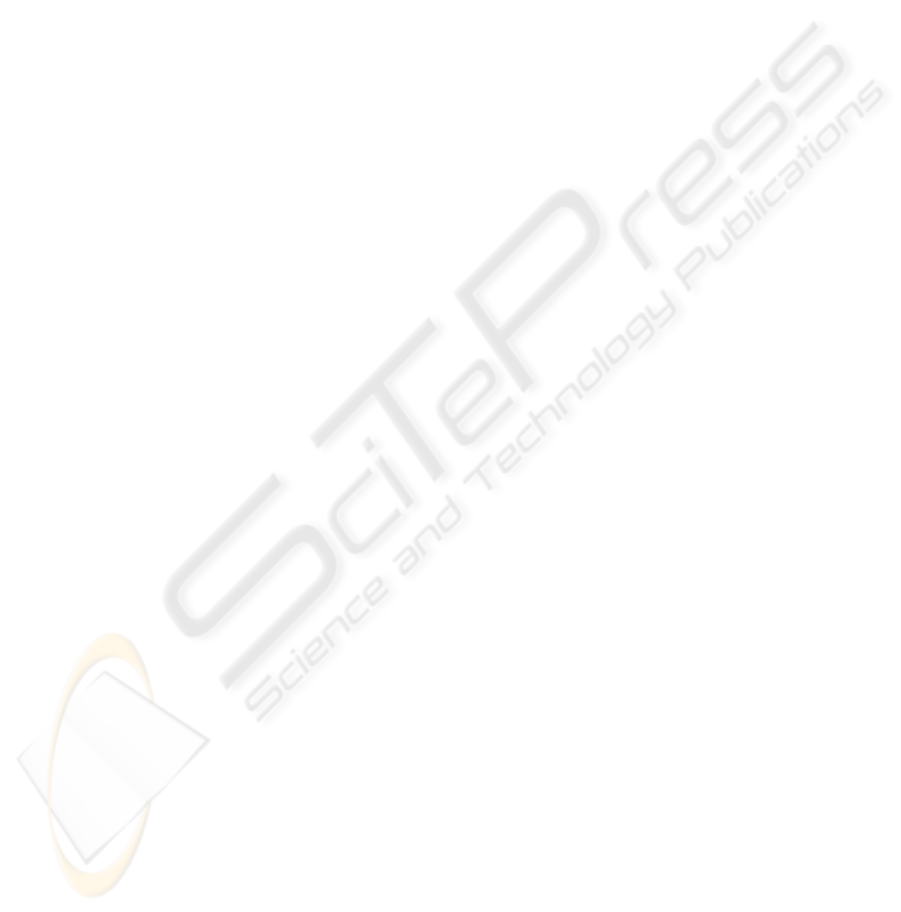
capabilities. They also have to respond to unplanned
breakdowns as part of their support mission.
The R&O planning process starts with the
equipment fleet manager supplying the R&O facility
with a list of equipments to be overhauled in the
future. Requirement’s horizon can range from
months to 10 years depending on the nature of the
projects. As part of their business and budgeting
plan, each R&O facility defines the maintenance
content to be performed and then it uses them to
determine the sequence of all activities in a project.
Based on its current capacity, the facility establishes
a maintenance program that specifies the estimated
starting and ending dates of every project and a
detailed budget.
When all the maintenance program budgets are
approved at the fleet manager level, a detailed
production plan is built by allocating the limited
pool of resources to each project. Different
production plans using different resource and
equipment levels are simulated and tested in order to
obtain a feasible plan that results in good utilization
of resources and also meets the customer’s
expectations. When the proposed plan is approved
by the customers, it is used as the master production
schedule for the next fiscal year.
3.2 R&O execution process
The R&O execution process includes the realization
of both unplanned repairs and planned
remanufacturing projects. For a typical overhaul
project, work starts with a disassembly activity. The
project content is defined as the main equipment is
inspected (Gharbi et al., 1998). The next step, the
most important in terms of workload, includes the
replacement and repair of a large number of parts
and components. At the same time, the main
structure of the equipment can be overhauled and
modified to accept the new components and the
repaired ones. The remanufacturing process then
ends with the assembly and a final inspection. Such
projects may also include paint stripping and
painting operations.
The network or routing topology of a
remanufacturing project is therefore divergent at its
start, followed by many parallel paths representing
the repair of systems or components, and converges
at the end (Gharbi et al., 1999). It is important to
note that not all MRPII or ERP systems can support
that type of work sequence and its related bill of
material (Pellerin, 1997).
The other element of complexity when executing
and controlling a repair and overhaul project resides
in the nature of each maintenance operation. The
amount of work depends on the specific condition of
the component being repaired or rebuilt. Therefore,
the exact duration of any repair is never known
before its end. The highly stochastic behavior of a
repair operation is also responsible for a high
variability in material consumption. Inventory
management for spares parts is extremely difficult in
that context. Parts usage must be planned according
to the maintenance program and based on historical
consumption data.
3.3 Integrating R&O management
process into ERP
Maintenance has always been considered as a supp:
ort function and rarely as a core enterprise process.
Consequently, most software development
companies have spent relatively little time and
efforts at integrating the maintenance processes into
their MRPII (Ip et al., 2000) or ERP applications
(Nikolopoulos et al., 2003).
Although the role of maintenance has become
more important in the last few years, most ERP
providers still position their maintenance
management system or module as an execution
system. This may be acceptable for traditional
manufacturing companies but it comes short to
satisfy all the needs of purely maintenance
organization such as a remanufacturing or an R&O
plant. These organizations need to integrate all
levels of their planning activities, from the strategic
business plan to the actual detailed maintenance
plan. This process requires planning, negotiating,
sourcing, inventory controlling, scheduling,
monitoring, quality assurance, and dispatching of the
necessary resources (Nikolopoulos et al., 2003).
They also need to be able to translate a customer
requirement into a firm order with an expected
delivery date. This is not an easy task because of
the stochastic nature of any major maintenance
request, as described earlier.
In the case of a defense R&O organization, the
management complexity increases with the length of
the planning horizon. Remanufacturing and overhaul
projects are planned at the fleet level and with
relatively few information at the equipment level.
The generic sequence of work is known with
certainty but this is not the case with the material
consumption and the work duration. In practice,
ERP applications are usually good at composing
with the changing nature of a maintenance order but
ADAPTING ERP SYSTEMS FOR SUPPORTING DEFENSE MAINTENANCE PROCESSES
295