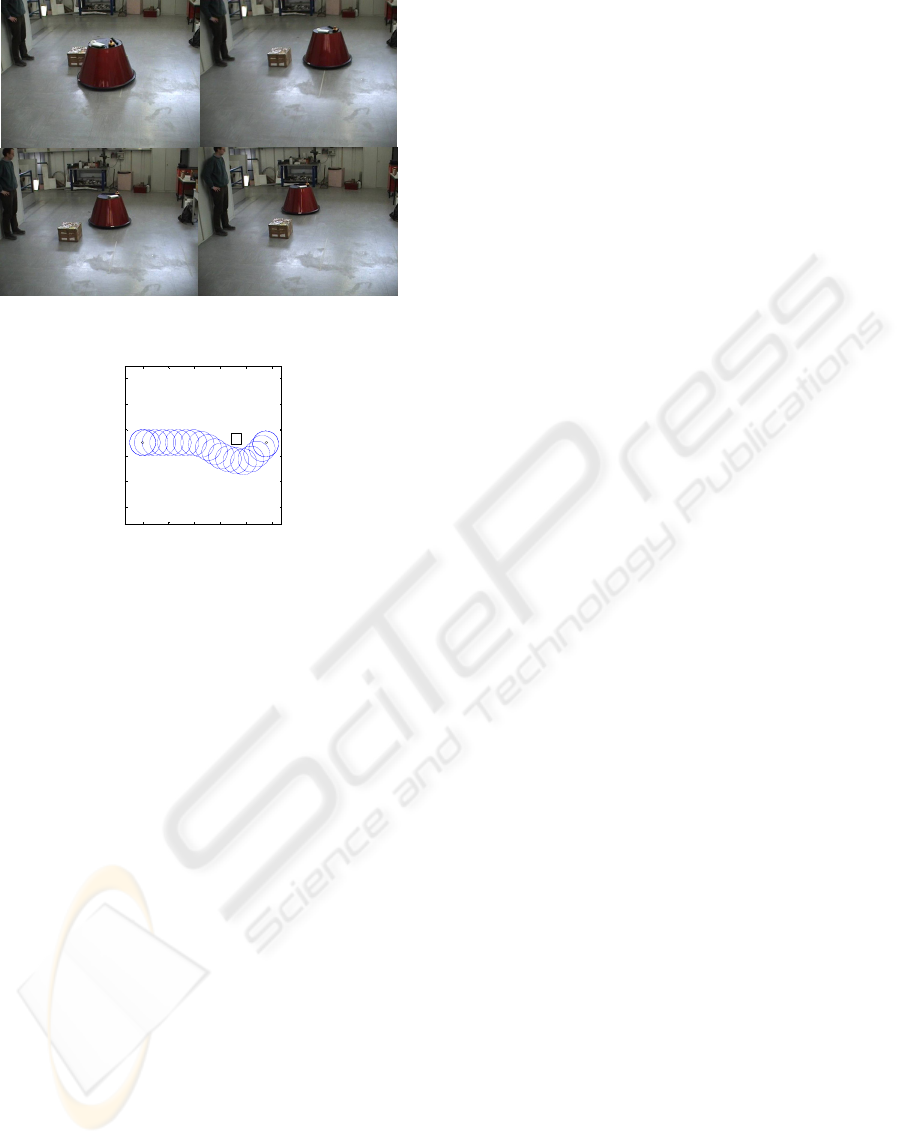
Figure 12e: safe robot motion to the target.
1 2 3 4 5 6
-1
0
1
2
3
4
X [ m]
Y [m]
Figure 12f: entire real trajectory.
9 CONCLUSIONS
This paper presents a novel technique called
“Reactive Simulation” for real-time obstacle
avoidance. A vehicle’s trajectory simulation starts
every time a new local target is planned due to the
detection of an obstacle. It was verified that 50 ms
integration step permits a fast simulation and the
maximum error enters in boundaries of safe robot
motion. The algorithm was successfully tested on a
vehicle in real-time applications, where an important
aspect is the correct execution of the tasks which
have to communicate with sensors, to estimate the
pose and to plan a safe path.
REFERENCES
Oussama Khatib, 1986, Real-Time Obstacle Avoidance
for Manipulators and Mobile Robot, in: The
International Journal of Robotics Research, Vol. 5,
No 1.
Y. Koren, J. Borentein, 1991, Potential Field Methods and
their Inherent Limitations for Mobile Robot
Navigation, in: Proceedings of the IEEE conference on
Robotics and automation, Sacramento, California,
April 7-12, pp 1398-1404.
J. Borentein, Y. Koren, 1991, The Vector Field histogram
– fast obstacle avoidance for mobile robot, in: IEEE
Journal of Robotics and Automation, Vol 7, No 3,
June, pp. 278-288.
Minguez, J., Montano, L., 2005. Sensor-based motion
generation in unknown, dynamic and troublesome
scenarios,in: Robotics and Automation Systems. 52, pp
290-311.
Planas R.M., Fuertes J.M., Martinez A.B.,Qualitative
Approach for Mobile Robot Path Planning based on
Potential Field Methods, Automatic Control Dept.
Technical University of Catalonia.
E.M. Nebot, H. Durrant-Whyte, 1999, A High Integrity
Navigation Architecture For Outdoor Autonomous
Vehicles, Robotics and Autonomous Systems, Vol 26,
p81-97.
Alonzo Kelly, Bryan Nagy, 2002, Reactive Nonholonomic
Trajectory Generation via Parametric Optimal Control,
submitted to the International Journal of Robotics
Research, Summer
I. Ulrich, J. Borentein, 1998, VFH+: Reliable Obstacle
Avoidance for Fast Mobile Robot, in: Proceedings of
the 1998 IEEE International Conference on Robotics
and Automation, Leuven, Belgium, May 16-21, pp.
1572–1577
I. Ulrich, J. Borentein, 2000, VFH*: Local Obstacle
Avoidance with Look-Ahead Verification, in: 2000
IEEE International Conference on Robotics and
Automation, San Francisco, CA, April 24-28, pp.
2505-2511
M. De Cecco, 2002, Self-Calibration of AGV Inertial-
Odometric Navigation Using Absolute-Reference
Measurement, in: IEEE Instrumentation and
Measurement Technology Conference, Anchorage,
AK, USA, 21-23 May
M. De Cecco, 2000, A new concept for triangulation
measurement of AGV attitude and position, in:
Measurement Science and Technology, vol 11, pp 105-
110
J. Chestnutt, J. Kuffner, K. Nishiwaki, S. Kagami, 2003,
Planning Biped Navigation Strategies in Complex
Environments, in:IEEE Int’l Conf. on Humanoid
Robotics (Humanoids 2003)
A. Stentz, 1994, Optimal and Efficient Path Planning for
Partially-Known Environments
, Proc. Of IEEE
International Conference on Robotics and
Automation, May 1994
L. Baglivo, M. De Cecco, F. Angrilli, F. Tecchio, A.
Pivato, 2005, An integrated hardware/software
platform for both Simulation and Real-Time
Autonomous Guided Vehicle Navigation, Proceedings
19th European Conference on Modelling and
Simulation
M. De Cecco, L. Baglivo, E. Ervas, E. Marcuzzi, 2006,
Asynchronous And Time
-Delayed Sensor Fusion Of A
Laser Scanner Navigation System And Odometry,
XVIII Imeko World Congress Metrology For a
Sustainable Development, September, 17 – 22, 2006,
Rio de Janeiro, Brazil, in publication
REACTIVE SIMULATION FOR REAL-TIME OBSTACLE AVOIDANCE
135