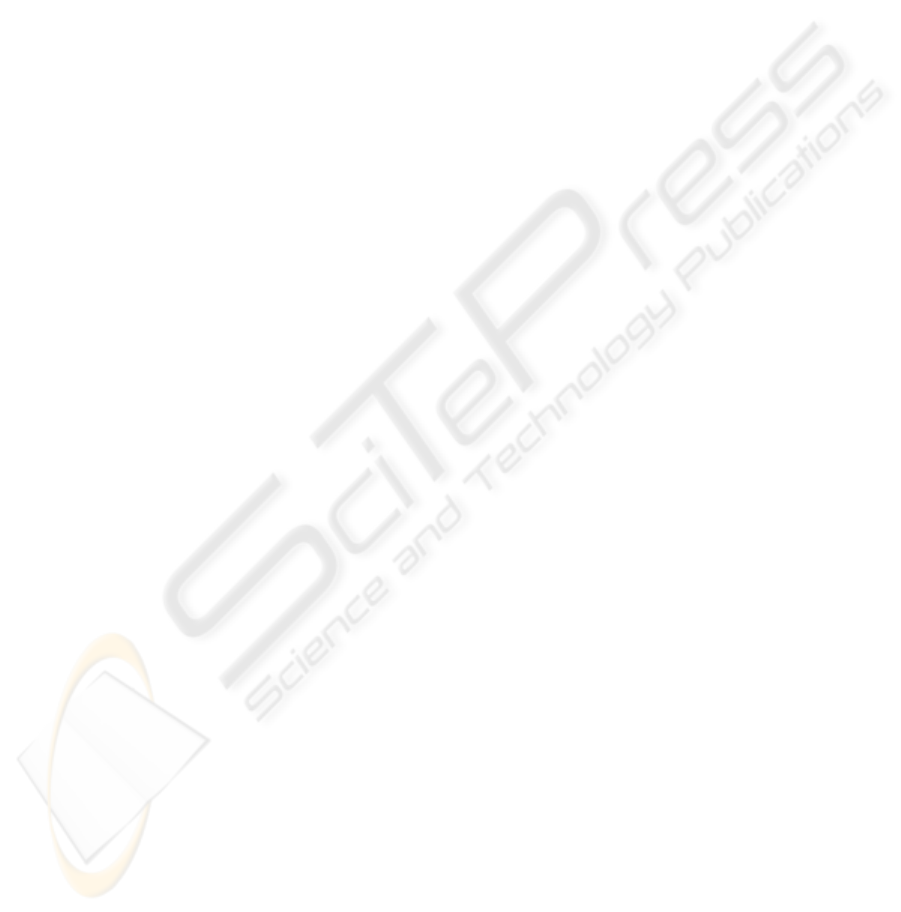
5 INTEGRATION OF
DISTRIBUTE OBJECTS
Aided with simulator and intelligent functions, the
systems are no longer being viewed as simply
operational and engineering tools, but quasi-
autonomous decision-makers. In this role they
continue to serve as the centre for operational
responsibility, but also provide data to systems and
users outside of the control centre environment who
depend upon timely information on which to base
day-to-day business decisions.
A full solution of intelligent SCADA will also
contain the following components/modules:
z distributed I/O with real-time data exchange
(networked data acquisition and control);
z batch control and executions;
z remote network management;
z multimedia user interface (large screen
terminals etc.)
To fully exploit the potentials the intelligent
SCADA system can offer, the system needs also
considerations on:
z assure security, data protection and access
management;
z redundant system components for reliability;
z the proper infrastructure framework for
information exchange (e.g. Internet protocol
applications).
6 CONCLUSIONS
The basic idea of a simulator enhanced intelligent
SCADA system architecture is introduced. The
concept of a simulator of a long-distance pipeline
system and its implementation approach are also
briefly mentioned.
The main features of the proposed system
simulator are as follows:
1. Hierarchical structured: The object orientation
of the model system and software architecture allows
the complex system be built and upgraded gradually.
2. Evolutionary: The system may evolve by
adding more specialised and modules. New objects
can be introduced. With several identical simulators
(or several copies of the simulator) available at
different phases of development, the performance of
the system can be improved continuously without
breaking the working life cycle.
3. Intelligent: The uncertainty in physical systems
can be dealt with using modern statistical methods,
fuzzy models and neural network techniques. The
system can learn from experience and update its
memory. The AI level of the decision making
process can be developed to make the whole system
highly intelligent.
REFERENCES
Demey, D, et al., Validation and implementation of model
based control strategies at an industrial wastewater
treatment plant, Water Science and Technology: a
Journal of the International Association on Water
Pollution Research, Volume 44, Issue 2-3. (2001)
Dieu, B, Application of the SCADA system in wastewater
treatment plants, ISA Transactions, Volume 40, Issue
3, (2001)267-281.
Gieling ThH; van Meurs WTh; Janssen, H J, A computer
network with SCADA and case tools for on-line
process control in greenhouses, Advances in Space
Research: the Official Journal of the Committee on
Space Research (COSPAR), Volume 18, Issue 1-2.
(1996)
Hernebring, C; Jönsson, L E; Thorén, U B; Møller, A,
Dynamic online sewer modelling in Helsingborg,
Water Science and Technology: a Journal of the
International Association on Water Pollution Research,
Volume 45, Issue 4-5,(2002)
Kingsley E. Abhulimen and Alfred A., Liquid pipeline
leak detection system: model development and
numerical simulation, Chemical Engineering Journal,
Volume 97, Issue 1. (2004)
Mareels, I, et al., Systems engineering for irrigation
systems: Successes and challenges, Annual Reviews in
Control, Volume 29, Issue 2, (2004)
Miller, M. R.; et al, 2000, Peak Expiratory Flow Profiles
Delivered by Pump Systems: Limitations due to Wave
Action, American Journal of Respiratory and Critical
Care Medicine, vol. 161, no. 6, (2000)
Nitivattananon, V., et al., Optimization of Water Supply
System Operation, Journal of Water Resources
Planning and Management, Vol. 122 No. 5.(1996)
Pham, D T, Xu, Y., Internet Enabled Total Automation-
Integration of Distributed Tasks in Manufacturing
Enterprises, the 15th IFAC World Congress b'02,
Spain, (2002).
Turner, W. J. Kwon, P. S-J.and Maguire, P. A., Evaluation
of a gas pipeline simulation program, Mathematical
and Computer Modelling, Volume 15, Issue 7, (1991).
Xu, Y., Web-based Enterprise Automation System Design
for Feed Industry, Computing Technology and
Automation, 2004-No.4 (in Chinese),,(2004).
Xu, Y., "A Dynamic Hierarchical Model for complex
pipeline systems, Proceedings of 2nd Inter. Confer. on
Pipeline Systems, Hague, Netherlands, (1997).
INTELLIGENT SIMULATOR DESIGN FOR DISTRIBUTED PIPELINE NETWORKS CONTROL
185