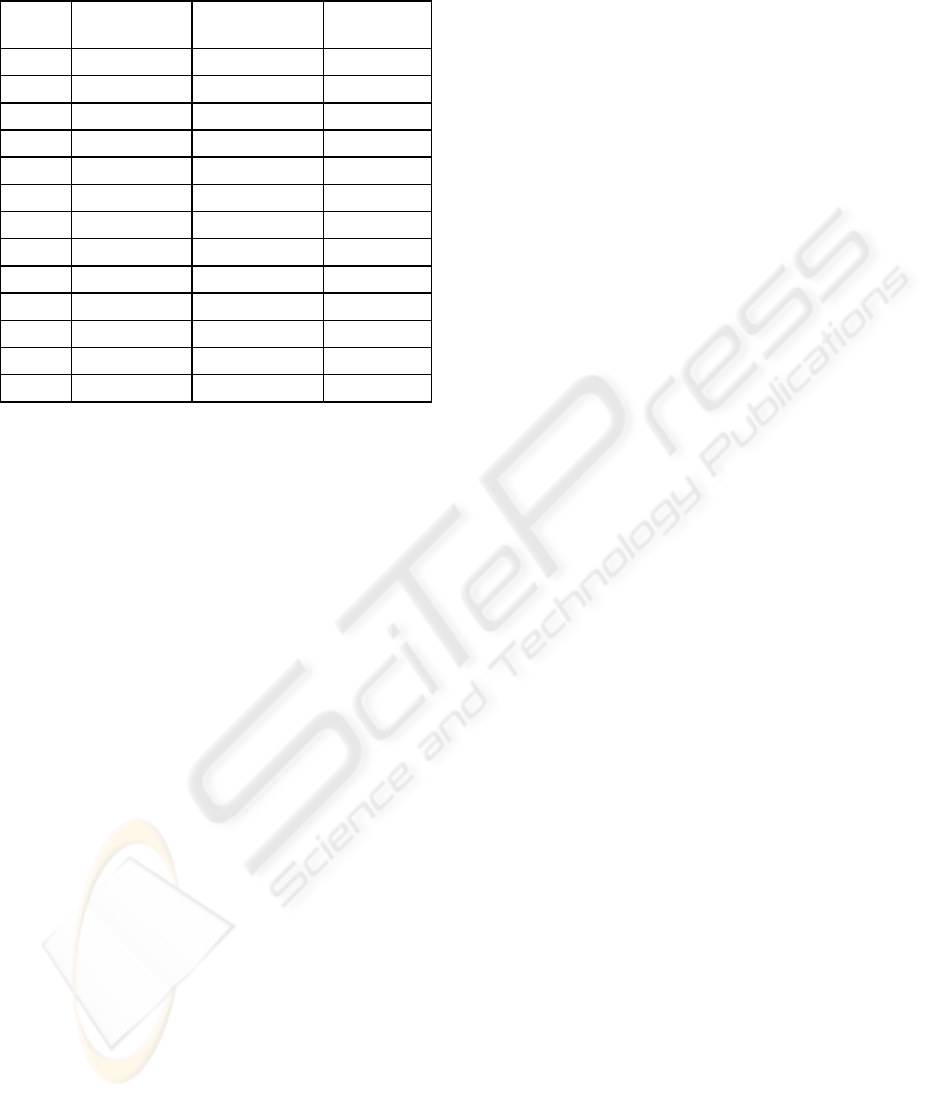
Table 6: Purchasing Orders.
Part# Vendor Delivery date Order
quantity
A SUP1 1 20
A SUP1 2 4
A SUP1 3 12
A SUP1 4 4
A SUP1 6 4
A SUP1 8 20
A SUP1 12 16
A SUP1 14 12
A SUP1 15 16
A SUP1 16 12
B SUP2 1 16
B SUP2 6 4
B SUP2 8 12
6 CONCLUSION
In order to remain competitive in the global market,
companies need to establish a well connected supply
chain to synchronize production and order decisions
in through information technology.
This study introduced an application of a
decision support model with CORBA for
synchronized sales and operations planning in a
multi-stage manufacturing environment. Our
objective was to gain insights into how real-time
order management decisions could be used to
maximize profitability while ensuring that the firm
has adequate resources to satisfy the demand. The
model interfaces in real time with enterprise-wide
planning systems to directly access financial and
plant floor machinery data for better business
planning.
The model presented considers availability and
cost of supply chain resources (including raw
material, work-in-process, finished goods inventory
and production and distribution capabilities) and
allocates these scarce resources to incoming orders
to maximize profitability. It suggests that the
synchronization of resource utilization across the
supply chain and the real-time cost of resource
information provided by the CORBA environment
can lead to more reliable order commitment and
increased profitability. By synchronizing the
organization’s cycle times with those of key
suppliers and customers, the company can order and
produce the exact quantity at the right time. The
heightened visibility and accuracy bring about more
streamlined process and greater adaptability to
changing customer requirements.
The added benefits of the real-time model
includes increased customer relationships through
fast and reliable deliveries, lower operation costs
(buying and producing only what is needed at the
right time), and increased flexibility in order
management.
REFERENCES
Bolton, F., 2002. Pure CORBA: A Code Intensive
Premium Reference, Sams Publ., Indianapolis, Ind.
Castillo, I., C. Roberts, 2001. “Real-time control and
scheduling for multi-purpose batch plants”. Computers
and Industrial Engineering, Vol. 41, pp. 211-225
Layden, J., 1994. “Real-time factory floor scheduling
enhances responsiveness”, Industrial Engineer, Vol.
26, No. 11, p. 20
O’Brien, J., K. Sivaramakrishnan, 1996. “Coordinating
order processing and production scheduling”. J. of
Management Accounting Res., Vol. 8, pp. 151-170
Ovacik, I, R. Uzsoy, 1994. “Exploiting shop floor status
information to schedule complex job shops”. Journal
of Manufacturing Systems, Vol. 13, No. 2, pp. 73-84
Pritsker, A.A.B., 1986. Introduction to Simulation and
SLAM II, Halstead Press
Sanz, R., 2003. “A CORBA-based Architecture for
Strategic Process Control”. Annual Reviews in
Control, Vol. 27, pp. 15-22
Sanz, R., M. Alonso, 2001. “CORBA for Control
Systems”. Annual Reviews in Control, Vol. 25, pp.
169-181
Singh, R., G. Gilbreath, 2002. “A real-time information
systems for multivariate statistical process control”.
International Journal of Production Economics, Vol.
75, pp. 161-172
Steele, J., Y. Son, R. Wysk, 2001. “Resource modeling for
the integration of the manufacturing enterprise”.
Journal of Manufacturing Systems, Vol. 19, No. 6, p.
407
Umble, M., E. Umble, L Deylen, 2001. “Integrating
enterprise resource planning and theory of
constraints.” Production & Inventory Management J.,
2nd Quarter, pp. 43 – 48
Vollmann, T.E., W.L. Berry, C. Whybark, 1997.
Manufacturing Planning and Control Systems,
Irwin/McGraw-Hill.
Yang, K.K., F.R. Jacobs, 1999. “Replanning the master
production schedule for capacity-constrained job
shop”. Decision Sciences, Vol. 30, No. 3, pp. 719-748
REAL-TIME SALES & OPERATIONS PLANNING WITH CORBA: Linking Demand Management with Production
Planning
129