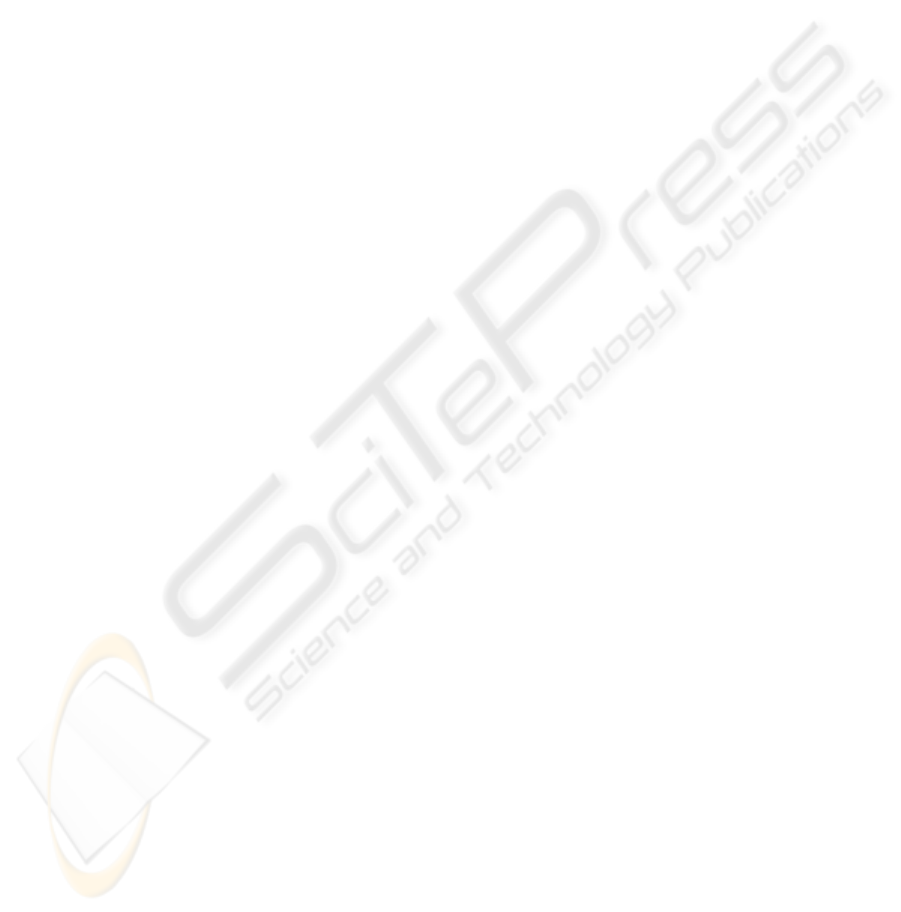
Second, the ERP systems are not capable of
handling the uncertainties and unexpected events
because the original MRP (Materials Requirement
Planning) logic is still in core. The MRP system
recognizes the differences between independent and
dependent demands. Through a simple logic and
with aid of a computer, the MRP system can
generate a list of material requirements for all the
subassemblies and components. However, the
simple logic has a couple of strong assumptions: (i)
unlimited capacity on the shop floor and (ii) non-
stochastic worldview. The capacity assumption is
addressed to some degree in the ERP system through
a feedback mechanism. Yet, the inability in handling
stochastic situations continues in the ERP systems.
Third, even though there are provisions for taking
real-time data from shop floor, the ERP system
needs additional external systems or devices such as
Manufacturing Execution System (MES) to actually
monitor and collect real-time data.
1.2 MES
The Manufacturing Execution Systems (MES)
provide up-to-the-second critical data about
production activities across the factory and supply
chain via communications networks. The MES can
assist in the decision making processes for an
enterprise by providing real time aspects of the
entire manufacturing process. The MES
accomplishes this task by guiding, initiating,
responding to, and reporting on plant activities in
real time, by using current and accurate data. The
MES can help reducing cycle times, levels of Work
in Progress (WIP), data entry time, paperwork and
scrap through the improvement in utilization of plant
capacity, process control quality, arrangement of
plant activities, tracking of orders and customer
service. (Choi 2002: Feng 2000)
The MES acts as an interface between the
planning level (ERP) and control level (shop floor)
by sending critical real time information to plant
managers. Overall it helps in integrating the entire
supply chain by bringing the shop floor closer to the
enterprise which helps the shop floor to become
more responsive to the business needs.
2 PROBLEM DEFINITION
The main objective of the research presented in this
paper is to assess and evaluate the impact of MES on
an enterprise. We start with a Null hypothesis that
the MES has no impact on the operations of the
enterprise. The alternative hypothesis is that the
MES affects the performance by optimizing the
resources. On the basis of the simulation models the
null hypothesis is tested and the comparative
performance measures are used in making the
conclusion so as to accept the null hypothesis or not.
Though we have a reasonable conjecture that real
time information will make the production system’s
operation more efficient, we want to quantify these
benefits. We analyze this impact of the MES' on an
enterprise by simulating two manufacturing systems,
one with MES capabilities and the other without
MES.
Even though performance measures can be
several including cycle time, WIP inventory,
resource utilization or others, we focused on the
production lead time in our initial study reported
here.
3 A METHODOLOGY FOR LEAD
TIME DETERMINATION
Before we begin the simulation study, we need to
address the problem of the ERP system associated
with its non-stochastic nature. Again, we focus on
the production lead time in this paper.
The lead time for a product is specified as a
fixed, deterministic number in the ERP systems.
However, the actual lead time in the shop floor
varies significantly due to the variances in individual
processing times and a queue in front of a highly
utilized workstation. Such variances are modeled in
a simulation model and their results are fed back to
the ERP system to determine the most appropriate
lead times. The procedure employs bi-directional
feedback between the non-stochastic ERP system
and the discrete event simulation model until a set of
converged lead times is determined.
3.1 The Simulation Model
The ERP systems contain much of the
manufacturing relevant data, so their databases can
serve as data depository for simulation models.
The first step involves feeding the data stored in
an ERP system to the pre-built simulation model.
The simulation model reflects a rather long-term
description of the shop floor. An interface to directly
read the data stored in the ERP database has been
designed which would result in an automated update
of the simulation model. The production data could
be read into the simulation model at specific
predefined intervals (e.g. hourly, end of the shift,
daily, etc). This enables the simulation model to
effectively simulate a near “real-time” production
ASSESSING THE IMPACT OF INTEGRATING A MES TO AN ERP SYSTEM
301