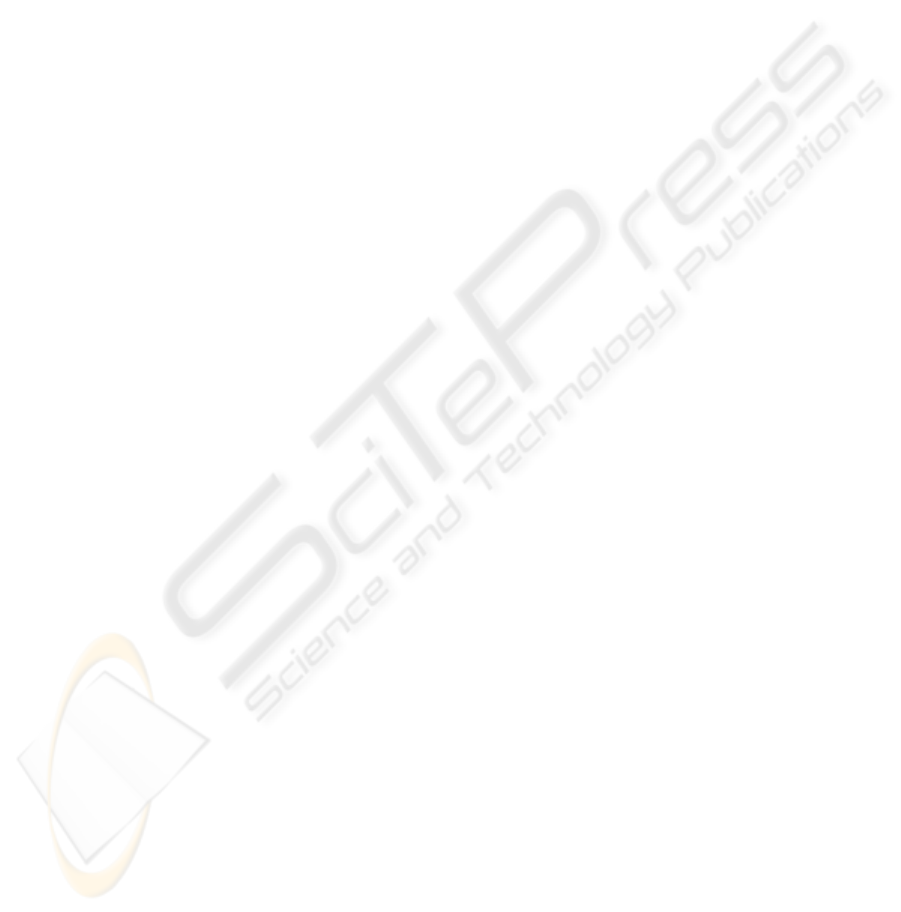
Crosbie, R., Zenor, J., Bednar, R., and Word, D. (2004).
High-speed, scalable, real-time simulation using dsp
arrays. In Proceedings of the 18th Workshop on Par-
allel and Distributed Simulation (PADS04), pages 52–
59. IEEE Computer Society.
Deppe, M., Zanella, M., Robrecht, M., and Hardt, W.
(2004). Rapid prototyping of real-time control laws
for complex mechatronic systems a case study. In The
Journal of Systems and Software, volume 70, pages
263–274.
Fernandes, J. M., Adamski, M., and Proenca, A. J. (1997).
VHDL generation from hierarchical petri net specifi-
cations of parallel controllers. In IEE Proceedings-
E Computers and Digital Techniques, volume 144,
pages 127–137.
Grono, A. J. (2001). Synchronizing generator with HITL
simulations. In IEEE Computer Applications in
Power, pages 43–46. IEEE.
Hafner, M., Jost, O., and Isermann, R. (2002). Mechatronic
design approach for engine management systems. In
Mechatrnoics, volume 12, page 10351046. Elsevier.
Hannan Bin Azhar, M. A. and Dimond, K. R. (2002). De-
sign of an fpga based adaptive neural controller for
intelligent robot navigation. In Euromicro Symposium
on Digital System Design, volume 00, pages 283–295.
Hernandez, A., Urena, J., Garcia, J., Mazo, M., Hernanz,
D., Derutin, J., and Serot, J. (2004). Ultrasonic rang-
ing sensor using simultaneous emissions from differ-
ent transducers. In IEEE Transactions On Ultrasonics,
Ferroelectrics, And Frequency Control, volume 51,
pages 1660–1670.
Hong-Tzong, Y., Ming-Tzong, L., Yao-Ter, C., and Kuo-
Chin, Y. (2005). Design and implementation of
real-time nurbs interpolator using a FPGA-based mo-
tion controller. In IEEE International Conference on
Mechatronics (ICM2005), pages 56–61, Taipei, Tai-
wan.
Huang, S. J., Yang, T., and Huang, J. (2002). Fpga real-
ization of wavelet transform for detection of electric
power system disturbances. In IEEE Transactions On
Power Delivery, volume 17, pages 388–394.
Isermann, R. and M ¨uller, N. (2003). Design of computer
controlled combustion engines. In Mechatrnoics, vol-
ume 13, page 10671089. Elsevier.
Isermann, R., Schaffnit, J., and Sinsel, J. (1999). Hardware-
in-the-loop simulation for the design and testing of
engine-control systems. In Control Engineering Prac-
tice, volume 7, pages 643–653. Elsevier.
Kalte, H., Porrmann, M., and R
¨
uckert, U. (2000). Us-
ing a dynamically reconfigurable system to accel-
erate octree based 3d graphics. In Proceedings
of the International Conference on Parallel and
Distributed Processing Techniques and Applications
(PDPTA2000), volume 5, pages 2819–2824, Monte
Carlo Resort, Las Vegas, Nevada, USA.
Kalte, H., Porrmann, M., and R
¨
uckert, U. (2002). A pro-
totyping platform for dynamically reconfigurable sys-
tem on chip designs. In Proceedings of the IEEE
Workshop Heterogeneous reconfigurable Systems on
Chip (SoC), Hamburg, Germany.
Lian, K. L. and Lehn, P. W. (2005). Real-time simulation
of voltage source converters based on time average
method. In IEEE Transactions On Power Systems,
volume 20, pages 110–118. IEEE.
Lin, C. F., Tseng, C., and Tseng, T. (2006). A hardware-
in-the-loop dynamics simulator for motorcycle rapid
controller prototyping. In Control Engineering Prac-
tice. Elsevier.
Nascimento, P. S. B., Pand Maciel, P. R. M., Lima, M. E.,
Sant’ana, R. E., and Filho, A. G. S. (2004). A par-
tial reconfigurable architecture for controllers based
on petri nets. In SBCCI ’04: Proceedings of the 17th
symposium on Integrated circuits and system design,
pages 16–21, New York, NY, USA. ACM Press.
Paiz, C., Kettelhoit, B., Klassen, A., and Porrmann, M.
(2005). Dynamically reconfigurable hardware for dig-
ital controllers in mechatronic systems. In IEEE In-
ternational Conference on Mechatronics (ICM2005),
Taipei, Taiwan.
Pohl, C., Franzmeier, M., Porrmann, M., and R
¨
uckert,
U. (2004). gnbx - reconfigurable hardware accel-
eration of self-organizing maps. In Proceedings of
the IEEE International Conference on Field Program-
mable Technology (FPT’04), pages 97–104, Brisbane,
Australia.
Shiakolas, P. and Piyabongkarn, D. (2003). Development of
a real-time digital control system with a hardware-in-
the-loop magnetic levitation device for reinforcement
of controls education. In Education, IEEE Transac-
tions on, volume 46, pages 50–60. IEEE.
Tazi, K., Monmasson, E., and Louis, J. P. (1999). Descrip-
tion of an entirely reconfigurable architecture dedi-
cated to the current vector control of a set of ac ma-
chines. In IEEE International Conference on Indus-
trial Electronics, Control, and Instrumentation, vol-
ume 3, pages 1415–1420.
Terwiesch, P., Keller, T., and Scheiben, E. (1999). Rail ve-
hicle control system integration testing using digital
hardware-in-the-loop simulation. In Transactions On
Control Systems Technology, volume 7, pages 352–
362. IEEE.
Tessier, R. and Burleson, W. (2001). Reconfigurable com-
puting for digital signal processing: A survey. In Jour-
nal of VLSI Signal Processing, volume 28, pages 7–
27. Elsevier.
Woo, W., Miller, M., and Kenney, J. S. (2005). A hybrid
digital RF envelope predistortion linearization system
for power amplifiers. In IEEE Transactions On Mi-
crowave Theory And Techniques, volume 53, pages
229–237.
Yue, X., Vilathgamuwa, D. M., and Tseng, K. (2005). Ro-
bust adaptive control of a three-axis motion simulator
with state observers. In IEEE/ASME Transactions On
Mechatronics, volume 10, pages 437–448. IEEE.
ICINCO 2006 - SIGNAL PROCESSING, SYSTEMS MODELING AND CONTROL
46