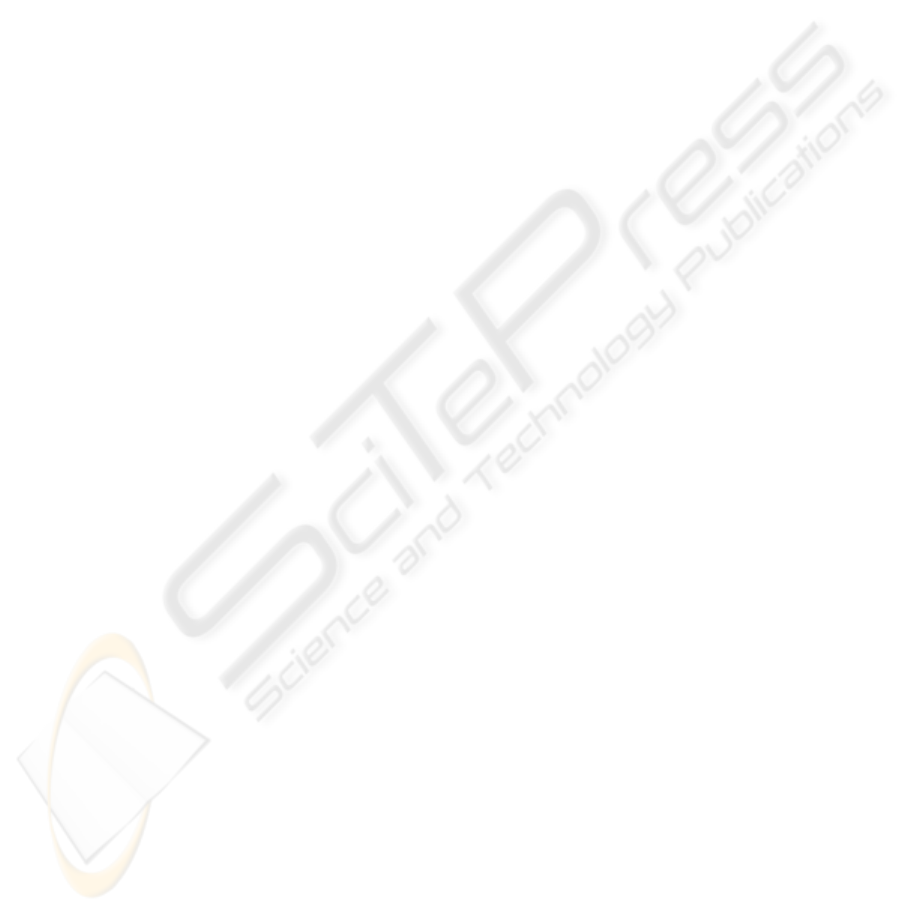
Simulation Modelling Performance Dynamics of Ship
Gas Turbine at the Load of the Ship’s
Synchronous Generator
Josko Dvornik
1
and Eno Tireli
2
1
Faculty of Maritime Studies, University of Split,
Zrinsko frankopanska 38, 21000 Split, Croatia
2
Faculty of Maritime Studies, University of Rijeka,
Studentska 2, 51000 Rijeka, Croatia
Abstract. Simulation modelling, performed by System Dynamics Modelling
Approach-MIT and intensive use of digital computers, which implies the
extensive use of, nowadays inexpensive and powerful personal computers
(PCs), is one of the most convenient and most successful scientific methods of
analysis of performance dynamics of nonlinear and very complex natural
technical and organizational systems [1].
The purpose of this work is to demonstrate the successful application of system
dynamics simulation modelling at analyzing performance dynamics of a
complex system of ship’s propulsion system.
Ship turbine generator is a complex nonlinear system which needs to be
analysed systematically, i.e. as an entirety composed of a number of sub-
systems and elements which are through cause-consequence links (UVP)
connected by retroactive circles (KPD), both within the propulsion system and
with the corresponding environment.
Indirect procedures of analysis of performance dynamics of turbine generator
systems used so far, which procedures are based on the use of standard, usually
linear methods, as Laplace’s transformation, transfer functions and stability
criteria, do not meet the current needs for information about performance
dynamics of nonlinear turbine generator systems.
Since the ship turbine generator systems are complex and the efficient
application of scientific investigation methods called qualitative and
quantitative simulation methodology of System dynamics will be presented in
this work. It will enable the production and application of more and varied
kinds of simulation models of the observed situations, and enable the
continuous computer simulation using high speed and precise digital
computers, which will significantly contribute to the acquisition of new
information about nonlinear characteristic of performance dynamics of turbine
generator systems in the process of designing and education.
Successful realization of this work, or qualitative and quantitative scientific
determination of a complex phenomenon of performance dynamics of load of
the ship electric network, or ship turbine generator system, will give a
significant scientific contribution to the fundamental and applied technical
scientific fields, and to interdisciplinary sub-directions of maritime transport,
exploitation of ship drive systems, mariners education, automatics, theory of
management and regulation, expert systems, intelligent systems,
computerization and information systems.
Dvornik J. and Tireli E. (2006).
Simulation Modelling Performance Dynamics of Ship Gas Turbine at the Load of the Ship’s Synchronous Generator.
In Proceedings of the 4th International Workshop on Modelling, Simulation, Verification and Validation of Enterprise Information Systems, pages
157-162
DOI: 10.5220/0002471301570162
Copyright
c
SciTePress