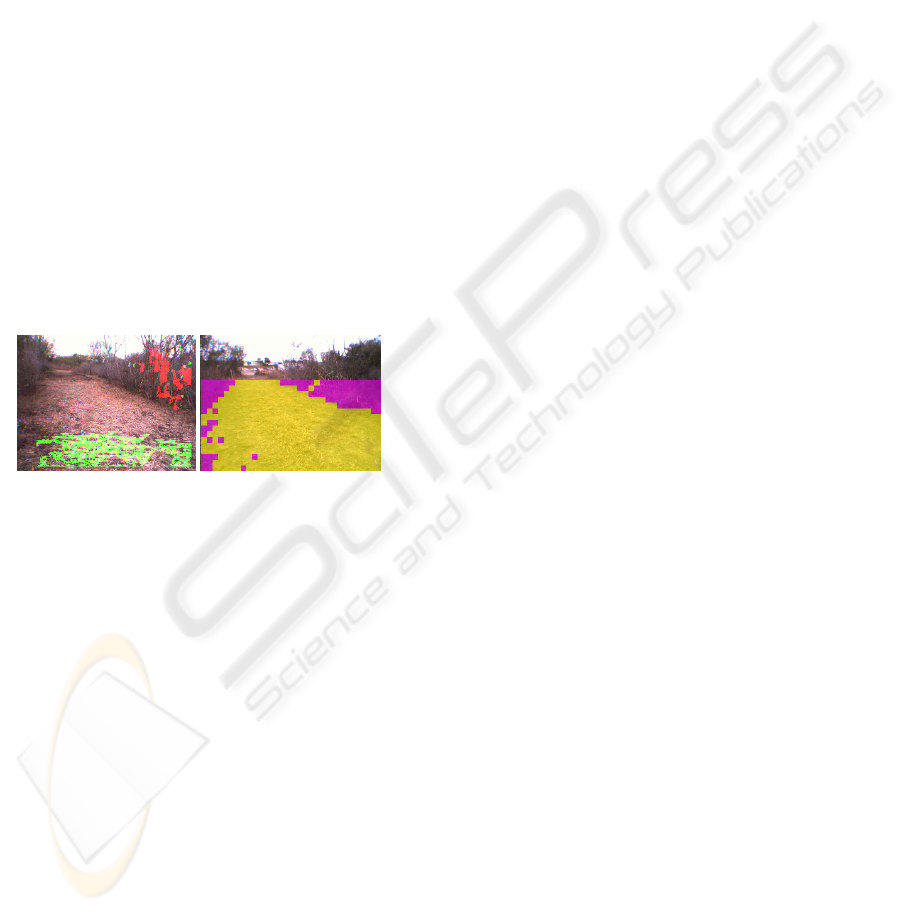
4 SUMMARY AND
CONCLUSIONS
The NIST 4D/RCS reference model architecture was
implemented on the DARPA LAGR vehicle, which
was used to prove that 4D/RCS can learn. Sensor
processing, world modeling, and behavior genera-
tion processes have been described in this paper.
Outputs from sensor processing of vehicle sensors
are fused with models in WM to update them with
external vehicle information. World modeling acts as
a bridge between multiple sensory inputs and a be-
havior generation (path planning) subsystem. Behav-
ior generation plan vehicle paths through the world
based on cost maps provided from world modeling.
Learning, as used on the LAGR vehicle includes
learning by example, learning from experience, and
learning of behaviors that are more likely to lead to
success.
Future research will include completion of the
sensory processing upper level (SP2) and developing
even more robust control algorithms than those de-
scribed in this paper.
(a) (b)
Figure 9: Learning by example images. (a) is an image
taken during learning and overlaid with (red) obstacles
and (green) ground, (b) is the same image overlaid with
traversability information as obstacles (magenta) and
ground (yellow).
REFERENCES
Albus, J.S., Juberts, M., Szabo, S., RCS: A Reference
Model Architecture for Intelligent Vehicle and High-
way Systems, Proceedings of the 25th Silver Jubilee
International Symposium on Automotive Technology
and Automation, Florence, Italy, June 1-5, 1992.
Albus, J.S., Huang, H.M., Messina, E., Murphy, K.N.,
Juberts, M., Lacaze, A., Balakirsky, S.B., Shneier,
M.O., Hong, T.H., Scott, H.A., Proctor, F.M., Shackle-
ford, W., Michaloski, J.L., Wavering, A.J., Kramer,
Tom , Dagalakis, N.G., Rippey, W.G., Stouffer, K.A.,
4D/RCS Version 2.0: A Reference Model Architecture
for Unmanned Vehicle Systems, NISTIR, 2002.
Albus, J.S., Balakirsky, S.B., Messina, E., Architecting A
Simulation and Development Environment for Multi-
Robot Teams, Proceedings of the International Work-
shop on Multi Robot Systems, Washington, DC, March
18 – 20, 2002
Balakirsky, S.B., Chang, T., Hong, T.H., Messina, E.,
Shneier, M.O., A Hierarchical World Model for an
Autonomous Scout Vehicle, Proceedings of the SPIE
16th Annual International Symposium on Aero-
space/Defense Sensing, Simulation, and Controls, Or-
lando, FL, April 1-5, 2002.
Bostelman, R.V., Jacoff, A., Dagalakis, N.G., Albus, J.S.,
RCS-Based RoboCrane Integration, Proceedings of
the International Conference on Intelligent Systems: A
Semiotic Perspective, Gaithersburg, MD, October 20-
23, 1996.
Chang, T., Hong, T., Legowik, S., Abrams, M., Conceal-
ment and Obstacle Detection for Autonomous Driving,
Proceedings of the Robotics & Applications Confer-
ence, Santa Barbara, CA, October, 1999.
Heyes-Jones, J., A* algorithm tutorial, 2005
http://us.geocities.com/jheyesjones/astar.html.
Shneier, M., Chang, T., Hong, T., and Shackleford, W.,
Learning Traversability Models for Autonomous Mo-
bile Vehicles, Autonomous Robots (submitted), 2006.
Jackel, Larry, LAGR Mission,
http://www.darpa.mil/ipto/programs/lagr/index.htm,
DARPA Information Processing Technology Office,
2005
Konolige, K., SRI Stereo Engine, 2005
http://www.ai.sri.com/~konolige/svs/.
Michaloski, J.L., Warsaw, B.A., Robot Control System
Based on Forth, Robotics Engineering, Vol. 8, No. 5,
pgs 22-26, May, 1896.
Ojala, T., Pietikäinen, M., and Harwood, D., A Compara-
tive Study of Texture Measures with Classification
Based on Feature Distributions, Pattern Recognition,
29: 51-59, 1996.
Oskard, D., Hong, T., Shaffer, C., Real-time Algorithms
and Data Structures for Underwater Mapping, Na-
tional Institute of Standards and Technology, 1990.
Shackleford, W., The NML Programmer's Guide (C++
Version), 1990.
http://www.isd.mel.nist.gov/projects/rcslib/NMLcpp.ht
ml.
Shackleford, W., Stouffer, K.A., Implementation of
VRML/Java Web-based Animation and Communica-
tions for the Next Generation Inspection System
(NGIS) Real-time Controller, Proceedings of the
ASME International 20th Computers and Information
in Engineering (CIE) Conference, Baltimore, MD,
September 10 – 13, 2000.
Tan, C., Hong, T., Shneier, M., and Chang, T., "Color
Model-Based Real-Time Learning for Road Follow-
ing," in Proc. of the IEEE Intelligent Transportation
Systems Conference (Submitted) Toronto, Canada,
2006
THE LAGR PROJECT - Integrating Learning into the 4D/RCS Control Hierarchy
161