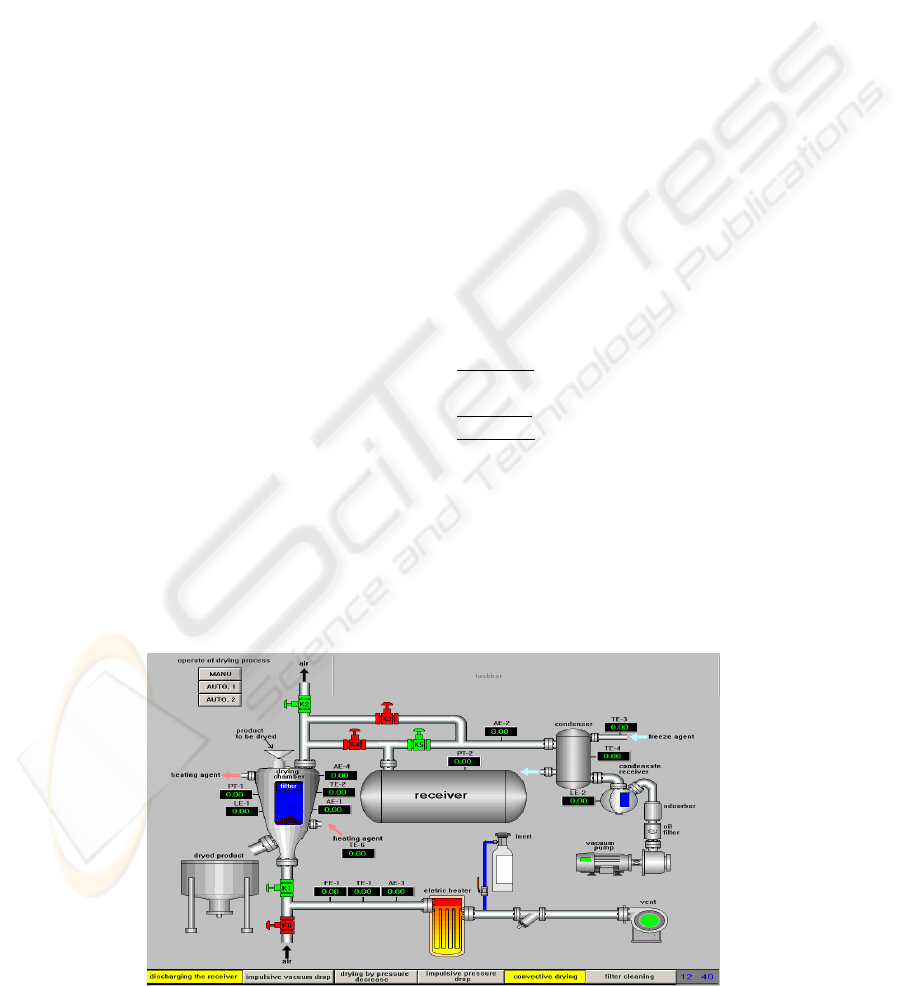
of the above mentioned B-DCS on the example of
the model of the dryer unit for drying bioactive
products. The creation and application of
computerized generalizing MMs and the
development of intensive drying process for
bioactive products exemplified by highly purified α
- amino acids.
The desiccation of highly purified α- forms of
irreplaceable amino acids as follows: Thr
(threonin), Trp (tryptophan), Leu (.Leucin), Ile (iso-
leucin) involves removal of the mixture of ethanol
(in which they are practically insoluble) and water
with solubility of 0.02-0.09 kg/kg at 20
0
C. The
residence time in vacuum dryer is up to 72 hours.
In view of the pressing requirement for the
development of commercial technology for intensive
desiccation of pure amino acids 25 types of dryers
were analyzed on the computer in an effort to find
the method of adequate intensive drying technology:
vacuum application, active hydrodynamic regimes.
A complex pilot plant was fabricated [1,2] for the
selection of appropriate drying process and the
following processes were tested : desiccation in
pseudo-liquified and densely purged beds ,
desiccation by pressure reduction (DPR), vacuum
oscillating desiccation - repeated alternation of
heating by hot gas and vacuum cooling, impulse
desiccation by depressurization of drying chamber
(DDC)- a new method proposed.
It was experimentally established that free moisture
is basically removed from the bioproducts being
investigated and they tend to agglomerate. The
agglomeration mechanism is related to the change in
the liquid phase composition upon desiccation: the
crystals partially dissolve in the mixture upon rapid
increase of water proportion (more volatile spirit is
removed faster) and subsequently start to stick to
each other. So as to loosen and break the
agglomerates the impulse depressurization was
effectively employed causing breaking normal
stresses depend-
ent on the duration and depth of terminal pressure
drop, size, inner structure and temperature of
agglomerates.
The proposed method alowed to meet the
requirements for the dispersive structure of amino
acids and to reduce
с
to 0.5 hour or less. The
unit incorporates the dryer, heating agent feeding
line, depressurization system and receiver.
5 DRYING PROCESS
DESCRIPTION
The installation scheme is represented in fig. 2
(screen shot of the engineer’s interface). The raw
material goes through the charging device of the
drying apparatus and then enters the drying
chamber. In the drying chamber the product is
exsiccated by hot air. The product is unloaded
pneumatically in the loading tank. In the drying
chamber vacuum creation is possible with the help
of pumping system consisting of the pump, the
condenser and the hotwell .The drying process can
be carried out in various ways. In emulation system
in the capacity of control and regulating blocks the
most widespread drying regimes are used.
Regime 1
– Drying in filtering and pseudo-liquefied
layers.
Regime 2
– Drying by pressure decline.
Regime 3
– Drying by the combined pressure drop
and vacuum.
This method integrates the following regimes of
drying:
− Preheating;
− Depressurization;
− Pumping out;
− Layer tossing up;
− Clearing the filter.
Figure 2: HI of the dryer unit.
HEAT-AND-POWER PROCESSES OPTIMIZATION BY MEANS OF MODEL-BASED SIMULATION
209