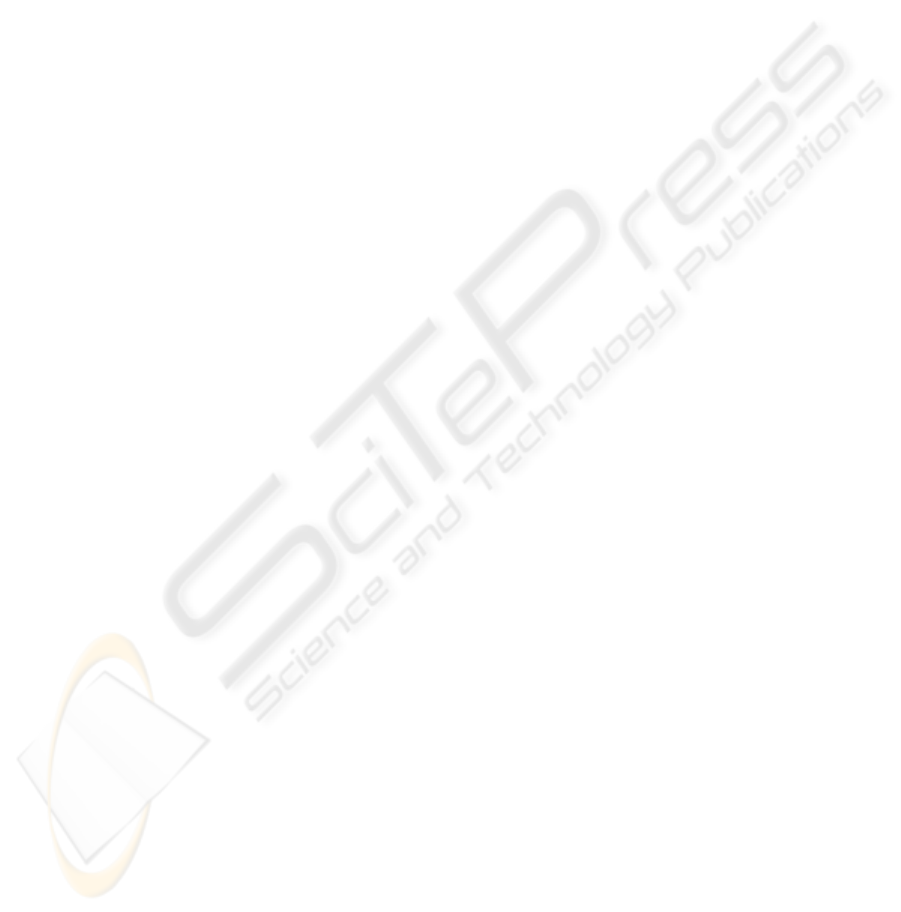
vegetables supply chain, so that its image of
“freshness” in its products is enhanced. By using the
system described above, the company aims at
achieving small batch frequent deliveries in its shops
through three regional distribution centres. This
diverts from its previous operations where large
quantities of fruits and vegetables were delivered
and stored in one refrigerated warehouses before
being distributed to the selling points.
Using Co-LEAN, the supermarket chain can now
adjust deliveries to current demand, thus avoiding
costly and risky inventories at both the warehouse
and the shops. In addition, it can adjust the fruit and
vegetable picking rates of the suppliers. By feeding
Co-LEAN-PE with a weighted mix of forecasted and
actual demand, the required rates are calculated and
broadcasted to all suppliers, including the suppliers
of packaging materials (Fig. 4). Deliveries are
optimised using the Relations Manager to exploit
any slack delivery capacity of suppliers, thus
reducing the overall cost (Fig. 6). The Relations
Manager has also helped in overcoming the
inabilities of specific suppliers to deliver caused by
bad weather. Alternative suppliers have been
engaged in the most efficient way. The Co-SISC and
Co-INOV tools have been used in the initial design
of the supply chain, thus providing full transparency
to all parties involved. Co-SOLVE, Co-MASS and
Co-INOV have been used for developing in a
collaborative manner new packages which are
convenient for home deliveries of orders placed
though the internet. At next stage, the same
supermarket chain plans to use the Co-LEAN suite
in a more demanding area, that of its own-label
products produced by third-party manufacturers
under its control.
5 CONCLUSIONS
In this paper we presented Co-LEAN, an integrated
suite of software tools suitable for the design and
operation of lean supply chains. In addition to
providing full operational support in the planning
and execution of the lean supply chain, including
production and logistics optimisation, though its Co-
LEAN-PE tool, the suite supports internet-based
collaboration in the innovation and product design
(Co-INOV), manufacturing strategy (Co-MASS),
and supply-chain design and improvement tasks
(Co-SOLVE, Co-SISC). The pilot application of Co-
LEAN has provided an early indication of its
usefulness in a specific application area (retailing).
We are expecting that additional installations will
trigger modifications and adjustments that will, in
turn, lead to a more flexible and widely applicable
system.
REFERENCES
Adamides, E.D. and N. Karacapilidis (2005a). Knowledge
management and collaborative model building in the
strategy development process, Knowledge and Process
Management, 12(2), 77-88.
Adamides, E.D. and N. Karacapilidis (2005b). Information
technology support for the knowledge and social
processes of innovation management, Technovation,
Article in Press.
Barratt, M. (2004). Understanding the meaning of
collaboration in the supply chain, Supply Chain
Management, 9, 30-42.
Cox, A. (2004). The art of the possible: relationship
management in power regimes and supply chains,
Supply Chain Management, 9, 346-356.
Duggan, K.J. (2002). Creating Mixed Model Value
Streams: Practical Lean Techniques for Building to
Demand, Productivity Press, New York.
Evans, P. and B. Wolf (2005). Collaboration rules,
Harvard Business Review, 83(7), 96-104.
Hines, P. and N. Rich (1997). The seven value stream
mapping tools, International Journal of Operations
and Production Management, 17, 46-64.
Hines, P., M. Holweg and N. Rich (2004). Learning to
evolve: A review of contemporary lean thinking,
International Journal of Operations and Production
Management, 24, 994-1011.
Holweg, M., S. Disney, J. Holmstrom, and J. Smaros
(2005). Supply chain collaboration: Making sense of
the strategy continuum, European Management
Journal, 22, 170-181.
Jones, D.T., P. Hines and N. Rich (1997). Lean logistics,
International Journal of Physical Distribution and
Logistics Management, 27, 153-173.
Karacapilidis, N., E. Adamides and Ch. Evangelou (2003).
Leveraging organizational knowledge to formulate
manufacturing strategy, 11th European Conference on
Information Systems, Naples, June, CD of Conference
Proceedings.
Karacapilidis, N.I., Adamides, E.D. and Pappis, C. (2004).
An IS framework to support the collaborative design
of supply chains, Proceedings of KES 2004, 62-70
Kehoe, D. and N. Boughton (2001). Internet based supply
chain management: A classification of approaches to
manufacturing planning and control, International
Journal of Operations and Production Management,
21, 516-524.
Kerrin, M. (2002). Continuous improvement along the
supply chain: the impact of customer-supplier
relations, Integrated Manufacturing Systems, 13, 141-
149.
Leonard, D. and S. Sensiper (2003). The role of tacit
knowledge in group innovation, in: Choo, C.W. and
Bontis, N. (Eds.), The Strategic Management of
TOWARDS AN INTEGRATED IS FRAMEWORK FOR THE DESIGN AND MANAGEMENT OF LEAN SUPPLY
CHAINS
41