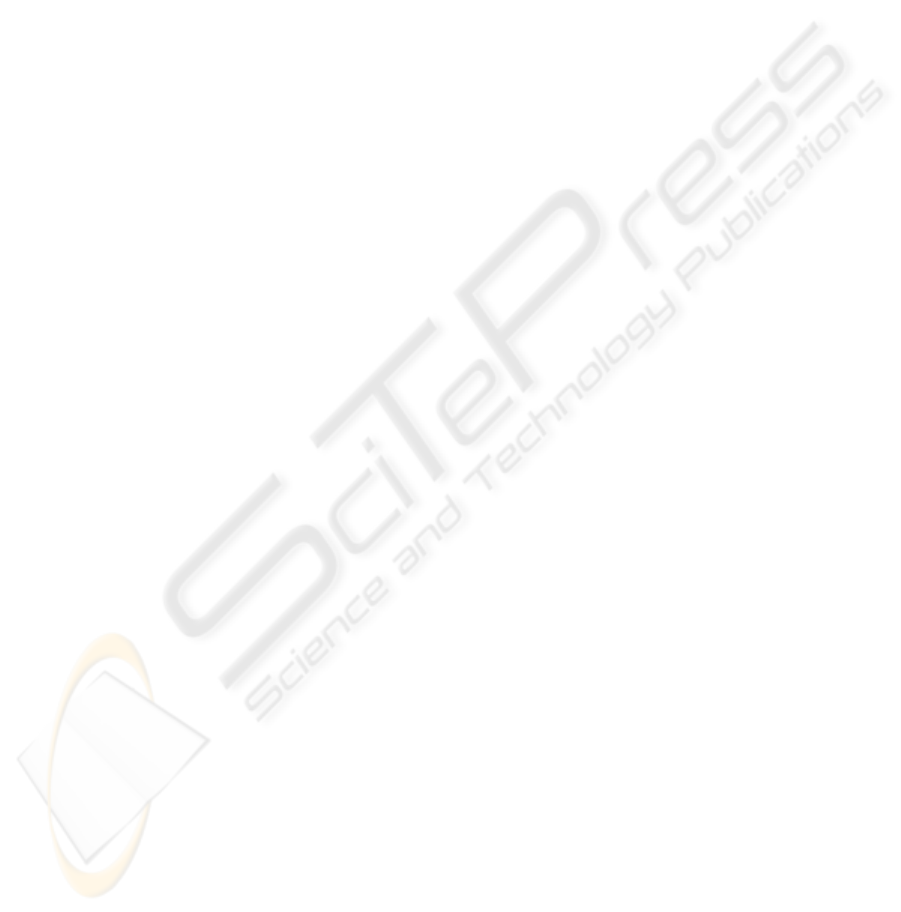
synchronisation (Hu Y., 1998). A simulated brain
wave pattern of slow wave sleep was coupled from
the coil to cat’s brain, in order to induce the
encephalic electrical activity to synchronise
gradually with the external low-frequency magnetic
fields and thus induce sleep in the cat.
An interesting study, led by Cook and Persinger,
conducted an investigation to find any interaction
with and to control the EM correlates of
consciousness generated by the brain through
applied complex magnetic fields whose
characteristics simulated natural, transcerebral EMFs
(Cook C. 1999). They designed a device to produce
rotational, circumcerebral transient magnetic fields
between 5 and 10µT, using 8 solenoids, which were
arranged circumcerebrally (every 45°) at the level of
the temporal-orbital plane. There were two
conditions utilised for this experiment: clockwise or
counter-clockwise arrangement of the 8 solenoids.
For the clockwise condition, solenoid 1 was placed
over the right prefrontal region such that solenoids
1-4 were equally spaced (45°) over the right
hemisphere and solenoids 5-8 were equally spaced
over the left hemisphere, along the orbito-temporal
plane. For the counter-clockwise condition, solenoid
1 was placed over the left prefrontal region such that
solenoids 1-4 were placed over the left hemisphere
and solenoids 5-8 were placed over the right
hemisphere. The counter-clockwise arrangement
generated a field sequence that moved in a rostral to
caudal direction along the left hemisphere but in a
caudal to rostral direction along the right
hemisphere. The frequency characteristics employed
burst-firing and frequency modulated “Thomas
pattern” (Thomas A.W, 1997).
They concluded that during the counter-clockwise
rotations, the conscious awareness, as inferred by
perception of time intervals, involved a process that
may be recreated approximately every 20-25ms and
may be affected by the right hemispheric activity.
The design of the rotational eight solenoid system
with pulsed magnetic fields has led to undertake
design and develop an automated system that would
localise a single solenoid to any head region (EEG
electrode position) and apply a sinusoidal magnetic
field to it in order to investigate any changes in EEG
activity.
2 DESIGN PROCESS
In the project, there has been several functional
system attributes mentioned that the system should
and may include:
• Self calibration and alignment properties.
• Scan the X and Y coordinates of the robotic arm
and record these points as origin reference.
• Ability to keep a record of all coordinates and
10-20 International EEG Electrode Placement
Scheme points for each test subject.
• Capability to analyse the information in
conjunction with measured EEG readings at
specific testing intervals.
• Utilise Bluetooth module to send and receive
data to and from PC’s microcontroller board.
There have been many different processes used in
order to complete the design and development of
this system. The design processes have therefore
been divided into three major parts: Mechanical,
Software, and Hardware processes.
2.1 Mechanical Design Process
For the mechanical design process of the robotic
arm, important structure design factors needed to be
taken into account, such as precise component
dimensions; minimisation of friction due to movable
plate movements; light-weightiness; durability; and
material of non-electromagnetic properties. In order
to minimise any induced currents onto EMF
exposure system, and maintain stable EMF level
during the experiment, a non-electromagnetic
material such as acrylic was selected.
2.2 Software Design Process
The Control Software design process was
undertaken throughout 9 versions to test and
improve acceptable software modules and reject
unsatisfactory modules. There have been six
software modules developed: Table, Move, Head,
Web, Auto-calibrate, Settings and Communication
Module.
At the initial stage of software design process,
only Table, Move and Head modules were
undertaken. The other modules were completed in
the final design process stage. The main goal of the
‘Table Module’ (TM) was to display reference
positions for sets of points located on the head that
the arm must move to. The main function of this
module was to save a current reference position of
the arm to one set of points in the table and also to
DESIGN AND DEVELOPMENT OF AUTOMATED SYSTEM FOR LOCALISED ELF MAGNETIC FIELD
STIMULATION OF THE HUMAN BRAIN
317