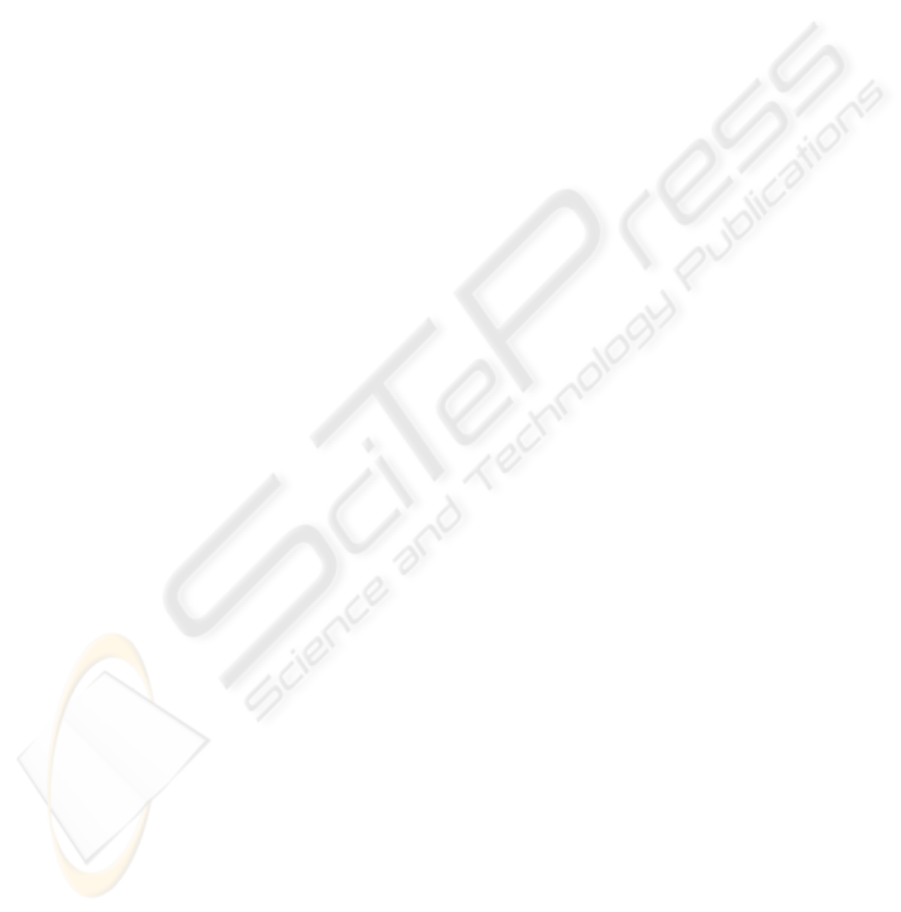
will be implemented on such networked control
systems as reliably as possible. Believing that next
to the implementation of the algorithm in the real
field conditions is the hardware-in-the-loop
simulation of the algorithm, we propose in this work
a facility for assessing the performance of the
control algorithms which involves the actual
controllers and the network that will be used in the
industrial field and a computer simulation of the
controlled process. This facility is enhanced with
generators of network traffic, so that the controller
induced traffic added to generated traffic would
allow to study the behaviour of the controller under
varying traffic loads. The traffic load imposed by the
generator simulates the load inflicted on the network
by other control applications that the same network
is used for.
The proposed test facility consists of at least
three units. The first unit is a PC-based computer
station which hosts a process simulation package
such as MATLAB (Math Works, 1996), interfaces
and links to an industrial network, such as FMS
Profibus (DIN, 1992, Tovar, 1999a). It also has the
necessary software that allows the transfer of data
between the controllers and the process simulation
package. The second unit is a PC-based station of
the network which simulates the traffic load of the
control applications. The third unit is another PC-
based network station that implements the algorithm
that controls the simulated plant. This facility is
scalable and can be expanded to accommodate
additional network stations that will implement the
control of other variables of the simulated plant.
Although the FMS protocol has functions and
services that are more than those required for the
pure automatic control of process variables, this
protocol has been selected as the protocol of the
first attempt to build a test-bed because it can
include traffic that is related with the functions of
the supervisory and process operations control.
These functions are an integral part of the operation
of any industrial complex and in small plants using
different Profibus protocols for the pure automatic
control and the higher level functions increases the
development and running cost. Therefore, this test
bed may be used to evaluate a mixture of higher and
low level control operations and its use is mainly
addressed to the case of the small process plant.
In this work a realization of the above test-bed
concept has been made and is presented. In this
realization the proposed test facility has been
expanded to include a fourth station that monitors
the network operation and realizes the supervisory
and monitoring functions of the plant simulation.
How these facilities can be used to assess the
performance of an algorithm on a networked control
system is demonstrated by realizing the LQC
networked control of two loops of a cement milling
circuit with the FMS Profibus protocol. Various
network parameters are adjusted and the use of the
developed test-bed to evaluate the performance of
the considered LQC control algorithm was studied
under a specific network traffic. This demonstration
shows the possible use of the test-bed to checking
whether a control algorithm can be implemented in
an existing networked control system without
driving the system to instability. Also, it shows how
one can tune the network to accommodate the
insertion of the new algorithm.
2 THE PROFIBUS INDUSTRIAL
NETWORK
Vendor-independent standardized networks for
control, supporting the open system concept, have
emerged over the last years. Profibus is one of the
available standards that have been approved by
CENELEC (EN, 1996). Numerous Profibus
installations have been reported. The Profibus MAC
protocol is a simplified version of the timed-token-
bus protocol (IEEE, 1985, Tovar and Vasques,
1999b). According to this protocol master stations of
the network get the bus access when a data object
called token is passed to them. During operation of
the network the station with the token transmits data
frames until it runs out of data frames or the time it
has held the token reaches a limit. Actually there are
two types of frames that are transmitted. The
synchronous and the asynchronous ones. The
synchronous ones correspond to critical data that
must be transmitted within the holding time of the
token. The Profibus protocol allows one
synchronous package per token holding time to be
transmitted and if time is left the asynchronous
transmission is initiated and is terminated even if
that requires the violation of the holding time limit
of the token.
The time delay of a message is defined as the
difference between the time when the source node
begins the process of sending a message and the
time when the destination node completes reception
of this message. This time delay must be less than
the target rotation time, a network timing parameter
that can be set by the user and expresses the time
elapsed between two consecutive receptions of the
token by the network station. A dominant part of the
TESTBED EVALUATION OF NETWORKED CONTROL SYSTEMS
117