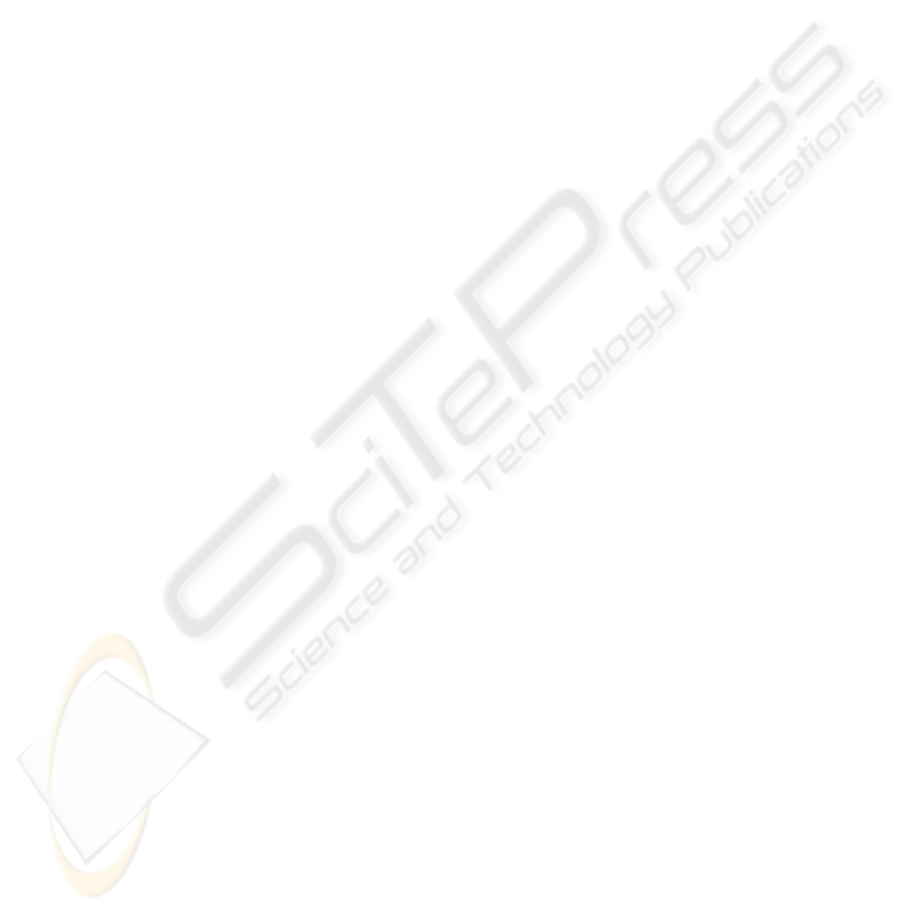
Fuzzy Controller for Flatness Based on Neural
Network Pattern-recognition
Jian-chang Liu and Zhu Wang
(School of Information Science and Endineering, Northeastern University, Shenyang
110004, China. Correspondent: Liu Jianchang,
Abstract: A pattern-recognition method for flatness defect based on CMAC
neural network is proposed, and a flatness fuzzy controller based on the
pat-
tern-recognition
results is designed in this paper. Pattern-recognition and con-
troller are designed into a single unit, in which CMAC recognizes the member-
ship grade relative to six basic modes of common flatness defect and realizes
the seeking function of the membership grade as the forepiece of the fuzzy con-
troller for flatness directly. Through analyzing the characteristics of the flatness
defect, the fuzzy set is defined reasonably, which has greatly reduced the calcu-
lation amount of fuzzy reasoning. The result of simulation shows that the pat-
tern -recognition method of flatness offers high recognizing precision, the de-
signed fuzzy controller for flatness can control the flatness defect to expected
goal fleetly and the performance of flatness control is fine
.
1 Introduction
Flatness control system is a multivariable, strong-coupling, and nonlinear control
system, for which the traditional control algorithm cannot meet the ends
[1]
. For artifi-
cial intelligence technology can deal with nonlinear and indeterminacy problems, it
has become more and more popular in practice with the development of the knowl-
edge processing technology. Recently, the artificial intelligence technology has made
good winning in the application of the flatness control [2-5].
Nowadays, Neural Network(NN) is tried in the flatness pattern recognition, which
takes the flatness defect of the measurement section along the strip width as the input
of NN and the basic pattern membership grade of the flatness defect as the output.
The input of this method is so many and the structure of the network is so complex,
that the amount of NN learning work is increased, in addition the strips with different
width need different topological structures of network, as a result the method does not
have good versatility and practicability [6,7].
A pattern-recognition controller based on CMAC neural network is proposed in this
paper. Introducing actual flatness defect and six basic mode of common flatness de-
fect, Euclidean distance of which is used to express what need to be recognized in
which CMAC recognizes the membership grades relative to six basic mode of com-
mon flatness defect and realizes the seeking function of membership grade as the
forepiece of fuzzy controller for flatness directly. The result of simulation shows that
Liu J. and Wang Z. (2005).
Fuzzy Controller for Flatness Based on Neural Network Pattern-recognition.
In Proceedings of the 1st International Workshop on Artificial Neural Networks and Intelligent Information Processing, pages 42-51
DOI: 10.5220/0001191600420051
Copyright
c
SciTePress