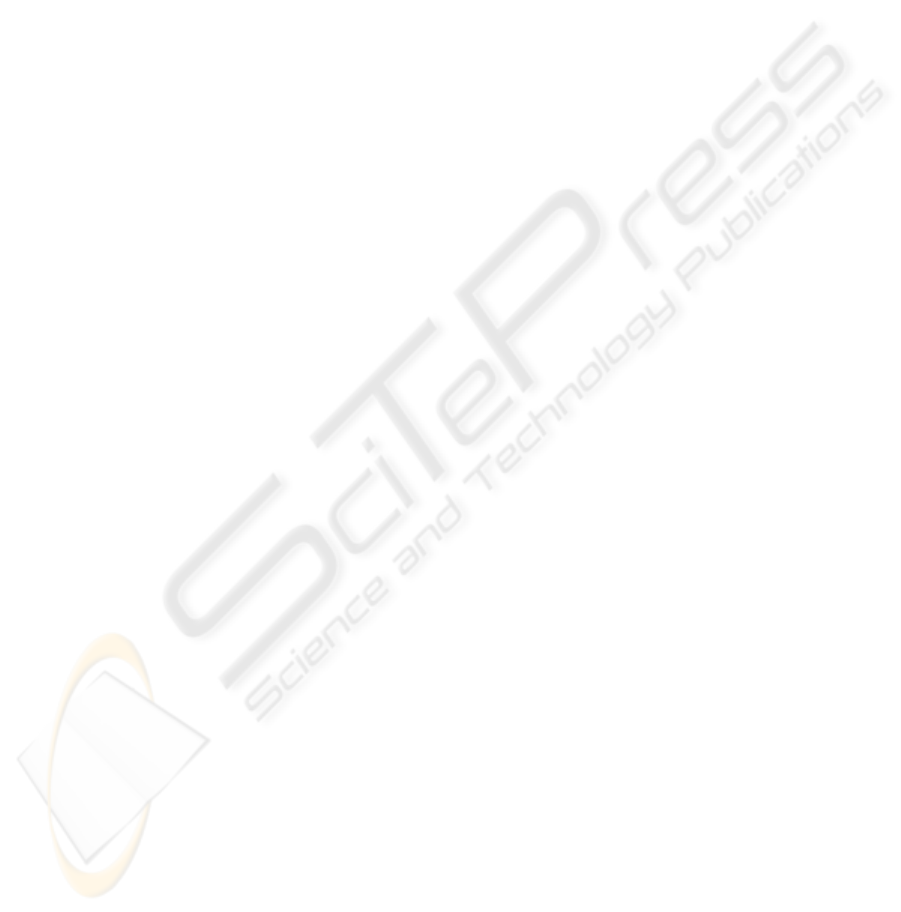
positions) there are two buttons, one to request a lift
going upwards and the other for going downwards,
and moreover course lights, time interval display
and acoustic signalization with the same timing
requirements as mentioned above for the lift cabin
control panel. The position and speed of each lift is
measured and controlled by a lift drive. This group
of in-puts/outputs requires special attention because
of hard real-time limits.
The control system architecture stems from the
following conception. The external serial bus
interconnects N identical lift controllers and a
dispatcher station; in addition, each lift controller
embodies a dedicated distributed system with
internal serial bus connecting a shaft controller, M
floor controllers, and a cabin controller. The shaft
controller, which is a dedicated multiprocessor,
comprises one scheduling processor and one drive
control processor communicating through a common
memory, two communication processors enabling
access to external and internal serial buses, and two
simple watchdog processors.
3.2 Functional Specifications
The behaviour of each lift is directed by its
scheduling processor using both global master
directives, which consider orders from floors
provided through a floor controller and local orders
from the lift cabin provided through a cabin
controller -- the global master, elected among all
active scheduling processors during the initialization
phase -- obtains also information about orders from
all cabins to improve task allocation efficiency. For
each shaft controller, a scheduling processor and a
drive control processor share, in two-port RAM, data
structures describing the state (position, speed,
direction, load, and error status), list of orders to be
serviced including allowed time limits, and the next
serviced floor.
Possible traffic modes implement a self-service
administration with various N-lift scheduling
strategies and a separate lift self-service or attendant
management including also such special policies as
maintenance and fire brigade support. While the
scheduling processor communicates with the global
master and, accordingly, updates the orders from
floors, the drive control processor controls the lift
position and speed and updates the lift state and
cabin orders. The lift cabin controller serves the
control panel and the load sensors and manages the
door drive respecting the door position, the drive
moment, and the gate optical barrier. Finally, the
floor controller serves floor buttons, course lights,
acoustic signalization of arriving lift, and display
with approximate time interval to floor tending.
The multiple lift control system is designed to be
fully observable and controllable through its serial
buses. In a special 'off-line' mode, every processor
can upload or download through the incident serial
bus its local data and local inputs or outputs. That
feature administered by relevant modes of the
dispatcher and diagnostic station behaviour props
installation and repair of the control system. Both
above mentioned stations can also emulate dedicated
network analyzers and management terminals.
While the dispatcher station can monitor, test, or
supervise the whole interconnected system, the
portable diagnostic station implements equivalent
functions for the individual lift controller. Such
property promotes both an adaptation of service
strategies and regular system maintenance.
After power supply initiation and successful
power-up tests of all processors including memories,
peripheries, and internal connections, the
communication processors incident with the external
interconnection elect, according to the lowest
address on external serial bus, the current global
master, which is responsible to allocate service tasks
to the individual lifts. This allocation follows a
strategy either prescribed by the dispatcher station or
selected by the global master according to the traffic
type of building serviced, week and month or season
day, and day or night time. When the external serial
bus is disconnected, the scheduling will proceed
locally.
The software of scheduling processors stems
from a real-time executive with pre-emptive task
planning based on fix priorities. The supervisor task,
which is periodically activated by a timer,
implements initialization, mode selection, and
extraordinary events services. The scheduler task,
which can be activated by a message, realizes global
and local scheduling of lift services. Other auxiliary
tasks support accessing and updating the lift data
model based on above mentioned data structures. As
for the drive control processors, their dedicated
software in foreground/background format
guarantees very short response times for speed and
position drive control loops and transfers, without so
strict temporal limits, information between the lift
data model and the lift cabin or floor controllers. In
each shaft controller, the communication controllers
implement corresponding, special purpose protocols
and release the execution processors from
communication loads. The lift cabin and floor
controllers fulfil the above stated functions using
polling loops.
FAULT MAINTENANCE IN EMBEDDED SYSTEMS APPLICATIONS - Multiple Lift Control System as Safety Critical
Embedded Application
185