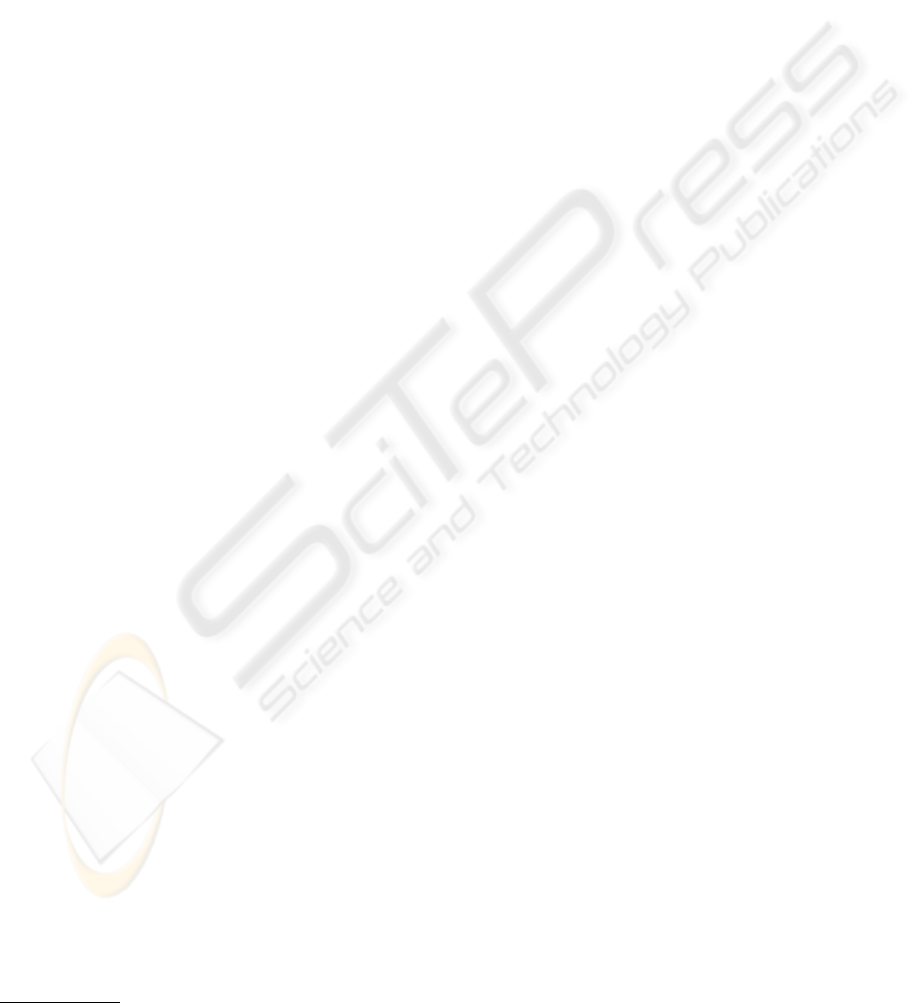
often based on timed sequences making it possible to
define the duration of activities. The timed extensions
of Petri nets are highly suitable models for the for-
mal study of these mechanisms (Juanole et al., 2000).
Although timed coloured Petri nets are usually used
to investigate the logical correctness of systems, they
can also be used to evaluate the performances of them.
The Petri net colouring allows to reduce the size of
a model to get a more compact representation of the
systems including dictinct components having simi-
lar behaviours. This is the case here with the station
operating cycle.
The model was designed using the software De-
sign/CPN (Christensen et al., 1997). Our choice has
been guided by the integration of performance facili-
ties in this computer tool (Linstrøm and Wells, 1998).
Design/CPN
1
allows to collect data during the model
execution and create reports containing statistical val-
ues.
3.1 Modelled Behaviour
This work focuses on the study of interactions within
the control system of an automated assembly line.
Thus, the model describes the architecture supporting
the exchanges between the local command units and
the controller. It is primarily founded on the indepen-
dent activities of the various stations and their access
to a shared resource which is the controller.
The model [Fig. 2] implements three main ele-
ments that are the station set, the communication
buffer and the controller. A counting function of pro-
duced parts is also implemented.
Station operations are integrated into the model in
the form of places. The described sequence takes into
account the operations of routing (place Conveying),
part identification (place Identification), status request
sent to the controller (place Request), response analy-
sis emitted by the controller (place Analysis), part as-
sembly processing (place Process), production data
reporting (place Reporting) and part relaxation (place
Relaxation).
Transitions correspond to events that make the to-
ken circulation symbolizing the system evolution.
Temporization of some transitions (notation @+de-
lay) makes it possible to keep the presence of tokens
in the places located upstream during the specified
time. It allows to specify the execution time of op-
erations.
Colouring is primarily used to distinguish various
stations as well as various positions of messages in
the communication buffer.
For the stations, colours are applied according to
their number and their order on the assembly line.
1
Design/CPN has been replaced by CPN/Tools
Part moving from a station to another one is mod-
elled by incrementing the token colour number, ex-
cept in case of a processing by the last station (end of
assembly). Station availability is managed by a spe-
cific place (place Inactivity) guaranteeing exclusivity
of its execution to the processing of only one part.
The presence of a token of color x indicates that the
station x is inactive. The place Inactivity is initialized
according to the number of declared stations.
The communication buffer is modelled by a place
(Waiting) in which the token represents the situation
of a station having emitted a request. Colors are af-
fected according to the order in the buffer. Each token
move models a message advance and its color number
is decreased.
The controller disponibility is done by a single
place (place Idling) and a token in this place indi-
cates the controller availability. A message arrival in
the communication buffer implies the token leaves the
place Idling. The controller stops its activity when it
completes the message processing and when the com-
munication buffer is empty.
3.2 Evaluated Criteria
Performance of the studied production systems is
mainly evaluated by the analysis of the communica-
tion buffer occupancy and by the controller load.
Communication buffer contents and the message
origin make it possible to know the number and the
list of stations waiting for a response from the con-
troller.
The message waiting time and the controller re-
sponse time can be deduced from the simulation data.
The analysis of these criteria allows to evaluate pro-
duction system performances and to obtain indica-
tions leading to a good knowledge in the way in which
the exchanges between the local command units and
the controller are held.
Product inter-departure times are also measured.
They are defined as the time between two part com-
plete assemblies and they can be easily compared
with the results of modelled real systems. Product
inter-departure times are a simple and effective per-
formance indicator of the production systems.
3.3 Model Settings
The size of the communication buffer and the fieldbus
speed are two modelling assumptions integrated into
the model.
The size of the communication buffer is defined
according to the number of stations declared in the
model. It makes it possible to have a sufficient capac-
ity for all evaluated configurations in order to avoid a
saturation in accordance with the real systems.
PERFORMANCE EVALUATION OF A CONTROLLED FLOW-SHOP SYSTEM WITH A TIMED PETRI NET
MODEL
497