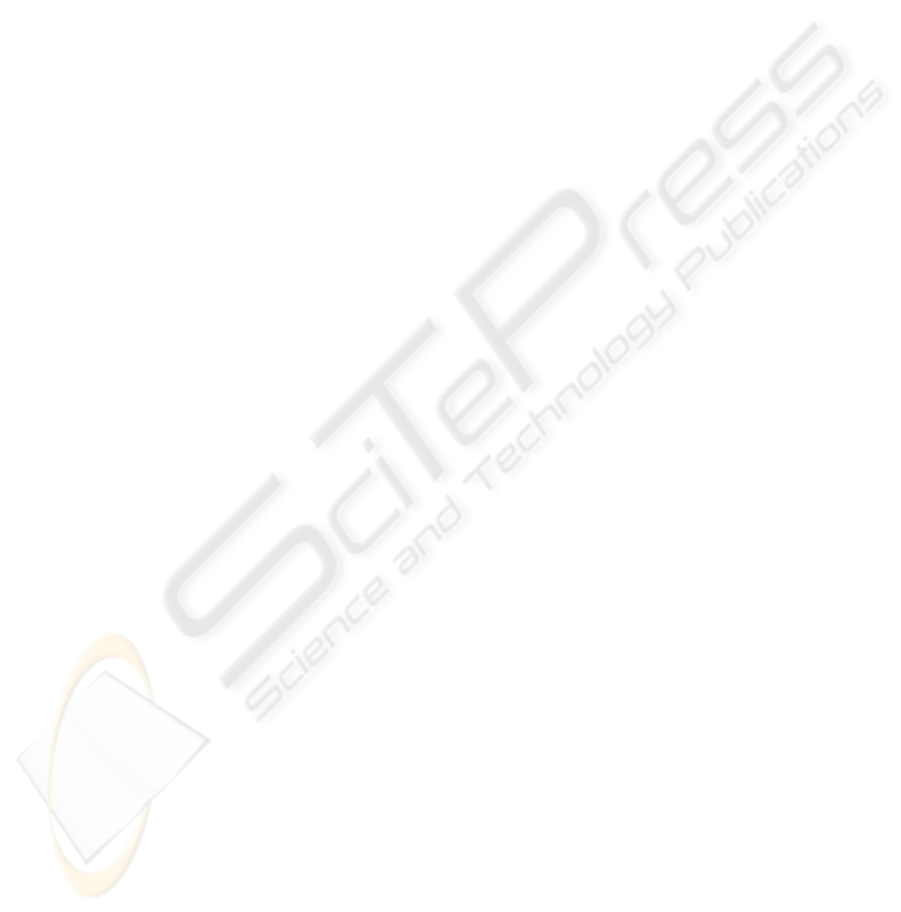
It is frequent to find two or more MAs or
registrations that differ just by product name from
one country to another. For example we can define
influenza (Flu) vaccines for entire Europe, but
during the structuring of the product information in
the e-TRAC, we should separate the products by
country.
R3: Validating the three data (Site of
Manufacturing, Shelf Life, Storage Condition) for
grippe in a particular region, requires the same data
values in e-TRAC reference frame for all countries
of this region, otherwise notify a compliance
exception.
Finally, within this Flu line product vaccines
case study, the applied architecture and its rules
provided an interesting solution by ensuring
compliance of 94,6% of the final products for the
used three data: Site of Manufacturing, Shelf Life,
and Storage Condition. One of the reasons of non-
total compliance is related to the existence of quality
level information in the MA system that has no
correspondence in the ERP system.
5 CONCLUSION
In this paper, we presented a methodology to
communicate between information systems. We
particularly focused on product structuring and
explained dependencies between product data in the
pharmaceutical field. Our main objective is to ensure
data compliance between two information systems,
one related to the Marketing Authorizations and the
other related to production, through the
establishment of communication architecture. We
based our work on the mapping between product
“states” information along the product
manufacturing life cycle. In spite of differences in
their business visions, both systems use the product
manufacturing decomposition as guide-line for
structuring the information.
Our methodology treats only the information
coming from Marketing Authorizations systems to
map and validate it in the ERP systems. However it
does not treat product information that exists in the
ERP systems and is not related to any MA system.
The next step of this work will focus on the
generalization of the used rules and constraints, not
only to extract or integrate data through reference
frames, but also between product states in a same
reference frame.
REFERENCES
ATHENA, 2005, “Second Version of State of the Art in
Enterprise Modelling Techniques and Technologies to
Support Enterprise Interoperability”, Version 1.3.1,
212 pages.
ATHENA, 2005, “Interoperability Roadmap up date”,
Version 1.0, 30 pages.
CTD Format: http://www.aboutctd.com/resource.htm and
http://www.ich.org/cache/html/1208-272-1.html,
accessed on October 2005.
EBXML, 2001, “Technical Architecture Specification
V1.0.4”, ebXML Technical Architecture Project Team,
39 pages
Gao X., Hayder A., Maropoulos P. G. and Cheung W. M.,
2003, “Application of product data management
technologies for enterprise integration”, International
Journal of Computer Integrated Manufacturing,
Taylor & Francis, Vol 16 N° 7-8, pages 491 – 500.
ICH6 - Sixth International Conference on Harmonisation,
2003, “New Horizons and Future Challenges”,
Summary Report, Osaka Japan, pages 13-15
International Conference on Harmonisation, Harmonised
Tripartite Guideline, 2000 “Organisation Of The
Common Technical Document For The Registration
Of Pharmaceuticals For Human Use”, International
Conference On Harmonisation Of Technical
Requirements For Registration Of Pharmaceuticals
For Human Use, 14 pages.
Sang Bong Y. and Yeongho K., 2002, "Web-based
knowledge management for sharing product data in
virtual enterprises", International Journal of
Production Economics, Volume 75, Issues 1-2, Pages
173-183
Schweigera R., Brumhardb M., Hoelzerc S., Dudecka J.,
2003,” Linking clinical data using XML topic maps”,
Artificial Intelligence in Medicine, Volume 28, Issue
1, Pages 105-115
Schweigera R., Brumhard M., Hoelzerc S., Dudecka J.,
2004, “Implementing health care systems using XML
Standards”, International Journal of Medical
Informatics (2005) 74, pages 267—277
U.S Food and Drug Administration, 2004,
“Pharmaceutical CGMPS For The 21st Century — A
Risk-Based Approach Final Report”, Department of
Health and Human Services, 32 pages
William C. Burkett, 2001, "Product data markup language:
a new paradigm for product data exchange and
integration", Computer-Aided Design, Volume 33,
Issue 7, Pages 489-500
ICEIS 2006 - DATABASES AND INFORMATION SYSTEMS INTEGRATION
86