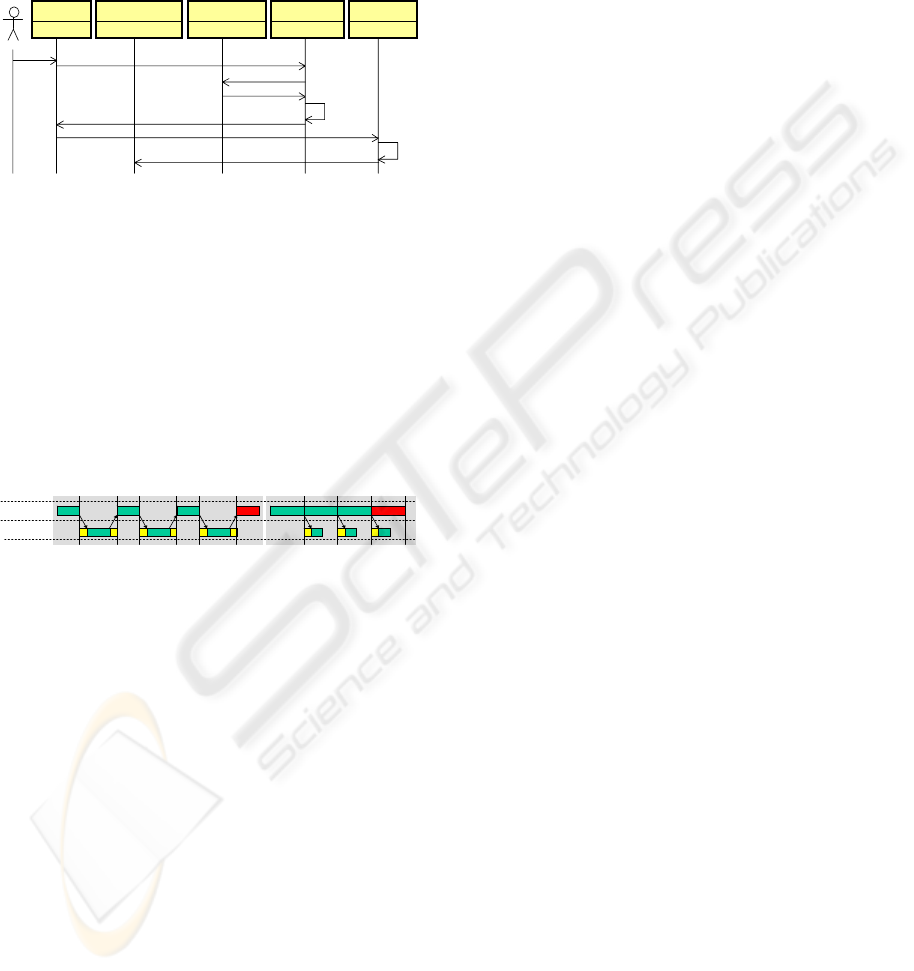
In the serial process (Figure 6.a) there is an
accumulated delay in every movement due to the
computational time (in the simulation) and the
communication time. This sequence is suitable just
for process where the speed in not important, but not
for critical process such as teleoperation where it is
necessary to optimize the performance.
: S imu lato r: S imu la to r :Robot Contro lle r:Robot Controller :Grasp P lanner:Grasp P lanner:3 D Rep os it or y:3 D Rep os it or y
Ob je c t Se lect in g
Gras p an Object
Trajectory Request
Trajectory
Gras ping
Algorithm
:Path Planner:Path Planner
3D Object Request
3D Ob ject Model
Gra s p P o in ts
Path planning
Algorithm
Figure 5: Sequence diagram for the planning processes.
Parallel process is carried out by a global
Scheduler with a Real-Time manager, which
controls both virtual and real movement
guaranteeing a security delay. The computational
time of a movement in the simulator will depend on
the complexity of the virtual world. The hard Real-
Time control of the robot seen in section 3.1 allows
the Scheduler to know the state of the real
movement and to modify the speed of this
movement (even to stop it by a emergency stop task
with the highest priority) in order to guarantee the
security delay in each movement.
1
1
Virtual
Movements
Real
Movements
2
2
3
3
4 1 2 3 4
1 2 3
Figure 6: a) Serial processes b) Parallel processes.
The scheduler is designed through the analysis of
the robot in Real-Time and the analysis of the
computational and communication parameters. In
our case, Real-Time Corba gives the necessary
quality of services to the communication parameters
to allow our system to be scheduled as is seen in
section 3.2. Figure 6.b shows a sequence example in
which the virtual movements are slower than real
movements, that is why the process is scheduled
with a security delay equivalent to the time of one
virtual movement plus the communication.
4 CONCLUSIONS
In this work we have presented the integration of an
experimental robotic cell with 3D servoing for
manipulation environments. We have developed a
distributed architecture based on Real-Time Corba
using the ORB supplied by TAO. This architecture
together with the hard Real-Time control of the
robot, based on RTLinux, allows us to turn the
global system into a soft Real-Time system in order
to improve its security, reliability and speed.
Distributed applications have been developed
following this architecture, such as the advanced
simulator, the 3D acquisition application and the
robot control application.
After this integration, the experimental cell can
work for full intelligent manipulation environments
as well as a secure robot teleoperation.
ACKNOWLEDGEMENTS
This research has been supported by the CICYT
Spanish projects PDI2002-03999-C02 and
DPI2005_03769.
REFERENCES
Albus, J.S., McCain, H.G., Lumia, R., NASA/NBS
Standard Reference Model for Telerobot Control
System Architecture, NIST, Technical Report 1235,
Gaithersburg, MD, April 1989.
Woo E., MacDonald B. A.., Trépanier F.. Distributed
mobile robot application infrastructure. IROS’03,
pages 1475-80, Las Vegas, October 2003
Pires, JN., Monteiro, P., Schölzke, V., Using Robot
Manipulators on High Efficient Wrapping Machines
for Paper Industry, ISR’2001, Seoul, Korea, 2001
Fung W. K., Xi N., Lo W. T., Liu Y. H., Improving
efficiency of Internet based teleoperation using
network QoS, ICRA 2002
Mallet, A., Lacroix, S., Gallo, L., Position estimation in
outdoor environments using pixel tracking and
stereovision. ICRA’00, pages 3519, April 2000.
Saedan, M., Ang, M. H, 3D Vision-Based Control of an
Industrial Robot, IASTED International Conference on
Robotics and Applications, Nov 19-22, 2001, Florida,
USA, pp. 152-157.
Merchán, P., Adán, A., Salamanca, S., Cerrada, C., 3D
Complex Scenes Segmentation From a Single Range
Image Using Virtual Exploration, Lecture Notes in
Artificial Intelligence, pp 923-932,. Springer. 2002.
Adán, A., Merchan, P., Salamanca, S., Recognition of
Free-Form Objects in Complex Scenes Using DGI-BS
Models. Submitted to the 3DPTV’06 Chapel Hill,
USA. 2006
Adán, A., Vázquez, A.S., Molina, F., Grasping Solutions
through MWS Models. ICAR’05 ISBN: 0-7803-9178-
0 Seattle (Washington). USA 2005
Vázquez, A. S., Torres, R., Adán, A., Path Planning for
Manipulation Environments through Interpolated
Walks. Technical Report, Grupo ISA, UCLM, Spain.
2006.
DISTRIBUTED CONTROL SYSTEM OF AN EXPERIMENTAL ROBOTIC CELL WITH 3D VISION
511