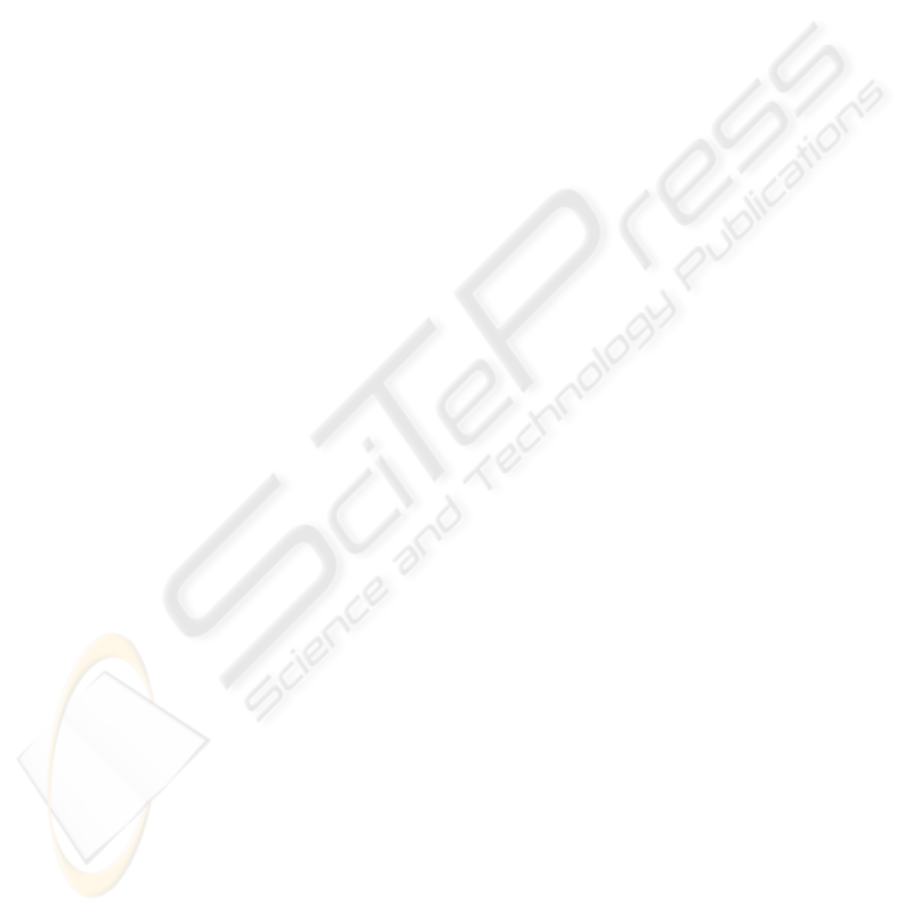
5 Conclusions and Future Work
In this paper, non-linear attractor dynamics was used as a tool to design a distributed
control architecture that enables a team of three robots to transport a large object. It was
assumed that the robots have no prior knowledge of the environment. The choice of the
control variables and parameters have taken into account the physical mobile robots at
which the architecture will be implemented. The amount of information communicated
among robots is minimal. The overall control system is flexible, since planning solu-
tions may change based on changes in sensed world and/or communicated information.
The leader broadcast its heading direction and path velocity (codified in 2 bytes) and
each helper share among them 3 values represented by 3 bytes. The control architec-
ture was evaluated through computer simulations. The global behavior is stable and
trajectories are smooth. Very important, the ability to avoid collisions with either static
or dynamic obstacles have been demonstrated. Future work consist on implementation
and validation on the physical robots.
Acknowledgements
This work was supported, in part, through grant POSI/SRI/38051/2001 from the Por-
tuguese Foundation for Science and Technology (FCT), FEDER and PRODEP III. We
wish to thank to W.Erlhagen, S.Monteiro, L.Louro, N.Hip
´
olito, A.Moreira, T.Machado.
References
1. Ahamadabadi M. and Nakano E. ”A cooperative multiple robot system for object lifting
and transferring tasks”. In Proc. ROBOMECH’96, Annual Conf. of The Japanese Society
of Mechanical Eng. on Robotics and Mechatronics, 1996.
2. Aiyama Y. et al. ”Cooperative transportation by two four-legged robots with implicit com-
munication”. Robotics and Autonomous Systems, 1999.
3. Bicho E., Mallet P. and Sch
¨
oner G. ”Target representation on an autonomous vehicle with
low level sensors”. The Int. Jou. of Robotics and Research, 19(5):424-447, 2000.
4. Ahmadabadi M. and Nakano E. ”A constrain and move approach to distributed object ma-
nipulation”. IEEE Transactions on Robotics and Automation, 17(2):157-172, 2001.
5. Chaimowicz L., Sugar T., Kumar V. and Campos V. ”An architecture for tightly coupled
multi-robot cooperation”. in Proc. IEEE ICRA, 2292-2297, 2001.
6. Soares R., Bicho E. ”Using Attractor Dynamics to Generate Decentralized Motion Control
of Two Robots Transporting a Long Object in Coordination”. Proc. of the 2002 IEEE/RSJ
Intl. Conf. on Intelligent Robots and Systems, EPFL, Lausanne, 2002.
7. Bicho E. ”Dynamic approach to Behavior-Based Robotics: design, specification, analysis,
simulation and implementation”. Shaker Vergal, 2000.
8. Bicho E., Louro L., et al. ”Coordinated transportation with minimal explicit communication
between robots”. 5th IFAC Symp. on IAV, Lisbon, Portugal, July 5-7, 2004.
9. Wang Z., Takano Y., Hirata Y. and Kosuge K. ”From Human to Pushing Leader Robot:
Leading a Decentralized Multirobot System for Object Handling”. in Proc. IEEE Int. Conf.
Robotics and Biomimetics, 2004.
10. Hirata Y., Kume Y., Sawada T., Wang Z. and Kosuge K. ”Handling of an object by multiple
mobile manipulators in coordination based on caster-like dynamics”. in Proc. IEEE Int.
Conf. Robotics and Automation, 807-812, 2004.
79