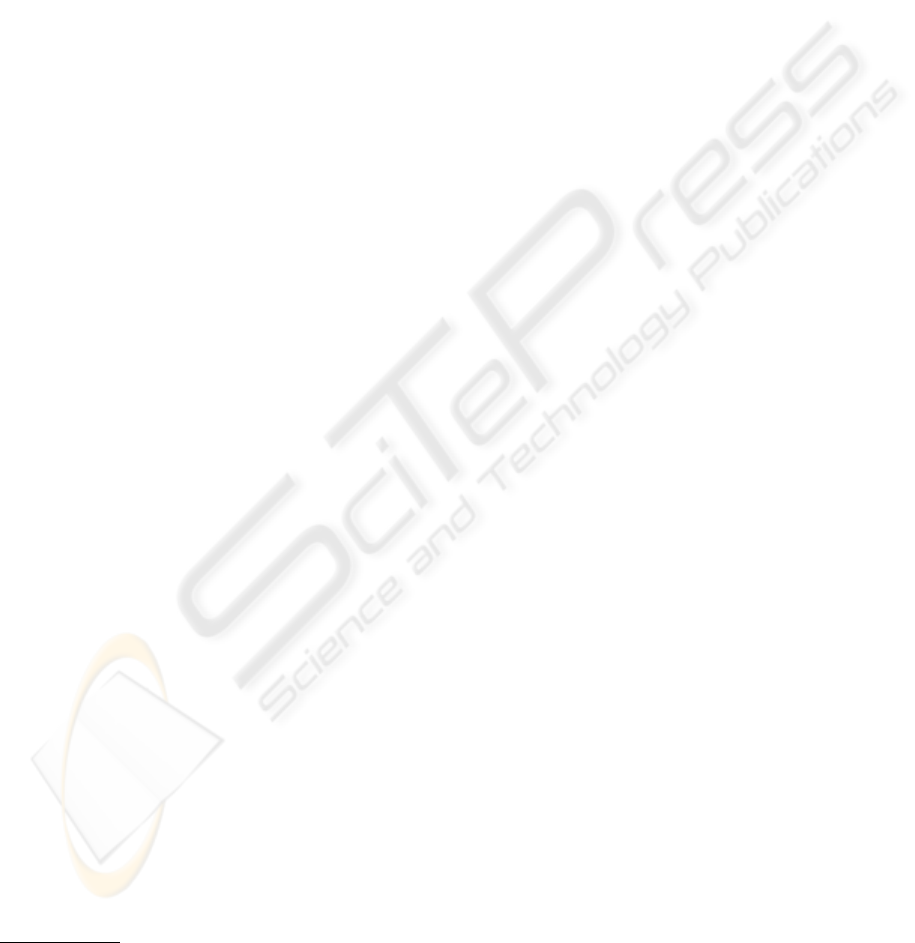
AN OPTIMAL CONTROL SCHEME FOR A DRIVING SIMULATOR
Hatem Elloumi, Marc Bordier, Nadia Ma
¨
ızi
Centre de Math
´
ematiques Appliqu
´
ees,
´
Ecole des Mines de Paris
2004 route des Lucioles, 06902 Sophia Antipolis Cedex, France
Keywords:
Driving simulation, optimal motion cueing, Gough-Stewart platform, motion perception.
Abstract:
Within the framework of driving simulation, control is a key issue to providing the driver realistic motion cues.
Visual stimulus (virtual reality scene) and inertial stimulus (platform motion) induce a self-motion illusion.
The challenge is to provide the driver with the sensations he would feel in real car maneuvering. This is an
original control problem. Indeed, the first goal is not classical path tracking but fooling the driver awareness.
Constrained workspace is the second issue classically addressed by motion cueing algorithms. The purpose
of this paper is to extend the works of Telban and Cardullo on the optimal motion cueing algorithm. A
nonlinear dynamical model of the robot is brought in. The actuator forces are directly included in the optimal
control scheme. Consequently a better (global) optimization and an advanced parametrization of the control
are achieved.
1 INTRODUCTION
Driving simulators are dedicated to the reproduction
of the behavior and environment of vehicles. They use
a motion system in order to provide drivers with the
appropriate inertial, proprioceptive and tactile motion
cues. Figure 1 shows a car cockpit mounted on a 6
degree-of-freedom parallel robot (the Gough-Stewart
platform). Figure 2 depicts the robot architecture.
A virtual reality environment is used to simulate the
road and traffic as well.
The Gough-Stewart platform is nowadays the most
common simulation platform
1
thanks to its ability to
manipulate heavy weights at high speeds, its stiffness
and its sensor accuracy. However it raises three is-
sues: the coupling between the actuators, the nonlin-
ear dynamics and the limited strokes.
The last point is, by far, the most important in the
simulation context. Indeed, examine for instance the
Renault simulator values (Reymond et al, 2000): the
robot “allows maximum displacements up to ±20cm
and ±15deg in all linear and angular axes”. Further-
more, the platform is also limited in acceleration and
1
Used by: Renault simulator, NASA Langley flight sim-
ulator, National Advanced Driving Simulator at the Iowa
University, Airbus A340 simulator, MORIS motorcycle sim-
ulator, etc.
speed: it can achieve up to ±0.5g (g=9.8s
−2
is the
gravity constant) and 0.4ms
−1
for linear motion and
300degs
−2
and 30degs
−1
for angular motion. These
values point out a high level of displacement limi-
tation. Fortunately, thanks to the immersion of the
driver in a virtual environment and the use of percep-
tual fooling it is possible to go beyond these limits,
i.e., the limited robot trajectories in the virtual sim-
ulator world can provide (up to a certain point) the
same feeling as a real car ride.
Consequently, the vehicle simulation commu-
nity (driving, flight or motorcycle) has developed
a scheme based on motion cueing algorithms (or
washout filters). The two-block diagram in the top of
figure 3 illustrates this idea. It consists in transform-
ing (filtering) the real vehicle trajectories onto robot
feasible ones. This projection takes into account both
the constrained workspace and the satisfaction of per-
ceptual validity. Then the simulator trajectories com-
puted from the washout filter are performed by the
robot thanks to a classical tracking algorithm.
The optimal motion cueing algorithm has been pro-
posed by Sivan et al 1982, later implemented by Reid
and Nahon 1985, and recently modified and imple-
mented by Telban and Cardullo (Telban et al, 1999;
Cardullo et al, 1999), (Telban and Cardullo, 2002),
(Guo et al, 2003) for flight simulators.
40
Elloumi H., Bordier M. and Mäızi N. (2005).
AN OPTIMAL CONTROL SCHEME FOR A DRIVING SIMULATOR.
In Proceedings of the Second International Conference on Informatics in Control, Automation and Robotics - Robotics and Automation, pages 40-47
DOI: 10.5220/0001178600400047
Copyright
c
SciTePress