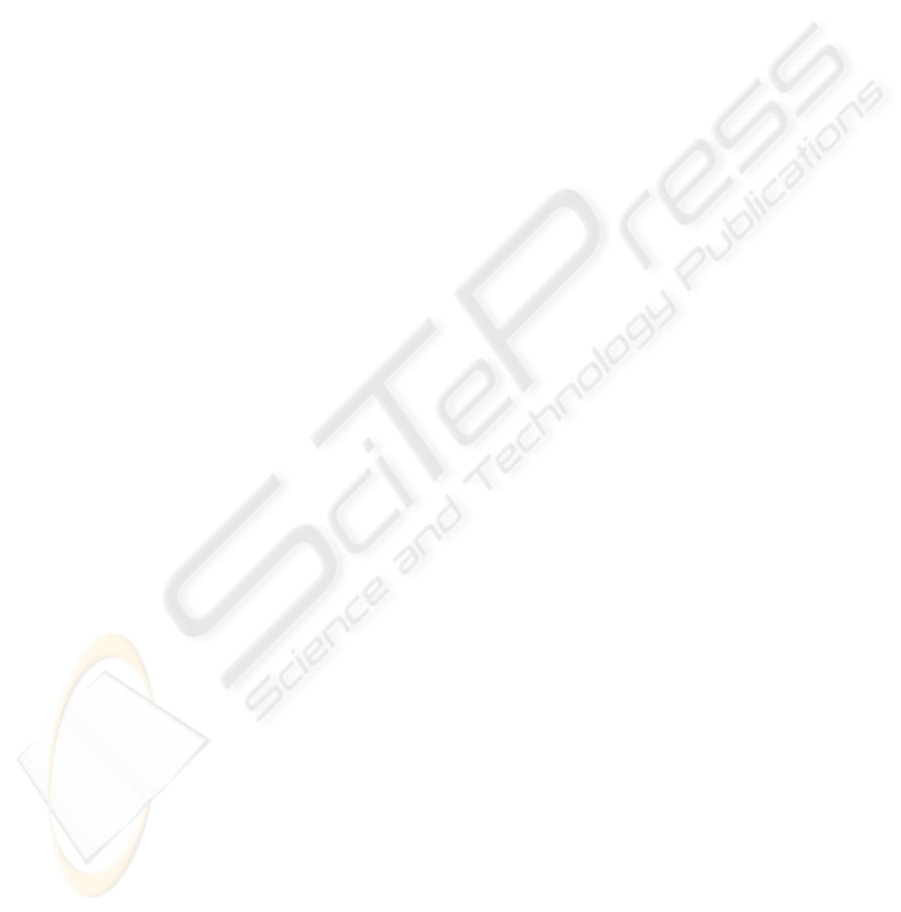
Neural Network Modeling for ALSTOM Gasifier
Armando Rivadeneyra Bardales
1
, Danilo Soares Barboza
2
, William Ipanaqué
1
,
Martin Flores
1
1
Universidad de Piura, Piura-Perú
2
Universidad de Santa Catarina, Brasil
Abstract. Neural Network Model Based Predictive Control (MPC) has become
a good choice of control strategy in many cases especially in the process
industry because it could face non linearities and cross coupling variables [6],
being modeling the first step to achieve this end. The model of a gasifier,
provided by ALSTOM Power Technology Centre, is of an industrial standard
and has been validated against a set of real data from test facilities. This makes
the challenge all the more relevant to practicing engineers. The paper sets out
the specifications and describes the design and performance of neural networks
modeling and presents a neural network approach to model the ALSTOM
Benchmark Challenge gasifier. This is a complex non-linear process, with a
high degree of cross coupling of the variables, manual control is difficult.
1 Introduction
Power generation is responsible for a significant part of the total emissions of solid,
liquid and gaseous pollutants all around the world. Due to a predicted higher long-
term availability of solid fuels, in particular coal, compared to oil and natural gas,
solid fuels will play an important part in future energy supply.
As a result of this, Integrated Gasification Combined Cycle (IGCC) power plants,
combining gasification with a gas and steam cycle, are being developed around the
world.
Low emission power generation techniques are being developed around the world
to provide environmentally clean and efficient power. To this scope, ALSTOM has
carried out researches on the combustion of pulverized coal using an Integrated
Gasification Combined Cycle (IGCC) power plant.
The operation of this Pilot Integrated plant (PIP) is based upon the Air Blown
Gasification Cycle (ABGC). First, limestone is added to the pulverized coal to
minimize sulphur originated from the coal.
Then, the mixture is fluidized in a stream of air and steam and conveyed into the
gasifier. As a result, a low calorific value fuel gas is produced by the reaction between
the air and steam and the carbon and volatiles from the coal. The limestone, ash and
unreacted carbon are removed as bed material from the base of the gasifier or
elutriated to avoid carrying it out of the top of the gasifier as fines with the product
gas.
Rivadeneyra Bardales A., Soares Barboza D., Ipanaqué W. and Flores M. (2005).
Neural Network Modeling for ALSTOM Gasifier.
In Proceedings of the 1st International Workshop on Artificial Neural Networks and Intelligent Information Processing, pages 94-102
DOI: 10.5220/0001182600940102
Copyright
c
SciTePress