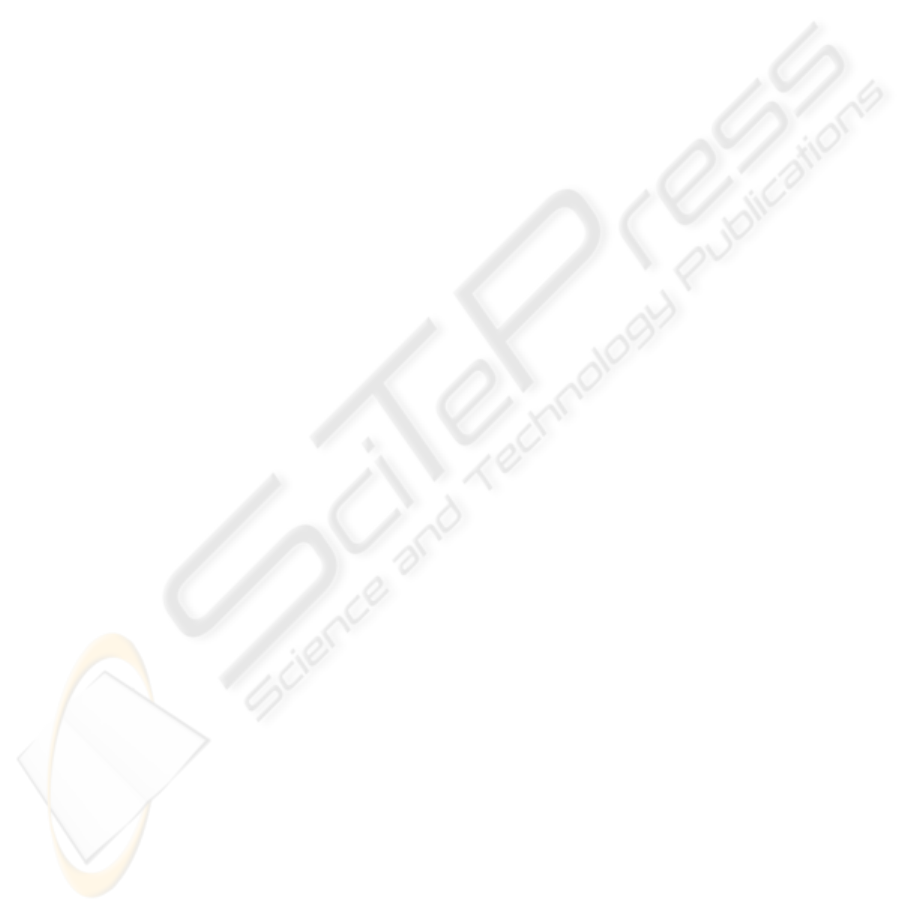
DEVELOPMENT OF HIGH PERFORMANCE SERVO
DRIVE/ANTI DRIVE MECHANISM FOR BACKLASH REMOVAL
I. Askari, S. A Hassan, M. Altaf, A. Azim, M. B. Malik, K. Munawar
College of Electrical and Mechanical Engineering. Rawalpindi. Pakistan
Keywords: 1 Degree of freedom Platform, Backlash Removal, System Modelling.
Abstract: In electromechanical drives, there is always a backlash between any pair of gears. Because of this, it is
almost impossible to realize a high accuracy and high performance drive. However such drives are crucial
in today’s modern electromechanical systems. A high performance drive/anti-drive servo mechanism is
developed to eliminate the effect of backlash. The concept utilizes redundant unidirectional drives to assure
positive coupling of gear meshes at all times. Based on this concept, a methodology for enumeration of
admissible redundant-drive backlash free mechanism has been established. The angular displacement is
achieved as a difference of two torques. These torques can be controlled by a high performance control
system. A controller model will be designed to move a single degree of freedom platform up to a desired
span with a payload.
1 INTRODUCTION
Manipulators use gear trains for power transmission
to allow actuators to be located in some desirable
position. Gear trains are also used for torque
amplification. Backlash is provided for prevention
of jamming of gear teeth due to manufacturing
errors or thermal expansion. However, backlash can
cause momentary loss of coupling between two
matting gears whenever there is torque reversal. It
can result in motion discontinuity, position
uncertainty, and impact in mechanical systems,
which, in turn, make accurate control of manipulator
difficult. End-effecter positioning accuracy is also
compromise due to backlash. Precision gears,
spring-loaded split gear assemblies, and precise
mechanical adjustment are often used to overcome
these difficulties. However, these techniques do not
completely eliminate the backlash and can increase
the cost of manufacturing and assembling.
Many methods such as backlash compensation
(Veitschegger and Wu, 1986), antibacklash gears
(Michalec, 1986), adjustable tooth thickness gears
(Michalec, 1986), adjustable center distance
(Dagalakis and Mayers, 1985) and harmonic drives
(Calson, 1985) have been proposed for the
elimination of backlash. Improvement on problems
caused from gear backlash has been made by using
these methods, e.g., backlash compensation used in
machine tools. However, these methods become
inadequate for robotic systems.
Presently none of these methods can eliminate
backlash in robotics completely. For example, the
method of adjustable center distance has been used
for the assembly of PUMA 560 robot. The backlash
control mechanism supplied by the manufacturer for
the PUMA robot is an eccentric cartridge-bearing
arrangement, as shown in figure1. Adjustable
centers are subject to maladjustments, and in the
field there is no assurance that the quality of a
readjustment will be comparable to the original.
This paper is a continuation of our previous work
where we developed a 2 DOF platform (Tanveer and
Masood et al, 2005), designed the controller (Askari
and Hassan et al, 2005), and finally modeled the
system (Hassan and Askari et al, 2005). Besides the
appropriate position as well as tracking control, the
only flaw of that system was backlash that resulted
in reduced efficiency for the tracking purposes. In
this paper a new concept of drive antidrive
mechanism has been described for one degree of
motion which results in a minimum backlash
between the gears to obtain a stable backlash free
system.
453
Askari I., A Hassan S., Altaf M., Azim A., B. Malik M. and Munawar K. (2006).
DEVELOPMENT OF HIGH PERFORMANCE SERVO DRIVE/ANTI DRIVE MECHANISM FOR BACKLASH REMOVAL.
In Proceedings of the Third International Conference on Informatics in Control, Automation and Robotics, pages 453-456
DOI: 10.5220/0001199304530456
Copyright
c
SciTePress