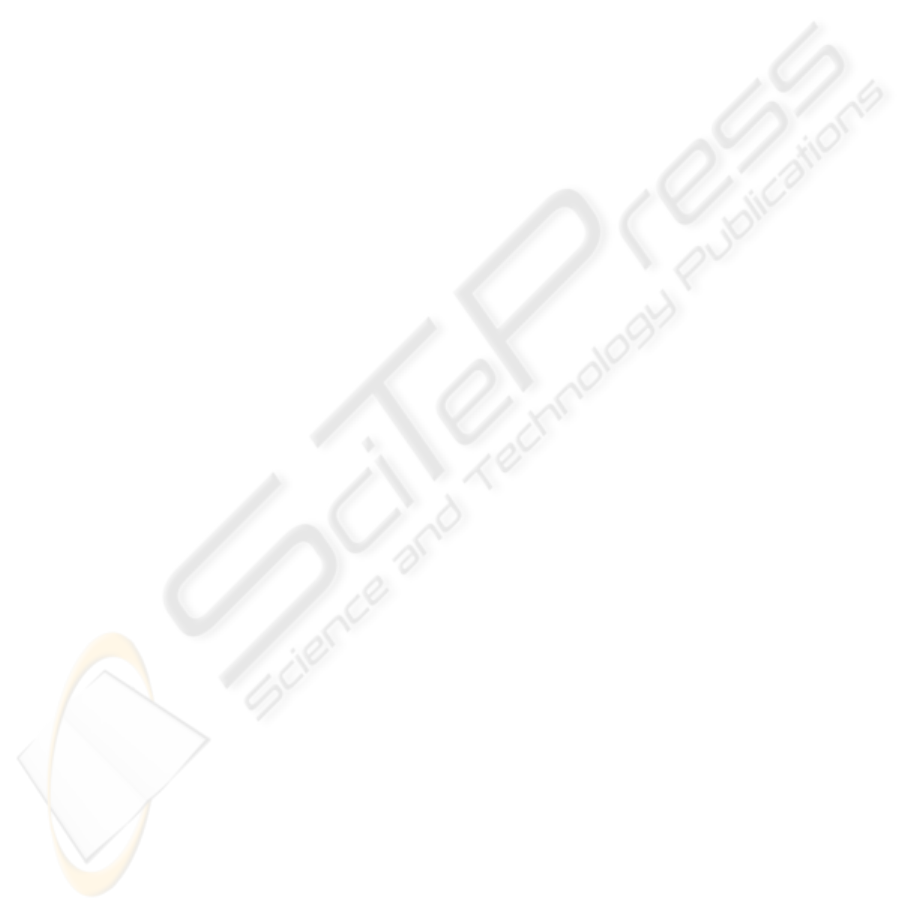
process performance measurement and analysis activ-
ities. This wealth of information can be used to pro-
vide process visibility in near real-time. The Event
Server consumes events as they are produced by the
business systems. These events can be processed and
further analyzed to derive events used to drive alerting
and notification software. Processing of raw business
events is known as Complex Event Processing (CEP).
Such event-driven processing systems provide a flex-
ible infrastructure for building real-time BAM soft-
ware (Knifsend and Debb, 2005). Process Mining,
(Agrawal et al., 1998) and (van der Aalst and Weijters,
2004), and statistical control techniques may also be
applied to the iWISE Event Server repository to yield
root cause analysis for out of control processes. In ad-
dition, processes can be simulated using iWISE sim-
ulation software which receives as input the event-
based process model captured using the iWISE PCT.
Using process analysis and simulation data processes
can be optimized with minimal latency in a constantly
changing business environment.
In recent years, consortia of businesses and re-
search institutions have developed process modelling
and definition languages to support interchangeable
business processes. (Mendling et al., 2004) analyze
fifteen of the currently available XML-based business
process modelling languages for completeness using
a set of meta-model concepts extracted from the can-
didate specifications. These concepts include the abil-
ity of the specification to include statistical data as
part of the business process meta-model. The inclu-
sion of statistical data for activities provides a busi-
ness process monitoring framework with information
to create relevant charts and alerts for its business
users. The study shows that the Workflow Manage-
ment Coalition’s (WfMC) XML Process Definition
Language is the only standardized interchange format
that includes process statistics. However, data cap-
tured is general and caters mainly for simulation ac-
tivities using statistical data such as costs and dura-
tions of tasks.
8 CONCLUSION
Fragmented collaborative and enterprise process visi-
bility requires a framework that integrates processes,
events and business information. This paper de-
scribed a common event-based model for integrating
disparate system processes and introduced the iWISE
BAM software architecture for process performance
monitoring. This approach brings together two im-
portant elements of enterprise modelling to provide
a more cohesive view of processes, the events gen-
erated by processes, and the business data manipu-
lated by the process. The iWISE framework allows
users to configure and manage event-based process
models using the iWISE Process Capture Tool and de-
ploy these models to the iWISE Event Server. iWISE
Legacy Listeners listen for system events and for-
ward these to the Event Server. Continuous data in-
tegration is achieved by packaging business data with
raw system events and sending it to the Event Server.
The Event Server processes a continuous stream of
event information and the iWISE Process Dashboard
presents users with up-to-date process information.
This generic approach is applicable to processes from
various business domains. A health-care process and
manufacturing process were presented in this paper
which the iWISE framework can support to enhance
business operational effectiveness through punctual
process visibility.
REFERENCES
Adams, C. W., Gupta, P., and Wilson, C. E. (2003). Six
Sigma Deployment. Butterworth Heinmann of Else-
vier Science.
Agrawal, R., Gunopulos, D., and Leymann, F. (1998). Min-
ing Process Models from Workflow Logs. In Proceed-
ings of the 6th International Conference on Extend-
ing Database Technology, pages 469–483. Springer-
Verlag.
Bobrik, R., Reichert, M., and Bauer, T. (2005). Require-
ments for the Visualization of System-Spanning Busi-
ness Processes. In The 16th International Work-
shop on Databases and Expert Systems Application,
Copenhagen, Denmark.
Casati, F. (2005). Industry Trends in Business Process Man-
agement: Getting Ready for Prime Time. In The 16th
International Workshop on Databases and Expert Sys-
tems Application, Copenhagen, Denmark.
Casati, F. and Discenza, A. (2000). Modeling and Managing
Interactions Amoung Business Processes. Technical
Report HPL-2000-159, Hewlett Packard, HP Labora-
tories Palo Alto, CA.
Caulcutt, R. (2001). Why is Six Sigma so successful? Jour-
nal of Applied Statistics, 28(3-4):301–306.
Costello, C., Molloy, O., Lyons, G., and Duggan, J. (2005).
Using Event-based Process Modelling to Support Six
Sigma Quality. In The 16th International Workshop on
Databases and Expert Systems Application, Copen-
hagen, Denmark.
Eder, J., Olivotto, G. E., and Gruber, W. (2002). A Data
Warehouse f or Workflow Logs. In EDCIS ’02: Pro-
ceedings of the First International Conference on En-
gineering and Deployment of Cooperative Informa-
tion Systems, pages 1–15. Springer-Verlag.
Eriksson, H.-E. and Penker, M. (2000). Business Modeling
with UML, Business Patterns at Work. OMG Press.
Kapoor, S., Bhattacharya, K., Buckley, S., Chowdhary,
P., Ettl, M., Katircioglu, K., E.Mauch, and Phillips,
ICEIS 2006 - INFORMATION SYSTEMS ANALYSIS AND SPECIFICATION
232