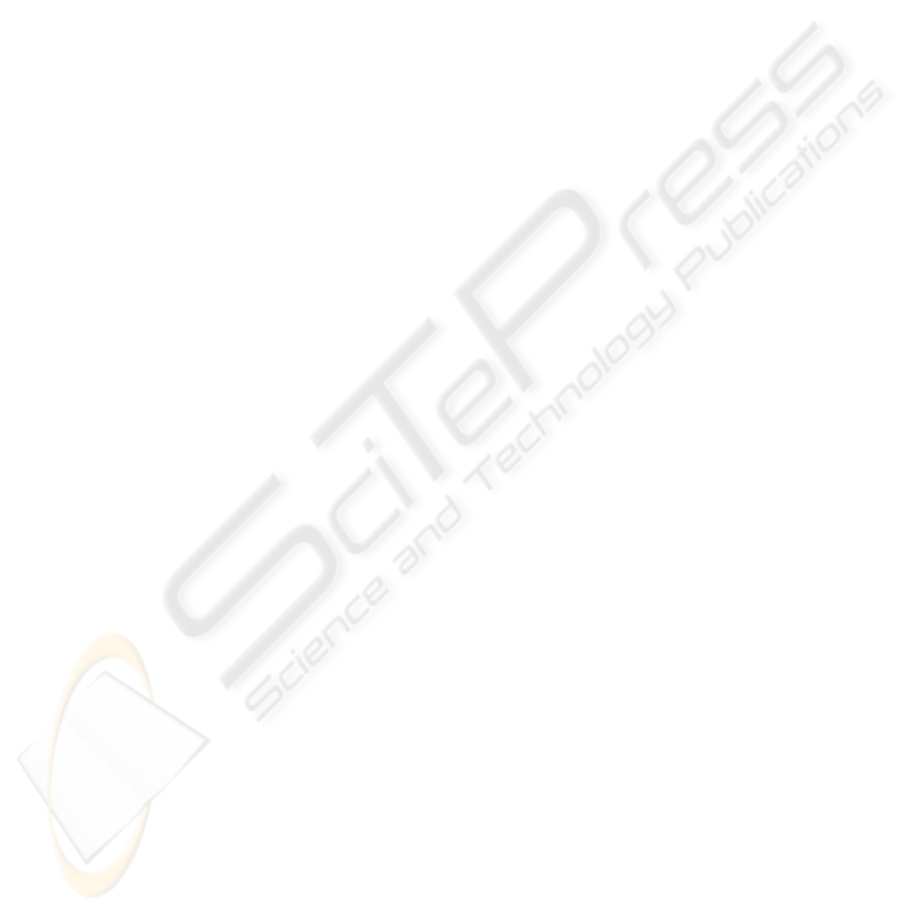
tively. The entries in Table 1 are average values over
20 instances.
The results show that the presented heuristic per-
forms very well for the entire collection of instances.
We observe that δ decreases with the increase in the
number of jobs. On average δ = 1.79%, 0.52%,
0.45%, 0.29%, 0.15% and 0.15% for problems with
20, 40, 60, 80, 100, and 120 jobs, respectively. The
CPU time of the heuristic grows with the number of
jobs. This increase is more significant for the CG al-
gorithm than for the GA. The number of machines
does not seem to affect significantly the computation
time of the heuristic, however, we observe that in the
case of 2 machines the CG algorithm consumes less
CPU seconds than in the cases of 3 and 4 machines.
7 CONCLUSIONS
In this paper a heuristic combining the column gener-
ation algorithm with the genetic algorithm for solving
the two-stage flowshop preemptive scheduling prob-
lem with parallel unrelated machines and resource
constraints at the first stage, and a single machine at
the second stage has been developed. The heuristic
has been tested as to its effectiveness in finding a min-
imum makespan schedule and as to its computation
time. The obtained results indicate that for problems
with a large number of jobs the heuristic usually finds
schedules with makespan close to the optimal value
in reasonable computation time.
REFERENCES
Barnhart, C., Johnson, E., Nemhauser, G., Savelsbergh, M.,
and Vance, P. (1998). Branch and price: column gen-
eration for solving huge integer problems. Oper. Res.,
46:316–329.
Brah, S. A. and Loo, L. L. (1999). Heuristics for scheduling
in a flow shop with multiple processors. Europ. J. of
Opernl Res., 113:113–112.
Chen, B. (1995). Analysis of classes of heuristics for
scheduling a two-stage flow shop with parallel ma-
chines at one stage. J. of Opernl Res. Soc., 46:234–
244.
Chen, Z.-L. and Lee, C.-Y. (2002). Parallel machine
scheduling with a common due window. Europ. J. of
Opernl Res., 136:512–527.
Dantzig, G. B. and Wolfe, P. (1960). Decomposition prin-
ciple for linear programs. Oper. Res., 8:101–111.
Figielska, E. (1999). Preemptive scheduling with
changeovers: using column generation technique and
genetic algorithm. Comp. and Ind. Engin., 37:63–66.
Gilmore, P. C. and Gomory, R. E. (1961). A linear program-
ming approach to the cutting-stock problem. Oper.
Res., 9:849–859.
Goldberg, D. E. (1989). Genetic Algorithms in Search, Op-
timization and Machine Learning. Addison-Wesley.
Gupta, J. N. D. (1988). Two stage hybrid flowshop schedul-
ing problem. J. of Opernl Res. Soc., 39:359–364.
Haouari, M. and M’Hallah, R. (1997). Heuristic algorithms
for the two-stage hybrid flowshop problem. Oper. Res.
Let., 21:43–53.
Holland, J. H. (1975). Adaptation in Natural and Artificial
Systems. University of Michigan Press, Ann Arbor,
MI.
Hoogeveen, J. A., Lenstra, J. K., and Veltman, B. (1996).
Preemptive scheduling in a two-stage multiproces-
sor flow shop is np-hard. Europ. J. of Opernl Res.,
89:172–175.
Linn, R. and Zhang, W. (1999). Hybrid flow shop schedul-
ing: a survey. Comp. and Ind. Engin., 37:57–61.
Oguz, C., Ercan, M. F., Cheng, T. C. E., and Fung, Y. F.
(2003). Heuristic algorithms for multiprocessor task
scheduling in a two-stage hybrid flow shop. Europ. J.
of Opernl Res., 149:390–403.
Ruiz, R. and Maroto, C. (2006). A genetic algorithm for hy-
brid flowshops with sequence dependent setup times
and machine eligibility. Europ. J. of Opernl Res.,
169:781–800.
Santos, D. L., Hunsucker, J. L., and Deal, D. E. (1995).
Global lower bounds for flow shop with multiple
processors. Europ. J. of Opernl Res., 80:112–120.
Slowinski, R. (1980). Two aproaches to problems of re-
source allocation among project activities - a compar-
ative study. J. Opl Res. Soc., 31:711–723.
Suresh, V. (1997). A note on scheduling of two-stage flow
shop with multiple processors. Int. J. of Prod. Econ.,
49:77–82.
PREEMPTIVE SCHEDULING IN A TWO-STAGE MULTIPROCESSOR FLOWSHOP WITH RESOURCE
CONSTRAINTS
135