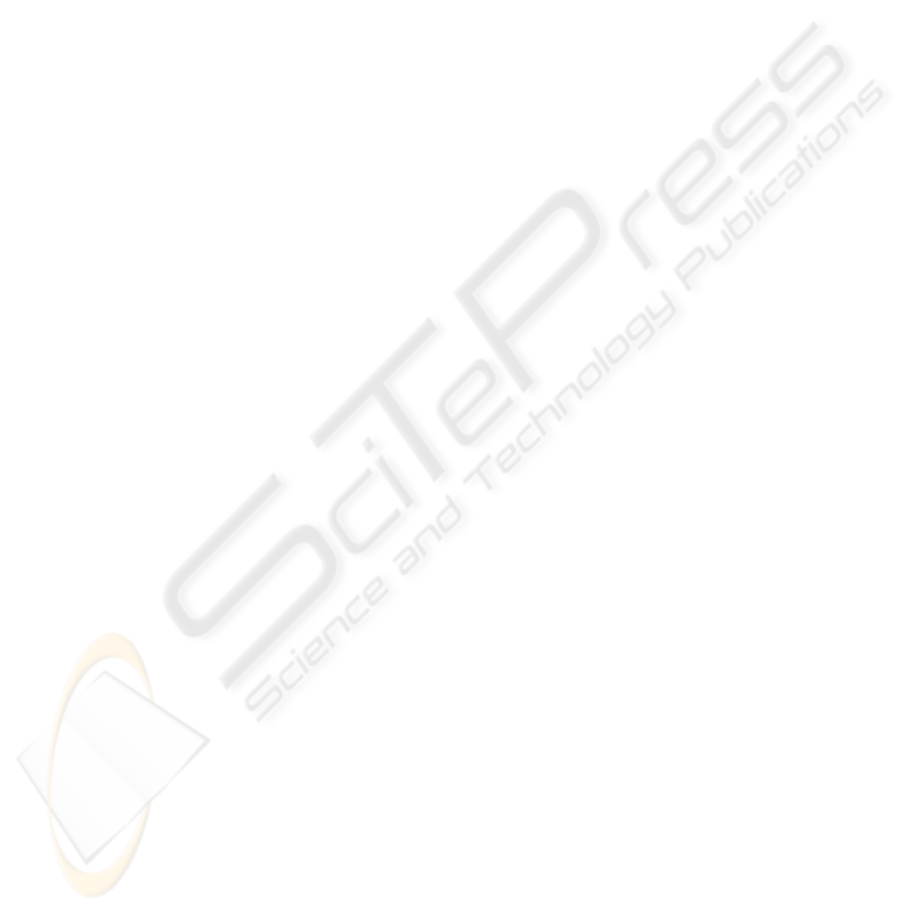
equipment. The request is then converted into a
series of commands appropriate for the specific
equipment being run by the Experiment Server.
When the experiment requested is completed the
Experiment Server computer sends results in the
form of data images and video clips back to the user
on the client computer via the ReLOAD web server,
providing virtually the same level of information as
would be obtained by performing the experiment
locally.
2.1 The Web Server
The web sever is set-up to receive and process
requests from the client, and since the web server
can be a single computer, custom software can be
readily created and installed to monitor internet
requests. The client computer may be one of
hundreds of different PC's and the manner in which
data is transmitted and received from the client
computer has significant impact on the overall
functionality and versatility of the final system.
Several alternative methods have been proposed
previously. An Active-X control panel could be
installed on the client computer to send and receive
information (Hites, 2002) through an Active-X
enabled browser. Alternatively a Java applet could
be created to run on a standard Internet browser to
control the experiment (Rohrig & Jochheim, 1999,
Sanchez et al., 2000). The ReLOAD system
simplifies all aspects of the remote experiment to
create a reliable, maintainable system. A standard
web form is used at the client end to request
experiments and retrieve and view the associated
results. At the server end, LabVIEW software
performs the experiments while monitoring,
receiving and sending data across the internet to the
client computer. The client computer only requires
standard java support to view the video feedback.
2.2 Controlling Equipment
The Experiment Server computers perform the
experiments and communicates across a LAN and in
turn pass the data on via the internet to the client PC.
Using data acquisition hardware, LabVIEW
software is used to control the experimental
equipment. The use of a single programming
environment and language simplifies the
development process.
The front panel of the Experiment Server
computer displays all parameters used by the
experiment, together with a preview window for the
video camera and the results graph. Hence the
experiment server computer functions as a
demonstration display, allowing staff, students and
visitors within the School of Mechanical
Engineering in Leeds to observe the experiments
being requested remotely. A tabbed panel on the
computer displays either a log of the requests
submitted to the system or the setup panel. A
shutdown button is incorporated into the design such
that it ensures that any requests being processed are
first dealt with before the ‘shutdown’ state.
2.3 System Communication
LabVIEW allows two alternative methods to
communicate the required information between
computers to perform remote experiments LabVIEW
HTTP Server with Common Gateway Interface
(CGI) Scripts or embedded ActiveX control panels.
The LabVIEW Web Server and embedded panel
method has several shortcomings. Firstly, it would
be necessary to purchase as many licenses as the
number of users that may be expected on the
experiment. Secondly, the provision of video; since
continuous experimental interaction is possible it
would be consistent to use streaming video footage,
giving a ‘live’ indication to the state of the
experiment. However, the quality of the video
footage is dependant on the connection speed.
Finally, this method relies on proprietary plug-ins in
order to embed the VI’s panel in a web-page.
The HTTP Server with CGI scripts method does
not encounter these problems, and justifies its use
for this application. The HTTP server does not
require a license dependant upon the number of
users expected and only a widely supported, multi-
platform java plugin is required, in this case to
display the video. It is important to note that only
experiments not requiring continuous interaction are
possible using this method.
The LabVIEW Internet Toolkit, an add on to the
standard LabVIEW package, provides a HTTP
server and a set of related Virtual Instruments (VI’s).
VI’s is the term used to refer to units of code that
perform a particular function. Of particular
relevance to this application are the CGI script VI’s.
CGI scripts are typically used in association with a
form on a web-page. Forms are defined using
standard HTML elements and allow a user to enter
information into a number of fields and post it to a
server. The server receives the post and invokes the
relevant CGI script. The script then processes the
information and sends back a response, typically a
web-page, through the server to the user. Note, once
the user has posted a form the web-browser will
AN APPLICATION OF REMOTLEY CONTROLLED EXPERIMENTS TO PERFORM FEEDFORWARD AND
FEEDBACK DAMPING CONTROL OF AN ELECTRO MECHANICAL SERVOMECHANISM
421