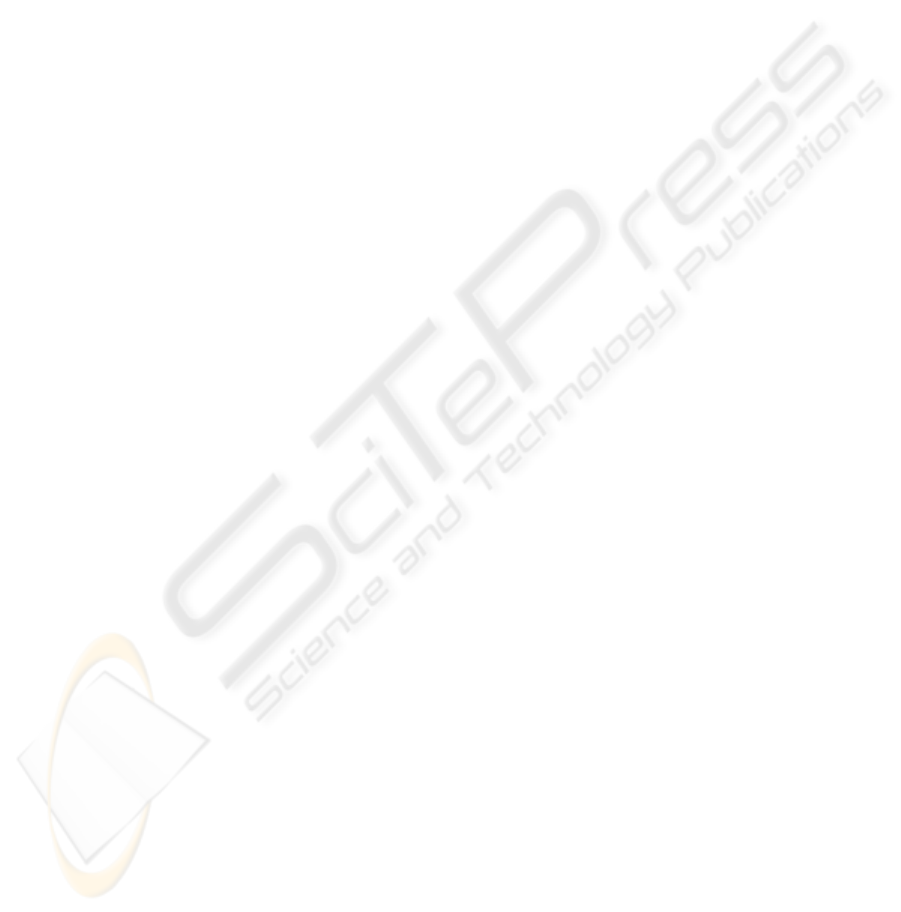
Acknowledgements
This work has been financed by a SAIOTEK 2003-04 grant from the Basque
Government. In its implementation we have used resources facilitated by the Cátedra
de Telefónica Móviles at the University of Deusto (http://www.ctme.deusto.es).
References
1. Telemetry definition, Wikipedia, http://en.wikipedia.org/wiki/Telemetry, 2004
2. OWASYS owa2x M2M modules Family, http://www.owasys.com/en/
BOK_100_1000_R3D.pdf, 2004
3. When Robots Rule the World, http://www.wired.com/news/technology/0,1282,65408,00.
html, Wired News, October 2004
4. Mars Exploration Rover Mission, http://marsrovers.jpl.nasa.gov/home/, NASA, 2004
5. Microchip PIC 16F87X Data Sheet, http://ww1.microchip.com/downloads/en/DeviceDoc/
30292c.pdf, Microchip Technology, 2001
6. The CMUcam2, http://www-2.cs.cmu.edu/~cmucam2/, Robotics Institute, Carnegie Mellon
University, 2004
7. Microsoft ASP.NET Home Page, http://asp.net, Microsoft Corporation, 2004
8. Mobile Application Development Toolkit, http://www.microsoft.com/downloads/
details.aspx?FamilyID=f4328333-0fd4-4348-88c0-39d10fb64f0a&DisplayLang=en,
Microsoft Corporation, 2004
9. Java 2 Platform, Micro Edition (J2ME), http://java.sun.com/j2me/, Sun Microsystems,
2004
10. WAP Binary XML Content Format, http://www.w3.org/TR/wbxml/, W3C, June 1999
11. Xylomenos G., Polyzos G. and Mahonen P. TCP Performance Issues over Wireless Links,
IEEE Communications Magazine, April 2001
12. Hypertext Transfer Protocol, http://www.w3.org/Protocols/, W3C, 2004
13. Hüttenrauch H. and Norman M, PocketCERO – Mobile Interfaces for Service Robots.
Proceedings of Mobile HCI 2001: Third International Workshop on Human Computer
Interaction with Mobile Devices, Dunlop, September 2001
14. Gage, D.W, Network Protocols for Mobile Robot Systems, SPIE Proceedings, 3210.
Presented at Mobile Robots XII, Pittsburgh, PA, 14-17 October, 1997
15. Sgouros N. and Gerogiannakis S., Integrating WAP-Based Wireless Devices in Robot
Teleoperation Environments, Proceedings of IEEE ICRA 2002, pp. 1191-1196, ISBN 0-
7803-7273-5}, 2002
16. Pirkus: Bluetooth Mobile Phone Controlled Robot,
http://www.blueserker.com/html/modules.php?op=modload&name=News&file=article&si
d=290&mode=thread&order=0&thold=0, 2005
17. Fujitsu, PFU Launch Initial Sales of MARON-1 Internet-Enabled Home Robot to Solutions
Providers in Japan Market, http://pr.fujitsu.com/en/news/2003/03/13.html, 2003
18. COMMBOTS website, http://www.ctme.deusto.es/COMMBOTS, Universidad de Deusto,
2004
51