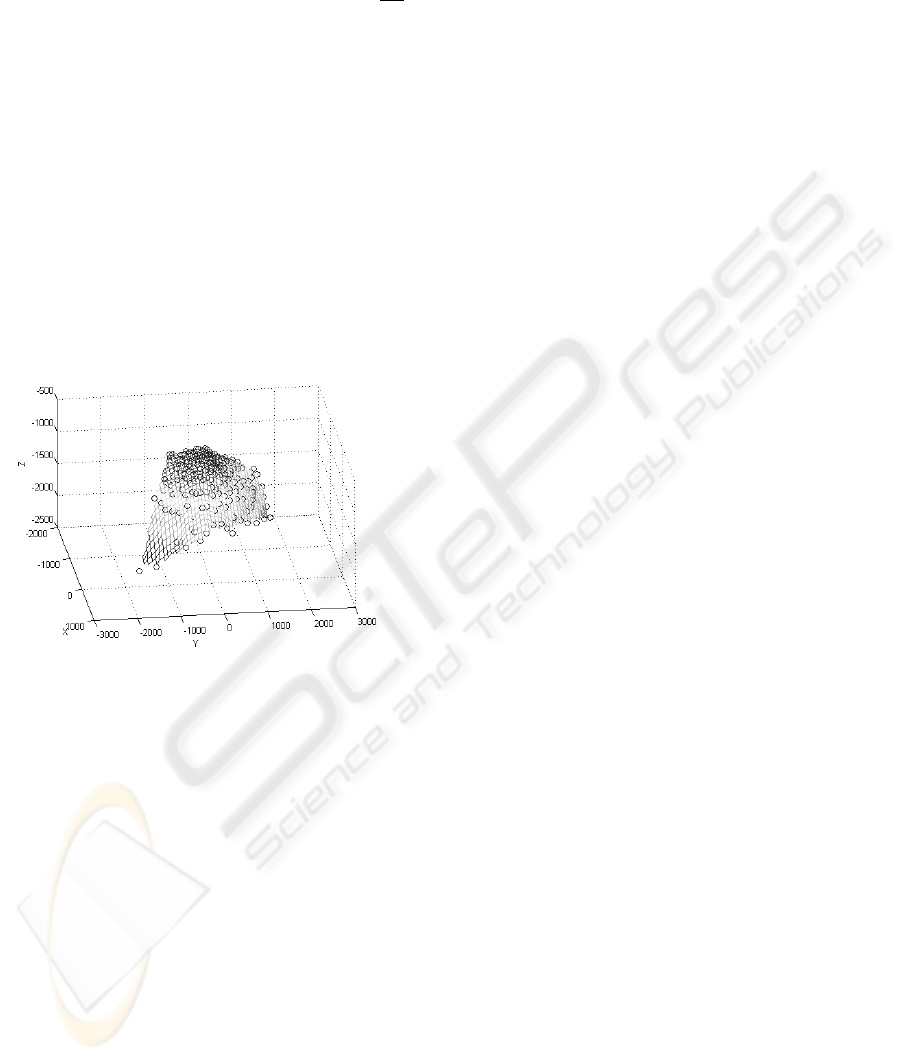
640 × 480, RGB-color, progressivescan sensor have
been implemented. Standard wide angle lenses with a
focal length of 4.8 mm were attached. The De Hough
space has computed with a resolution of ∆ϕ =
π
100
.
The R
DH
axis has been mapped on to 255 values.
Good results for stereovision preprocessing could be
obtained using a 40 × 40 kernel for h
hp
. The match-
ing point procedure has been computed within a range
of 120 × 120 pixels around the designated point P
Li
.
The application will be implemented in C/C++ run-
ning on a standard office PC with a 3GHz Pentium 4
processor using Windows 2000. With the functions
of image segmentation that are already implemented
on the target system we obtain a effective update rate
F
upd
≥ 1Hz. The turnaround time of the modules
of stereo vision still implemented in matlab m-code
falls below 40 seconds. If FILLED is implemented
completely on the target system we expect an overall
update rate of F
upd
≥ 0.1Hz.
Figure 4: 3D Model of the freight heap
Figure 4 shows the 3D model of the bulk freight
heap. This dataset was derived from the car shown
in figure 3 as the result of the stereovision analysis.
The surface is reconstructed with regard to the camera
coordinate system. The axis are scaled in milimeters.
4 CONCLUSION
This work introduces a novel sensoring approach to
measure the fill level of agricultural bulk freight. We
believe that the general procedure used in the present
FILLED prototype can adequately adapted to work
with most kinds of bulk freight, and that an assign-
ment of FILLED for many types of transport devices
and for different materials would become feasible. A
further ongoing research on shape from X methods
investigates the possibility of using just a single cam-
era instead of a stereo vision combination. Moreover
usage of a calibrated camera system will provide the
possibility to measure the overloaded volume. Al-
though it becomes obvious that this could be a prac-
tical method of fill level measurement, there are still
problems to be solved. With regard to the speed of
filling - in our case the harvester processed aproxi-
mately 150 tonns per hour - an update rate of 0.1Hz
would be hardly enough for controlled loading. How-
ever tests evidenced that it is possible to follow the
filling process. An optimization of the implementa-
tion of the mathematical processes as well as the us-
age of specific hardware for array mathematic could
be an approach to increase the measurement speed.
Due to the fact that no reliable online calibration
method could be implemented yet, the state of the cal-
ibrated optical system must not changed during mea-
surement. This inhibits the usage of autofocus objec-
tives or objectives which provide a variable magnifi-
cation. Using the inline calibration algorithm men-
tioned before requires initialization runs from time to
time to ensure that the epipolar system data are valid.
This means that the overloadprocess has to be inter-
rupted, which is unfavoured for economical reasons.
We think that online calibration methods such as the
eight point algorithm (P.H.S. Torr, 2004) could be a
possible solution for this problem.
ACKNOWLEDGMENT
The authors would like to thank the DFG (German
Research Foundation) for their financial support of
this project.
REFERENCES
Canny, J. (Nov 1986). A Computational Approach to Edge
Detection. IEEE Transactions on Pattern Analysis and
Machine Intellegence, Vol 8, No 6.
Emanuele Trucco, A. V. (1998). Introductory Techniques
for 3-D Computer Vision. Prentice Hall (25. Mrz
1998).
Jon Orwant, Jarkko Hietaniemi, J. M. D. (April 2000). Al-
gorithmen mit Perl. ISBN 3-89721-141-6, 1. Auflage.
P.H.S. Torr, A. F. (2004). Invariant Fitting of Two View
Geometry or In Defiance of the eight point algorithm.
IEEE Transactions on Pattern Analysis and Machine
Intellegence, 26(5), pages 648-651.
Will Schroeder, Ken Martin, B. L. (2003). VTK Toolkit 3rd
Edition An Object-Oriented Approach To 3D Graph-
ics. ISBN 1-930934-12-2, Kitware.
ICINCO 2005 - ROBOTICS AND AUTOMATION
442