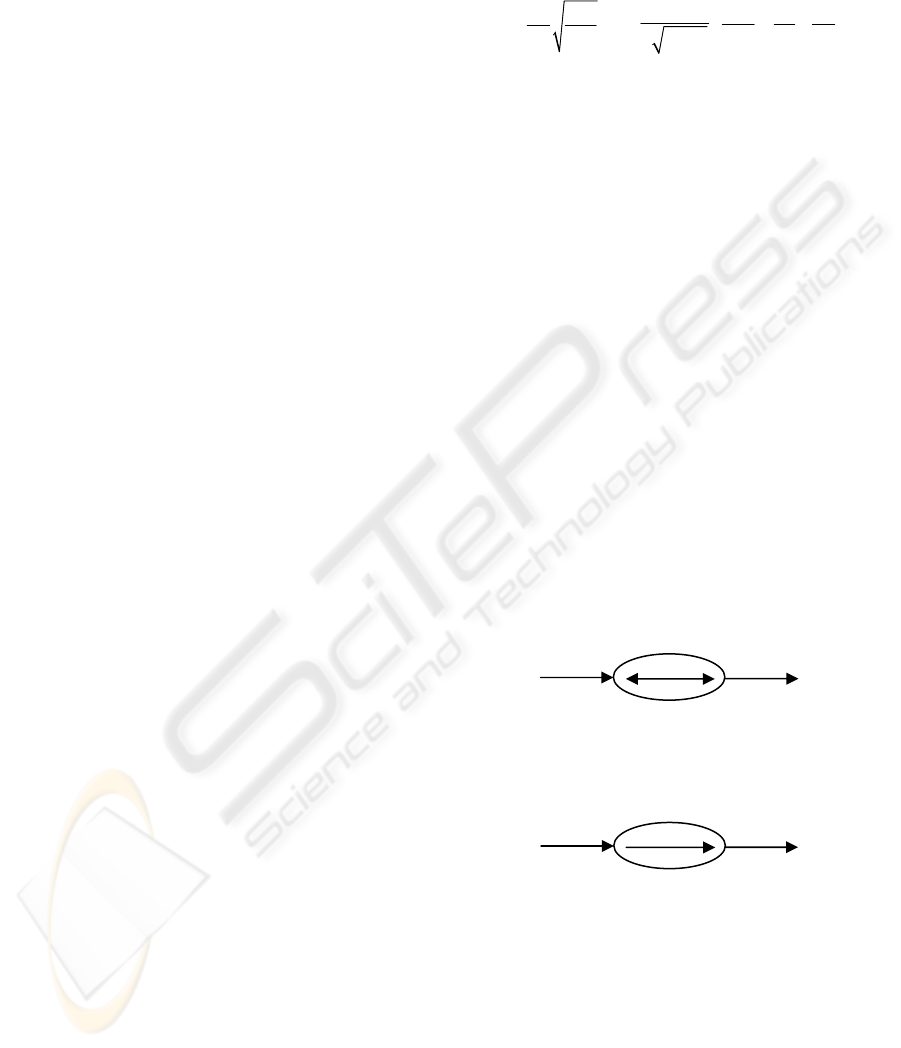
1994), (Ellis, 2000).
The Finite Elements Method is a classical tool
which enables an accurate modelling of the
dynamical behaviour of a flexible system, using a
polynomial approximation of the deformations of
elements such as beams, plates, etc... Figure 1
shows the first deformation mode due to the bending
of the vertical Z-axis during the horizontal motion of
the robot. The evolution of the other deformation
modes during the motion of the robot in its working
space is not intuitive.
Whereas this method allows the behaviour of the
robot to be understood, its complexity prevents its
use for control purposes. An alternative method to
the modelling of small deformation consists of
decomposing the structure in a set of rigid bodies
which are linked by spring elements using the
method of Assumed Modes. A model with lumped
parameters for which the stiffness of the spring
depends on the position of the load mass in the
working space allows the first deformation modes to
be represented (Meirovich, 1994). This study will be
limited to the modelling and control of the first
deformation mode, i.e. projection of the bending of
the vertical axis on the horizontal plane during the
motion of the X axis. The dynamical model of the
motion can be represented by a two-mass model
with a spring of variable stiffness.
Modal analysis can be carried experimentally
using an impulse response obtained when exciting
the effector’s end with an impact hammer (Barre,
96). The signal is recorded using a spectrum
analyser. The variation of the modal parameters for
an horizontal displacement (axis X) is moderate but
becomes very important because of torsional
coupling when both the axis X and Y are moving.
All these parameters are lumped through the value
of the Z position. According to Figure 2, the
equations of model are:
(
(
11 2 1 2 1
mx k x x a x x u=−+−+
&& & &
(1)
()
)
22 1 2 1 2
mx k x x a x x=−+−
&& & &
(2)
()
02
kk gy=+ (3)
where u is the driving effort, x
1
and x
2
are
respectively the positions of the motor and the load
for the horizontal X axis, y
2
is the position of the
load for the transverse Y axis, m
1
and m
2
are
respectively the modal masses of the motor and the
load part, k is the modal stiffness. Experimental
results show that g(y
2
)=a.y
2
+b.
Consider an horizontal displacement, for which
y
2
-y
20
=α(x
2
-x
20
). The stiffness k is now a linear
function of the load position x
2
, with k=k
0
+aα(x
2
-
x
20
)+b+ay
20
.
The frequency of the main deformation mode
and the corresponding damping ratio are given:
1
2
n
eq
k
F
π
=
,
2
eq
A
kM
ς
=
,
12
111
eq
mm
=+
(4)
3 ACCELERATION FEEDBACK
As discussed previously, the motor part can be
controlled in closed-loop whereas the load is
controlled in open-loop. Two control methods can
be employed, depending on the specifications that
are required by the user. As an example, one may
want to improve the cycle time while others want to
reduce the load’s vibrations to an acceptable level.
3.1 Tracking of the Motor Reference
Position
Since the concept of causality is important in the
comprehension of the physical phenomena, we used
a tool called the Causal Ordering Graph and
introduced by Hautier (Hautier, 2004). It allows us
to represent a system with elementary objects
defined using energetic considerations. When an
object does not store any information, the causality
will be defined as external and the output will be
derived directly as a function of the input. The
relation (R) is then called rigid:
If an object stores information, the causality is
internal and the output is a function of the energetic
state of the system. In this case, the relation (R) is
called causal, both the time and initial state are the
implicit inputs:
When the model of the process is established, the
control structure is deduced by inversion of the
COG. This model being made up of causal and rigid
relations, two different solutions for the inversion
result:
In a Rigid Relation, a bijective relation C
determines a control law using direct causal
inversion.
u
u
USE OF THE COG REPRESENTATION TO CONTROL A ROBOT WITH ACCELERATION FEEDBACK
27