine is regarded
as mechatronic system within the whole engineering
process. At first, it is needed to understand the essen-
tial components of a mechatronic system and the data
processed in development.
1.2 Composition of mechatronic
systems
A mechatronic system consists of three subsystems:
a mechanical subsystem, an electronic subsystem and
a subsystem of information processing. The associ-
ation between the three subsystems is the spatial ar-
ragement and the functional interaction. The spatial
arrengement is determined by the mechanical design.
The functional interaction is mainly determined by
the information processing system (Isermann, 1999;
Welp et al., 2001; Pelz, 2001).
The mechanical subsystem provides support and
guidance. The electronic subsystem records the
measurement data from sensors and sends the con-
trol data to actuators. The subsystem of informa-
tion processing controls the manufacturing process
(K
¨
ubler, 2000).
The development of these three subsystems is the
main task within the whole engineering of the mecha-
tronic system. Normally, the life cycle of a mecha-
tronic system is subdivided into the following phases:
requirements analysis, planning, mechanical design,
electric/electronic design, application programming,
manufacturing, start up, production, maintenance and
modification as illustrated in figure 1.
Each subsystem is developed within the corre-
sponding engineering phase. Additionally, each of
these phases can contain simulations to verify the
phase solution.
Figure 1: Phase definition in special purpose machine engi-
neering
In the past, the development of mechatronic sys-
tems has often been dominated by mechanical de-
sign. The design of software/electronic components
was added later. This has led to a poor development
approach (Isermann, 1996; Gausemeier et al., 2001).
Today the work flow is recursive and solutions from
earlier phases have to be taken into consideration per-
manently.
Software tools which are used in the phases of
planning, mechanical design, electric/electronic de-
sign and application programming deal with most of
the tasks in the entire engineering. They determine
also most of the engineering data. Other phases use
the engineering data from these four phases and make
rarely changes or replenishments. For this reason, the
discussion in the remaining sections will focus on the
engineering data models in these four phases.
GENERAL ENGINEERING DATA MODEL IN SPECIAL PURPOSE MACHINE ENGINEERING
349