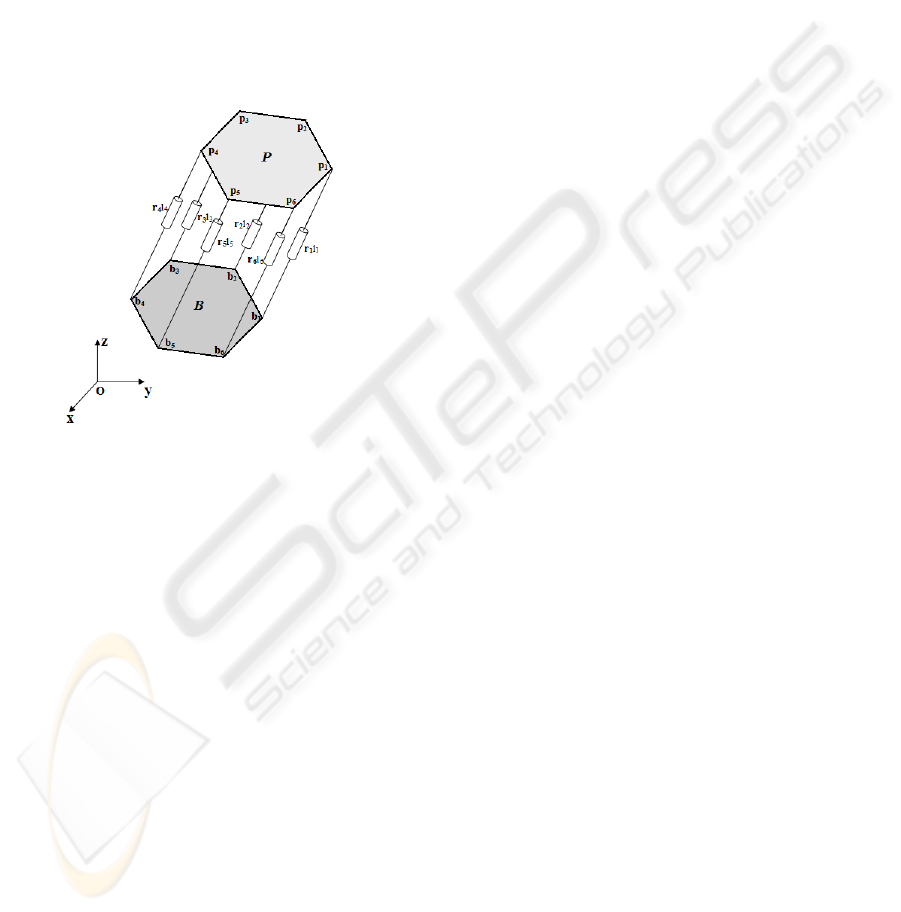
to the ground, as the base of the robot. The body
P moves according to the joint values and the kine-
matic constraints. The actuator lengths are denoted
by l
i
,i=1,...,6. The i-th actuator connects the
points b
i
and p
i
and has length l
i
.
Unlike serial manipulators, the direct kinematics of
generic parallel manipulators can not be easily writ-
ten in closed form. Numerical methods are often used
to determine the position and attitude of the P body
from the set of joint variables (the lengths of the actu-
ators).
Figure 2: A generic Stewart-Gough platform
The direct kinematics of a generic Stewart-Gough
platform has often multiple solutions. For instance,
the general Stewart-Gough platform can have 40 real
solutions, (Dietmaier, 1998). Practical applications of
direct kinematics, e.g, in robot control architectures,
often require a one to one correspondence between
subsets in the spaces of joint variables and positions
and attitudes. Therefore, a relevant aspect in the study
of the kinematics of parallel robots is related with the
ability of the kinematics solution methods to converge
to a particular solution.
Various approaches to the computation of the kine-
matics of Stewart-Gough robots have been presented
in the literature. In (Jakobovi
´
c and Budin, 2002) the
direct kinematics problem is addressed by solving six
optimization problems, one for each actuator. Algo-
rithms like Powell’s method, Hooke-Jeeves’, steep-
est descent with constant update steps and Fletcher-
Powell’s were used to solve those problems. The di-
rect kinematics is also addressed as an optimization
problem in (Hopkins, 2002), solved using a Newton-
Raphson method. The work in (Hopkins, 2002) is
integrated in a control architecture. A hybrid strat-
egy using neural networks and Newton-Raphson tech-
niques is proposed in (Parikh and Lam, 2005). In this
strategy the neural network stage is used to obtain the
initial estimate for the Newton-Raphson method. Dy-
namic modeling, a fundamental aspect for high per-
formance control, has been addressed in (Khalil and
S., 2004).
This paper presents an algorithm that describes the
motion of the P body as a rigid body transforma-
tion, i.e., through rotations and translations. Newton’s
method is used to compute the rigid body transforma-
tion matrix that corresponds to the desired solution
of the direct kinematics of Stewart-Gough platforms.
Simulation results are obtained from one special class
of Stewart-Gough platform 6-3/\
3
configuration (the
notation in (Merlet, 2000) is followed hereafter to de-
scribe the organisation of the actuators in the robot).
The direct kinematics problem is formalized as an
optimization problem and simulation results obtained
are presented.
The paper is organized as follows. Section 2 de-
scribes the direct kinematics problem (the inverse
kinematics is trivial) in the space of rigid body trans-
formations. Section 3 describes a set of simulation
experiments. Section 4 presents the conclusions of
the paper and ongoing work.
2 KINEMATICS MODELING
Table 1 details the notation used in the paper to for-
mulate the kinematics of the robot.
Table 1: Notation used in the paper
l
i
a scalar standing for the i-th
actuator length
p
i
=(p
x
i
,p
y
i
,p
z
i
) point in R
3
belonging to P
b
i
=(b
x
i
,b
y
i
,b
z
i
) point in R
3
belonging B
r
i
unit vector in R
3
¯p
i
the “usual” inclusion of p
i
in the projective space P
3
q
i
representation of point p
i
described in a local refer-
ence frame (see Figure 3)
Figure 3 illustrates relations between the coordi-
nate reference frames assigned to the rigid bodies that
form the robot.
Assuming the rigidity of the two bodies B and P ,
the kinematics of the robot is completely described by
the set of equations,
ICINCO 2005 - ROBOTICS AND AUTOMATION
94