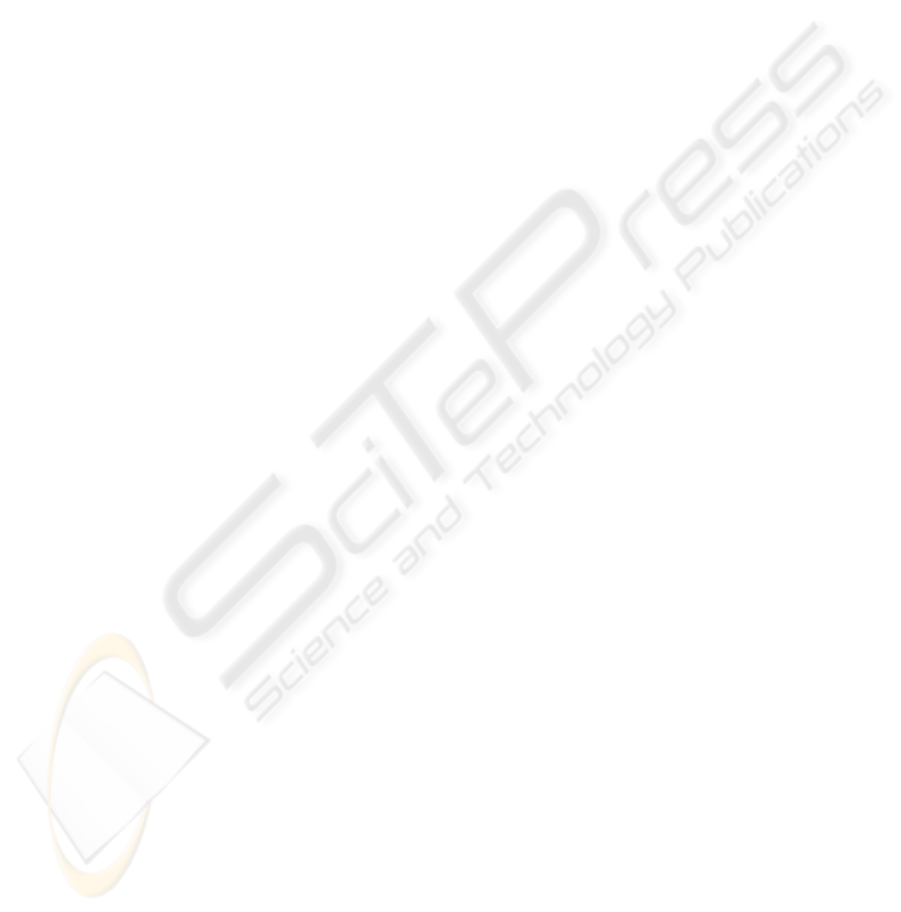
discrepancy between the estimated and actual
duration times. No changes had to be made to any
of the models in order to switch from using them for
control or simulation.
Since there is no tool that can accept a collection
of models, simulating this system with commercial
simulation software like ARENA will be impossible.
The method that is commonly used to model
distributed systems is to create a new equivalent
simulation model that is not distributed. This
however represents a considerable modeling effort.
For example, the complete modeling effort for our
system, including the models for control as well as
the simulation models, is cut by 72% over using a
conventional modeling tool. Using a conventional
tool would have resulted in a modeling effort
equivalent to writing models for 88 units where as
we only wrote 25 models, one for each of the 25
units. And this does not include the extra modeling
effort that goes into modeling the communications
among the controllers, which, for our system is
integrated into the tool and therefore represent no
additional modeling. If one wants to incorporate
simulation at different resolutions then this requires
additional modeling using a commercial tool. Our
tool provides all levels of resolution using the basic
set of models. One simply includes those models
whose logic we want represented.
7 CONCLUSIONS
The distributed simulation and control system was
successfully tested on our physical simulator of an
FMS consisting of 4 single processor machines, 1
double processor machine and an automated guided
vehicle system. For the sake of demonstration the
system used 6 independent computers to control the
hardware. Real-time simulations of the distributed
controller using our methodology were concurrently
executed using the same control models. The
simulations were initialized to the current state of
the hardware before starting. This allows the
simulations to produce future predictions.
We have shown an implementation of a tool that
along with a coordination object can simulate a
distributed system using the individual models. The
key issue for this implementation to work is our
distributed modeling methodology where each
individual simulation object is included into the
simulation program and the coordination function
coordinated the execution of each simulation object
to model the concurrent processing. The
coordination function uses its global event list to
organize the execution of the simulation object by
chronological order. The simulation objects in tern
only execute the immediate event and do not cycle.
One of the most important advantages of using
the same models for both simulation and control is
that the state definition is simply the data in the
variables of the models. This allows for the
simulation to be initialized with the current state of
the controller with only a trivial copying of the data
to a 2nd copy of the model. This solves a major
problem in control. That is, the state does not need
to be interpreted to meaningful information to
initialize a different model.
REFERENCES
Albus, J. S. and A. Meystel, 1997, “Behavior Generation
in Intelligent Systems,” National Institute of Standards
and Technology Internal Report, Gaithersburg, MD.
Albus, J. S. and A. Meystel, 1995, “A reference model
architecture for design and implementation of semiotic
control in large and complex systems” In
Architectures for Semiotic Modeling and Situation
Analysis in Large Complex Systems: Proceedings of
1995 ISIC Workshop, 33- 45, AdRem Press, Bala
Cynwyd, Pennsylvania.
Arango G., and R. Prieto-Diaz, 1991, “Domain analysis:
concepts and research directions,” Domain Analysis
and Software Systems Modeling, Los Alamitos, CA:
IEEE Computer Society Press, pp. 9-33.
Bodner D. A., S. A. Reveliotis, 1997, “Virtual factories:
an object-oriented simulation-based framework for
real-time FMS control,” Proceedings of the 6th
International Conference on Emerging Technologies
and Factory Automation, pp. 208 –213.
Davis W. J., D. Setterdahl, J. Macro, V. Izokaitis, and B.
Bauman, 1993, “Recent Advances in the Modeling,
Scheduling and Control of Flexible Automation,”
Proceedings of the 1993 Winter Simulation
Conference, pp. 143-155.
Davis W. J., 1998, “On-Line Simulation: Need and
Evolving Research Requirements,” Simulation
Handbook, J. Banks, ed., Wiley, pp. 465-516.
Gonzalez F. G., W. J. Davis, 1997,"A Simulation-Based
Controller for Distributed Discrete-Event Systems
with Application to Flexible Manufacturing,"
Proceedings of the 1997 Winter Simulation
Conference, pp. 845-853.
Gonzalez F. G., W. J. Davis, 1998a,"Initializing On-Line
Simulations From the State of a Distributed System,"
Proceedings of the 1998 Winter Simulation
Conference.
Gonzalez F. G., W. J. Davis, 1998b, "Developing a
Physical Emulator for a Flexible Manufacturing
System," Proceedings of the 1998 International
Conference on Systems, Man and Cybernetics.
ICEIS 2005 - INFORMATION SYSTEMS ANALYSIS AND SPECIFICATION
150