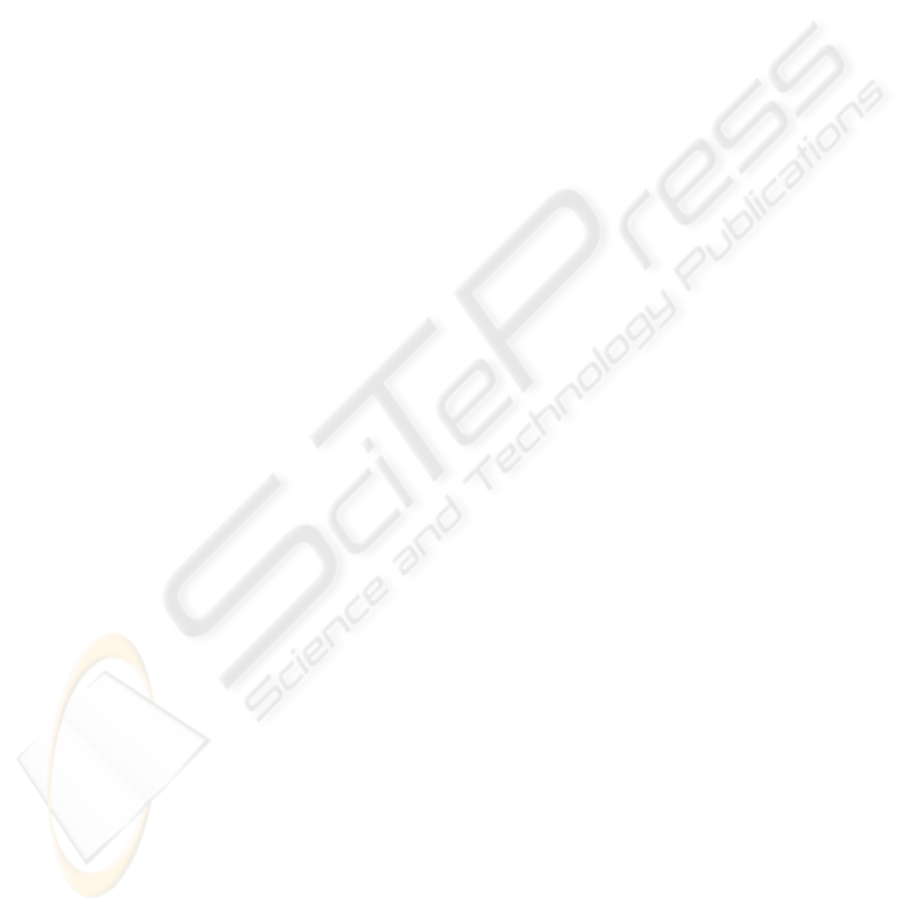
6 CONCLUSION AND FUTURE
WORK
In this paper, we present a physical-based deforma-
tion method. When working with our deformation
method, the designer does not need to manipulate
some non-intuitive mathematical shape parameters,
such as control points and control vectors. Instead,
he/she can work with the point constraints and
spline-based constraints, therefore designers can
easily and intuitively control the resultant shape.
The potential function is centered at the con-
straint and it symmetrically distributes the so-called
force energy. Compared with other deformation
methods, this approach has the following advantages:
intuition, locality and simplification since this
method combines shape creation and deformation.
Finally, it is possible to use various intensities and
smoothing functions to enrich the quality and accu-
racy of the deformation.
Although our method is intuitive and less compu-
tationally challenging for free form surface modeling
and styling, it still needs some time to create sophis-
ticated models; and there is a limitation in our de-
formation technique when we want to change the
topology of the model, such as creating a hole.
In the future work, we will further investigate in-
telligent operations for shape editing and multi-
surfaces modeling based on 3D sketching; such as
surface splitting and stitching. We also plan to im-
prove the connectivity and continuity between dif-
ferent surfaces based on declarative constraints.
ACKNOWLEDGEMENT
This research presented in this paper is a part of EU
project “IMPROVE” and of the Part of the project
InSIDe.
REFERENCES
Barr, A. H.,1984 , “Global & local deformations of solid
primitives,” Computer Graphics, 18(3), 21-30.
Güdükbay, U. and Üzgüç, B., 1990, “Free-form solid
modeling using deformations,” Computer Graphics,
14(3/4), 491-500.
Sederberg, T. W. and Parry, R.,1986, “Free-form deforma-
tions of solid geometric models,” ComputerGraphic,
20(4), 151-160.
Coquillart, S., 1990, “Extended free-form deformation: A
sculpting tool for 3D geometric modeling,” Computer
Graphics, 24(4), 187-196.
Bechmann, D., 1994, “Space deformation models survey,”
Computer & Graphics, 18(4), 571-586.
Kalra, P., Mangili A. and Thalmann, N., 1992, “Simula-
tion of facial muscle actions based on rational free-
form deformation,” Computer Graphics Forum, 2(3),
59-69.
Lamousin, H. J. and Waggenspack, W. N., 1994, “NURBS
based freeform deformation,” IEEE Computer Graph-
ics & Applications, 14(6), 59-65.
Griessmair, J. and Purgathofer, W., 1989, Deformation of
solids with trivariate B-spline,” Proc.
EUROGRAPHICS’89, 137-148.
Coquillart S. and Jancene, P., 1991, “Animated free-form
deformation: an interactive animation technique,”
Computer Graphics, 25(4), 23-26.
Chadwick, J. E., Haumann, D. and Parent, R. E., 1989,
“Layered construction for deformable animated char-
acters,” Computer Graphics, 23(3), 243-252.
Borrel, P. and Rappoport, A., 1994, “Simple constrained
deformations for geometric modeling and interactive
design,” ACM Transactions on Graphics, 13(2), 137-
155.
Xiaogang, J., Youfu L. and Qunsheng, P. , 2000, “General
constrained deformation based on generalized meta-
balls,” Computer & Graphics, 24(2), 219-231.
Léon, J. C. and Veron, P., 1997, “Semiglobal deformation
and correction of free-form surface using a mechanical
alternative,” The Visual Computer, 13(3), 109-126.
Léon, J. C. and Trompette, P. , 1995, “A new approach
towards freeform surfaces control,” C.A.G.D, 12(4),
395-416.
Léon, J. C., 1991, “Modé lisation des courbes et des surfa-
ces pour la CFAO,” hermès, paris.
Li, Han, Giuseppe, Conti, Raffaele, De. Amicis (2005),
“Freehand 3D curve recognition and oversketching,”
Eurographics UK Chapter 2005,187-193.
Chesutet, V. and Catalano, C.E., Pernot, J. P. “ 3D
Sketching with Fully Free Form Deformation
Features for Aesthetic Design.”
EUROGRAPHICS Workshop, Sketch-based In-
terfaces and Modeling, 2004, 9-18.
Michalik, P. and Brüderlin, B.D., “Constraint-based De-
sign of B-spline Surface from Curves.” ACM Sympo-
sium on Solid Modeling and Applications, 2004, 213-
220.
DIETZ, U. , “Creation of Fair B-Spline Surface Fillets” In
Creating Fair and Shape Preserving Curves and Sur-
faces. B.G. Teubner, Stuttgart, 1998. 2, 3, 8
Fontana, M., Giannini, F., Meirana, F., “Free Form Fea-
tures for Aesthetic Design.” Int. Jou. Shape Modelling,
vol. 6, n°2, 2000, 273-302.
ADAPTIVE CONSTRAINT AND 3D SKETCH-BASED DEFORMATION FOR INTERACTIVE FREE FORM
SURFACE STYLING
399