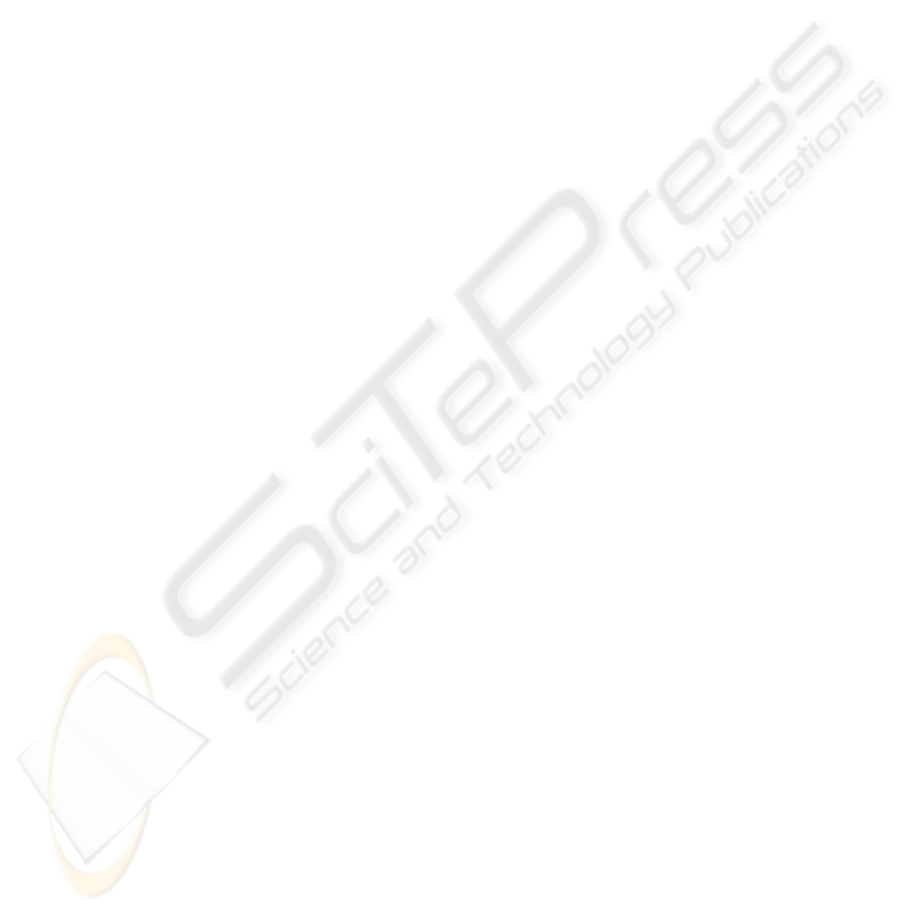
coordinates of the pixel or sub-pixel matching. The
function linking the 3D points to the 2D points is
obtained and a local bilinear interpolation is carried
out to get the 3D/2D matchings for points which 3D
coordinates are known.
Three main perspectives of work are envisaged.
• The first one consists in developing analytical pro-
cedures which enable the correction of the mis-
alignment of the two sensors and the misalignment
between the optical axis and the vertical axis of the
frame of the test-pattern.
• The second one is linked to the development of an
analytical calibration method which is based on the
minimization of a criterion function. This function
is defined as the non-linear equation linking a 3D
point considered in the environment and a 2D point
on the image plane (Svoboda, 1999). We propose
to use the Levenberg-Marquardt algorithm which
is a classical optimization technique for non-linear
equation.
• The third one deals with the self-calibration of the
panoramic stereovision sensor. It consists in the es-
tablishment of the fundamental and essential matri-
ces. This calibration method is linked to the epipo-
lar geometry which enables the matchings of pixels
in different image planes. This geometry is well
known for classical vision systems and has been
recently established for catadioptric sensors (Svo-
boda, 1999).
REFERENCES
Aliaga, D. (2001). Accurate catadioptric calibration for
real-time pose estimation inroom-size environments.
In 8th IEEE International Conference on Computer
Vision, volume 1, pages 127–134.
C. Cauchois, E. Brassart, C. P. and Clerentin, A. (1999).
Technique for calibrating an omnidirectional sensor.
In International Conference on Intelligent Robots and
Systems.
C. Drocourt, L. Delahoche, E. B. and Cauchois, C. (2001).
Simultaneous localization and map building paradigm
based on omnidirectional stereoscopic vision. In Pro-
ceeding IEEE Workshop on Omnidirectional Vision
Applied to Robotic Orientation and Nondestructive
Testing, pages 73–79.
C. Geyer, K. D. (2001). Catadioptric projective geometry.
International Journal of Computer Vision, 43:223–
243.
F. Marzani, Y. Voisin, A. D. and Voon, L. F. L. Y. (2002).
Calibration of a 3d reconstruction system using a
structured light source. Journal of Optical Engineer-
ing, 41:484–492.
Faugeras, O. (1993). Three-dimensional computer vision
: a geometric viewpoint. MIT Press, Cambridge,
Massachusetts, 4th edition.
G.L. Mariottini, D. P. (2005). The epipolar geometry tool-
box : multiple view geometry for visual servoing for
matlab. IEEE Robotics and Automation Magazine.
J. Fabrizio, J.-P. Tarel, R. B. (2002). Calibration of
panoramic catadioptric sensors made easier. In Work-
shop on Omnidirectional Vision.
J.P. Barreto, H. A. (2005). Geometric properties of central
catadioptric line images and their application in cali-
bration. IEEE Transactions on Pattern Analysis and
Machine Intelligence, 27:1327–1333.
Kang, S. (2000). Catadioptric self-calibration. In Inter-
national Conference on Computer Vision and Pattern
Recognition, volume 1, pages 201–207.
L. Smadja, R. Benosman, J. D. (2004). Cylindrical sensor
calibration using lines. In 5th Workshop on Omnidi-
rectional Vision, Camera Networks and Non-Classical
Cameras, pages 139–150.
Lacroix, S., Gonzalez, J., El Mouaddib, M., Vasseur, P.,
Labbani, O., Benosman, R., Devars, J., and Fabrizio,
J. (2005). Vision omnidirectionnelle et robotique. rap-
port final. Technical report, LAAS, CREA, LISIF.
Moldovan, D. (2004). A geometrically calibrated pinhole
model for single viewpoint omnidirectional imaging
systems. In British Machine Vision Conference.
Mouaddib, M. E. (2005). La vision omnidirectionnelle. In
Journée Nationale de la Recherche en Robotique.
P. Biber, H. Andreasson, T. D. and Andreas, A. S. (2004).
3d modeling of indoor environments by a mobile ro-
bot with a laser scanner and panoramic camera. In
IEEE/RSJ International Conference on Intelligent Ro-
bots and Systems.
S. Baker, S. N. (1999). A theory of single-viewpoint cata-
dioptric image formation. International Journal of
Computer Vision, 35:175–196.
S. Baker, S. N. (2001). Panoramic Vision: Sensors, The-
ory and Applications, chapter Single viewpoint cata-
dioptric cameras, pages 39–73. Springer-Verlag, 1st
edition.
Svoboda, T. (1999). Central panoramic cameras. Design,
geometry, egomotion. PhD thesis, Czech Technical
Univeristy.
T. Ea, O. Romain, C. G. and Garda, P. (2001). Un capteur
de sphéréo-vision stéréoscopique couleur. In Congrès
francophone de vision par ordinateur ORASIS.
T. Svoboda, T. Pajdla, V. H. (1998). Epipolar geometry for
panoramic cameras. In 5th European Conference on
Computer Vision, volume 1406, pages 218–232.
X. Ying, Z. H. (2003). Catadioptric camera calibration us-
ing geometric invariants. In International Conference
on Computer Vision, pages 1351–1358.
Zhu, Z. (2001). Omnidirectional stereo vision. In 10th IEEE
ICAR Workshop on Omnidirectional Vision.
VISAPP 2006 - IMAGE FORMATION AND PROCESSING
18