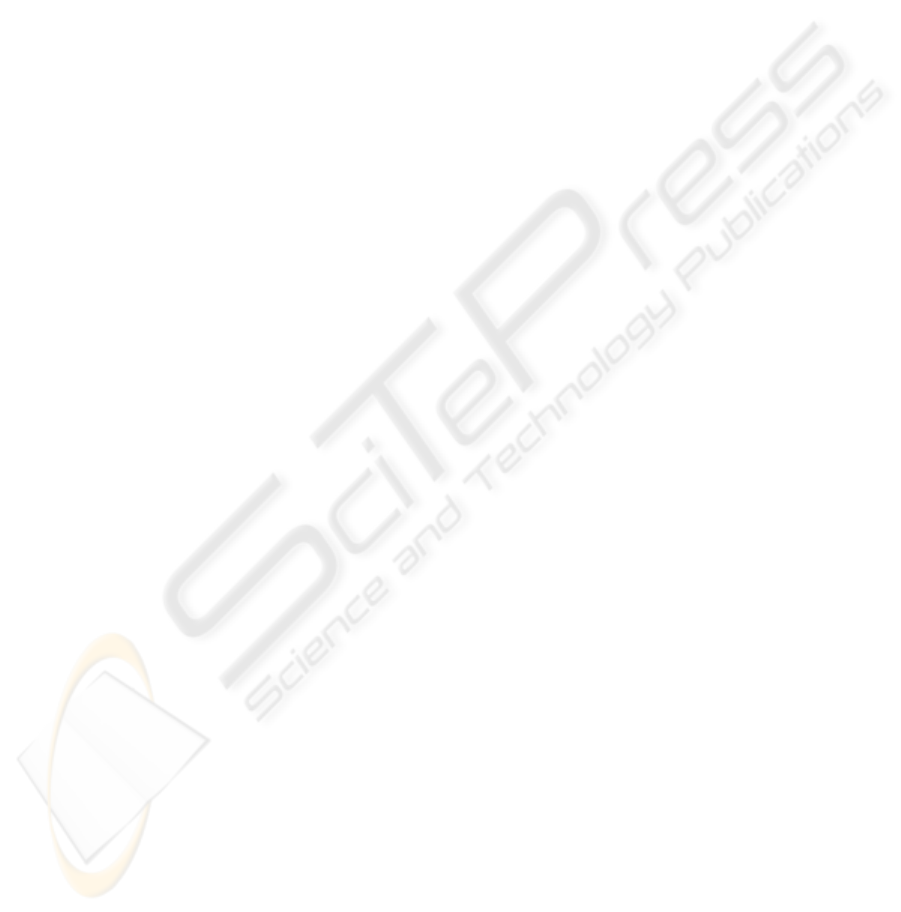
3 COMPARISON OF 3D
SCANNERS ON THE MARKET
The manufacturers of 3D scanning equipment can be
grouped in three categories; those that provide the
hardware, those that write the software and those
that implement both systems. We looked at the
leading manufactures of 3D scanners and this
enabled us to make a comparison of their various
products. Given that these use different technologies
these results are not easily compared since we have
to identify uniform parameters for comparison in
each of the methods. Owing to the variations in
software available on the market, the survey has
been limited to the comparison of the hardware and
its performance. Definitely their performance
depends greatly on the software, but that will be
dealt with in another article.
The providers of scanners that we have been able
to identify, that use each of the various technologies
for 3D reconstruction are diverse. A look is taken at
those who provide the datasheets on their products.
Using these, a comparison of similar parameters is
carried out to come up with unbiased conclusions.
The scanners are commercial implying that we
have had to rely on the information provided by their
manufacturers, as it is close to impossible to have all
scanners in the university laboratory considering
their high cost. The parameters taken into
consideration were; the operating range, accuracy,
speed of capture, and the types of surfaces. Each
scanner will be compared with a series of cameras in
the same range. This will be followed by a
comparison of with the results from other scanning
techniques. The survey looked at products from the
following companies: 3D Scanners (MMZ), Konica
Minolta (VIVID 700), Optimet technologies
(Conoline), Opton formerly EOIS (Moiré scanners),
Roland (Pix 30) among others.
Table 1. shows these parameters in several
commercial scanners. Judging from the results
presented, several observations about the various
technologies can be made. Laser triangulation is the
commonest method used in 3D scanners, as seen in
the table most scanners use triangulation. The
reasons that are put forward for its popularity are;
it’s easy setup, its low cost as compared to other
methods, its speed which enables real time scans and
reconstructions on the production line. Laser
triangulation is limited when very high precision and
accuracy are required. It is also marred by speckle
and inability to scan reflective surfaces.
Stereo is passive and does not emit any radio or
light energy. Recording on site can be done very fast
and as such it can be used on-line. However, the
matching of the points in the two images captured by
the cameras in stereo is tedious. Whereas they can
adjust for component size, stereo cannot easily
accommodate free form surfaces. In addition, the
requirement for one of the two cameras to be fixed
at a specific angle restricts the inspection region and
presents difficulty in inspecting the entire
component. The scene has to be rigid to begin
reconstruction which makes it difficult for on-line
implementation.
Moiré is considered a very good method for 3D
reconstructions because it amplifies small errors,
thus enabling their detection. It requires less
computer time than other methods like laser
triangulation during capture, once it has been
properly setup, and so has a great potential for rapid
on-line registration and inspection. The parameters
of a moiré can easily be changed. Moiré limitations
can be cited in the difficulty in its design and in
adjusting the setup to capture data. Its very high
precision makes the acquisition costs extremely
prohibitive (Dubowsky , S).
Holography performs much better than laser
triangulation when it comes to precision and
accuracy. Readings of up to several microns can be
taken. However it is limited as far as speed is
concerned. A lot of precaution has to be taken when
recording the holograms since lengthy exposure
requires a high level of stability in order to obtain
good results in the processing. The range for
recording the holograms also has to be well chosen
in order to get a good reconstruction. Holography
has not been fully taken on in industry inspite of
being very accurate, given the complication in
adjustments that have to be made while taking
readings.
Conoscopic holography being a modification to
holography sorts out the speed problem. It features a
high precision in its readings and reconstructions of
up to 47 microns using an objective of focal length
100mm. The accuracy and range depend on the
objectives used on the conoline. Conoscopic
holography has clearly enabled holography to be
applied to the manufacturing industry. Of the
benefits we are able to note using the conoline is the
ability to measure several surfaces and reach an
angle of incidence up to 85º, which not many
methods are capable of doing. Conoscopic
holography could still benefit from an increase in its
speed of capture in order to be adapted to more real
time applications. (Optimet)
VISAPP 2006 - MOTION, TRACKING AND STEREO VISION
462