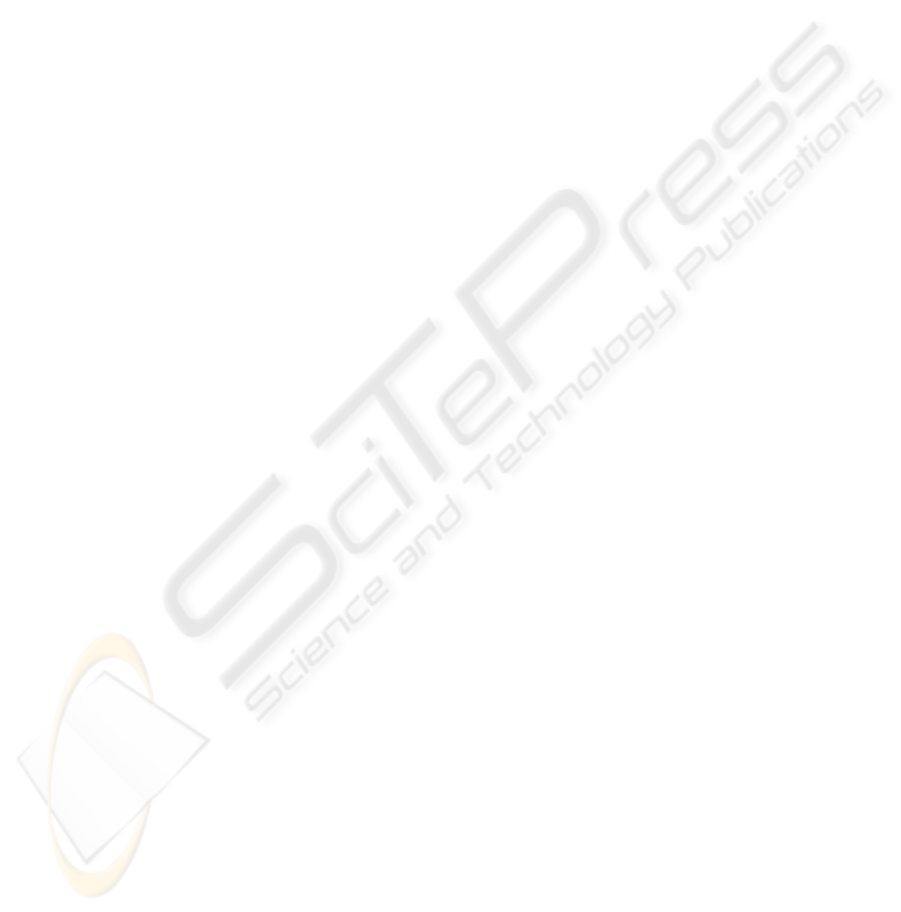
5 Conclusion
Production management data and timed Petri nets with the holding-duration principle
were used to model production activities. In production management systems the prod-
uct structure is usually given in the form of the BOM and the process structure in the
form of routings. These two groups of data items, together with the work centers as
capacity units, form the basic elements of the manufacturing process. A procedure for
using existing data from production management systems to build the Petri-net model
was developed.
The proposed method is an effective way to get an adequate model of the production
process, which can be used to develop different analyses of the treated system, e.g.
schedules. The intention of the future work is to make some additional tests of the
provided method on the real manufacturing environment.
References
1. van der Aalst, W.M.P.: Petri net based scheduling. Computing Science Report, 23 (1995)
2. van der Aalst, W.M.P.: The Application of Petri nets to Workflow Management. Journal of
Circuits Systems and Computers, 8(1), (1998) 21–66.
3. Berning, G., Brandenburg, M., G
¨
ursoy, K., Kussi, J.S., Mehta, V., T
¨
olle, F.: Integrating col-
laborative planning and supply chain optimization for the chemical process industry (I) -
methodology. Computers and Chemical Engineering, 28, (2003) 913–927.
4. Bowden, F. D. J.: A brief survey and synthesis of the roles of time in Petri nets. Mathematical
& Computer Modelling, 31, (2000) 55–68.
5. Freedman, P.: Time, Petri nets, and robotics. IEEE Transactions on Robotics and Automation,
7(4), (1991) 417–433.
6. Czerwinksi, C. S., Luh, P. B.: Scheduling products with Bills of materials using an improved
lagrangian relaxation technique. IEEE Tr. on robotics and automation, 10(2), (94) 99–111.
7. L
´
opez-Mellado, E.: Analysis of discrete event systems by simulation of timed Petri net mod-
els. Mathematics and Computers in Simulation, 61, (2002) 53–59.
8. Gu, T., Bahri. P. A.: A survey of Petri net applications in batch processes. Computers in
Industry, 47, (2002) 99–111.
9. Murata, T.: Properties, analysis and applications. Proc. of the IEEE, 77(4), (1989) 541–580.
10. Recalde, L., Silva, M., Ezpeleta, J., Teruel, E., Petri Nets and Manufacturing Systems: An
Examples-Driven Tour. In: Lectures on Concurrency and Petri Nets, Vol. 3098. Springer-
Verlag (2004), 742-788.
11. Tacconi, D. A.: A New Matrix Model for Discrete Event Systems: Application to Simulation.
Control Systems Magazine, IEEE, 17, (1997) 62–71.
12. Yeh, C.H.: Schedule based production. International Journal of Production Economics, 51,
(1997) 235–242.
13. Yu, H., Reyes, A., Cang, S., Lloyd, S.: Combined Petri net modelling and AI based heuristic
hybrid search for flexible manufacturing systems-part 1. Petri net modelling and heuristic
search. Computers & Industrial Engineering, 44, (2003) 527–543.
14. Zuberek, W. M., Kubiak, W.: Timed Petri Nets in Modeling and Analysis of simple Schedules
for Manufacturing Cells. Comp. and Mathematics with Applications, 37, (1999) 191–206.
15. Zhou, M. C., Venkatesh, K., Modelling, Simulation, and Control of Flexible Manufacturing
Systems: A Petri Net Approach (World Scientific) (1999)
38