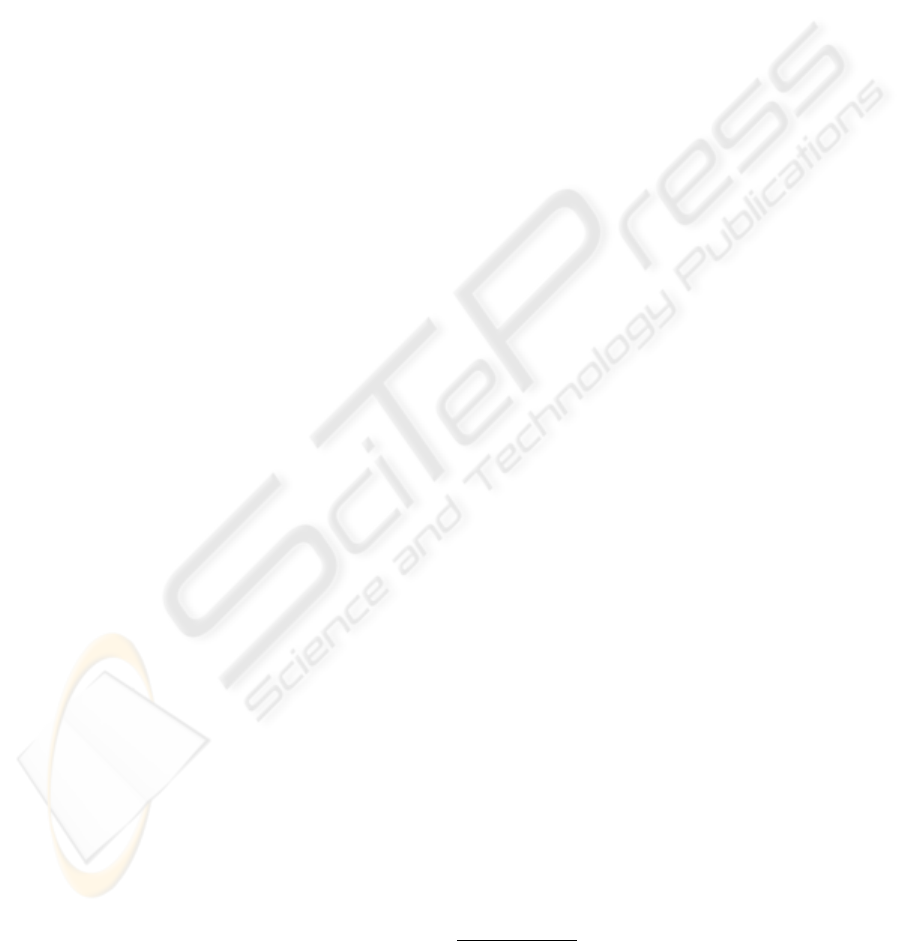
IDENTIFICATION OF A CAR-LIKE VEHICLE via MODULATING
FUNCTIONS
Davide Corsanini
Department of Electrical Systems and Automation, University of Pisa
Via Diotisalvi 2, 56126 Pisa, Italy
Fabrizio Tocchini
Department of Electrical Systems and Automation, University of Pisa
Via Diotisalvi 2, 56126 Pisa, Italy
Keywords:
Modulating functions, uncertain systems modelling, car-like vehicle, online identification.
Abstract:
This paper describes an interesting application of the modulating functions technique to model identification
of a car-like vehicle that has to face various types of surface. Several models have been obtained in different
operating conditions. The construction of a ‘mean model’ will make possible the design of a robust control
for unmanned guidance purposes. An alternative control strategy based on adaptive methods is also suggested
by means of an online implementation of the technique.
1 INTRODUCTION
In model identification literature, the modulating
functions technique plays a very important role. Sev-
eral published works have shown excellent results as
for the characterization of linear models, see (Shin-
brot, 1957) or (Balestrino et al., 2003). Recently,
an appealing application has involved the character-
ization of various classes of nonlinear models, see
for example (Pearson, 1992). In (Balestrino et al.,
2000) a very useful adaptation of the method is pro-
vided for the identification of systems with an un-
known delay. In general, the most frequently inves-
tigated fields are model identification of electrical en-
gines (Daniel-Berhet and Unbehauen, 1996), switch-
ing converters (Balestrino et al., 2003) and robot com-
ponents (Daniel-Berhet and Unbehauen, 1997).
The aim of this work is the application of such
technique to model identification of a car-like vehi-
cle, that has to face several types of surface (dry and
wet asphalt, dry and wet grass) and different operat-
ing conditions (presence or absence of a person on
board). Various linear models are then derived in the
above-mentioned conditions and a satisfying fitting of
real data is consequently obtained. We are also go-
ing to provide a comparison between the estimation
errors of the original model supplied by the manufac-
turer and the model deduced from the identification
process.
The further step will be the design of a control law
for the unmanned guidance of the vehicle. The com-
putation of a ”mean model” will allow us to set the
problem of the controller’s design in terms of robust
control problem.
Last, the possibility of an online identification is
presented. In this way an adaptive control strategy
can be implemented.
This paper is organized as follows: in Section 2
the vehicle and the manufacturer’s model; in section
3 the modulating functions method is reviewed and
the identified models in different conditions are com-
puted; in section 4 the mean model is derived and
the control problem is formulated; in Section 5 on-
line identification is presented and, in Section 6 some
conclusions are reported.
2 THE CAR-LIKE VEHICLE
The vehicle
1
has been originally conceived as a caddy
vehicle for golf courses (see Figure 1). It is a three
wheels vehicle equipped with a DC motor supplied
with two 12 volt batteries; the two back wheels are
for the traction, the wheel in the front is for the di-
rection. Our final goal is the realization of an un-
manned guidance; for this purpose the caddy has been
equiped with a linear actuator
2
for the steering, and
1
By courtesy of Bestkart S.N.C., Pionca di Vigonza
(Padova), Italy.
2
By courtesy of Ognibene Elettromeccanica Srl,
Bologna, Italy.
211
Corsanini D. and Tocchini F. (2005).
IDENTIFICATION OF A CAR-LIKE VEHICLE via MODULATING FUNCTIONS.
In Proceedings of the Second International Conference on Informatics in Control, Automation and Robotics - Signal Processing, Systems Modeling and
Control, pages 211-217
DOI: 10.5220/0001181802110217
Copyright
c
SciTePress