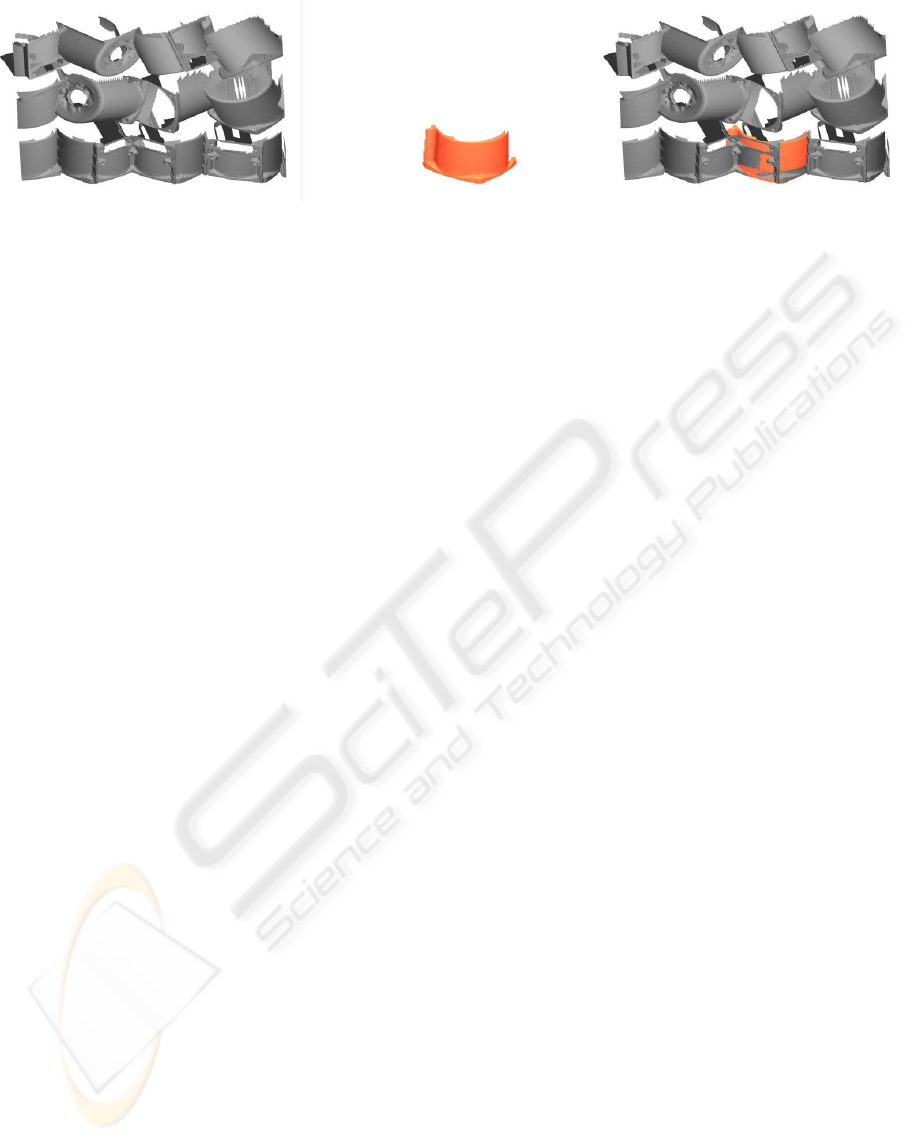
(a) The scene. (b) The (rotated and translated)
sub-model that matched best.
(c) The scene and transformed sub-model
overlaid.
Figure 8: Depiction of a correct 5 degree of freedom pose estimation.
REFERENCES
Balslev, I. and Eriksen, R. D. (2002). From belt picking to
bin picking. Proceedings of SPIE - The International
Society for Optical Engineering, 4902:616–623.
Berger, M., Bachler, G., and Scherer, S. (2000). Vi-
sion Guided Bin Picking and Mounting in a Flexi-
ble Assembly Cell. In Proceedings of the 13th In-
ternational Conference on Industrial & Engineering
Applications of Artificial Intelligence & Expert Sys-
tems, IEA/AIE2000, pages 109–118, New Orleans,
Louisiana, USA.
Boughorbel, F., Zhang, Y., Kang, S., Chidambaram, U.,
Abidi, B., Koschan, A., and Abidi, M. (2003). Laser
ranging and video imaging for bin picking. Assembly
Automation, 23(1):53–59.
Bronstein, A. M., Bronstein, M. M., Gordon, E., and Kim-
mel, R. (2003). High-resolution structured light range
scanner with automatic calibration. Technical report,
Technion - Israel Institute of Technology.
Curless, B. (2000). Overview of active vision technologies.
3D Photography - Course Notes ACM Siggraph ’00.
Frome, A., Huber, D., Kolluri, R., Bulow, T., and Malik,
J. (2004). Recognizing objects in range data using
regional point descriptors. In European Conference
on Computer Vision (ECCV), pages 224–237, Prague,
Czech Republic.
Ghita, O. and Whelan, P. F. (2003). A bin picking system
based on depth from defocus. Machine Vision and
Applications, 13(4):234–244.
Kazhdan, M., Funkhouser, T., and Rusinkiewicz, S. (2003).
Rotation invariant spherical harmonic representation
of 3d shape descriptors. In SGP ’03: Proceedings
of the 2003 Eurographics/ACM SIGGRAPH sympo-
sium on Geometry processing, pages 156–164, Sar-
dinia, Italy.
Kirkegaard, J. (2005). Pose Estimation of Randomly Orga-
nized Stator Housings using Structured Light and Har-
monic Shape Contexts. Master’s thesis, Lab. of Com-
puter Vision and Media Technology, Aalborg Univer-
sity, Denmark.
Moeslund, T. B. and Kirkegaard, J. (2005). Pose estimation
of randomly organised stator housings with circular
features. In Scandinavian Conference on Image Anal-
ysis, Joensuu, Finland.
Posdamer, J. L. and Altschuler, M. D. (1982). Surface mea-
surement by space-encoded projected beam systems.
Computer Graphics and Image Processing, 18(1):1–
17.
Saldner, H. (2003). Palletpicker-3d, the solution for pick-
ing of randomly placed parts. Assembly Automation,
23(1):29–31.
Salvi, J., Pags, J., and Battle, J. (2004). Pattern codification
strategies in structured light systems. Pattern Recog-
nition, 37(4):827–849.
Schraft, R. D. and Ledermann, T. (2003). Intelligent picking
of chaotically stored objects. Assembly Automation,
23(1):38–42.
Schwarte, R., Heinol, H., Buxbaum, B., Ringbeck, T., Xu,
Z., and Hartmann, K. (1999). Principles of Three-
Dimensional Imaging Techniques in ”Handbook of
Computer Vision and Applications”, volume 1. The
Academic Press, first edition.
Torras, C. (1992). Computer Vision - Theory and Industrial
Applications. Springer-Verlag, first edition.
Trucco, E. and Verri, A. (1998). Introductory Techniques
for 3D Computer Vision. Prentice Hall, first edition.
Valkenburg, R. J. and McIvor, A. M. (1998). Accurate 3d
measurement using a structured light system. Image
and Vision Computing, 16(2):99–110.
www.grundfos.com (2005).
VISAPP 2006 - IMAGE UNDERSTANDING
108