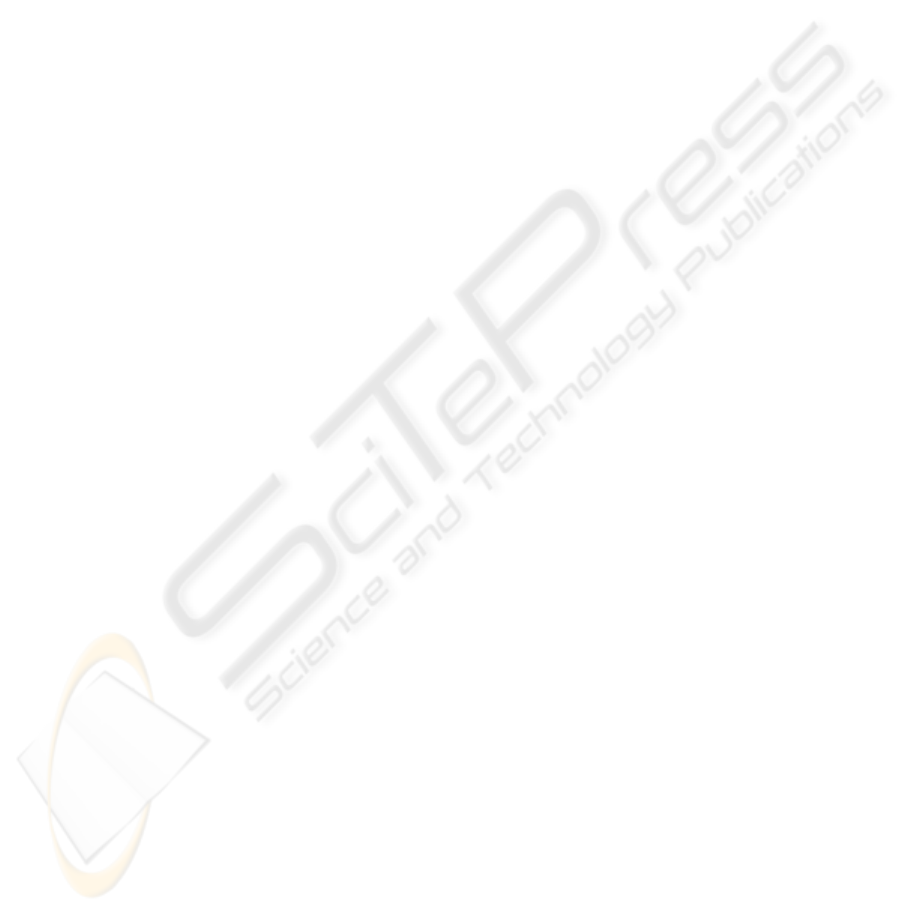
industry. The researchers hope to get an answer to
this problem through building the prototype.
It is the researchers’ opinion that the system
offers operational cost savings as well as new
business models. Operational cost savings are
achieved by optimizing refill amounts, by reducing
the frequency of visits on factory sites and by
improving the reaction to understock situations. In
addition deepened co-operative relationship between
customer and supplier results in synergy benefits.
Supplier expands supply to customer and service
improves for the customer. With the most efficient
stocking strategy, a supplier is able to deliver service
to customers which are far away from the delivery
centre (can’t be served using current operational
model). Furthermore, when competing for new
customers, the supplier has a competitive edge. The
clear advantage to the customer is the availability of
more detailed reports. For example, the analysis of
an understock situation is easier than before because
the supplier will be able to give detailed shelf
inventory balances and historical data to the
customer. From the supplier’s point of view, one can
be assured of maintaining the current customer base
and raising interest of new customers by offering a
better reporting system than the competition.
Will this implementation model be too
expensive compared to its benefits? It’s the
researcher’s opinion that this will only be clarified
through the prototype as well as through inspecting
constructing and maintaining tasks of the system in
practice. The businesses involved in the study also
felt that it would be important to find out customer
groups that are best suited to the proposed system.
Even though the proposed solution might be
financially non-viable in its entirety at this stage, it's
good to be aware of how the technology and costs
should develop in future in order to achieve the
necessary economic benefits which would make the
proposed solution viable.
7 FURTHER RESEARCH
The topic areas for further research will be price-
quality ratio analyses, the possibilities of
optimization of visit frequencies through simulations
and future cost predictions based on historical data
(basically mathematical analysis). Cost research will
concentrate on the total costs including servicing,
maintenance, installation, calibration, system
integrations and information engineering costs.
The researchers are also considering doing a
theoretical study about information exchange and
the problems associated with it. The Collaborative
Planning, Forecasting and Replenishment CPFR
framework will be studied as a development
direction for VMI operations and also the
exploitation and prediction of measuring data, to
assure that the ”service quality” of automated
ordering is not forgotten.
Because C-class products have an
indeterminable balance in the engineering industry,
their management models have been some what ad-
hoc in nature. Proposed solution would change the
nature of C-class products to that of B-class
products, so it would be natural to investigate B-
class management models in this context. It would
be particularly interesting to study how well current
Enterprise Resource Planning (ERP) systems could
be integrated into this type of “approximate”
inventory balance produced by this kind of
monitoring system. In other words, can current ERP
systems and their B-class management models be
directly adopted (for these C-class products) as is, or
does a completely new management theory have to
be developed for them?
REFERENCES
Disney, S.M., Towill, D.R., 2002. A Procedure for the
optimization of the dynamic response of a Vendor
Managed Inventory system. Computer & Industrial
Engineering, volume 43, issue 1-2, pages 27 – 58.
Federation of Finnish Enterprises. Retrieved 21.10.2006,
from http://www.yrittajat.fi/sy/home.nsf/www/english
Katz, M., Klaris A., Scorpio C., 2000. CPFR: Moving
Beyond VMI. Bobbin, Volume 41, Number 9, pages
90-94.
Pohlen, T.L., Goldsby, T.J., 2003. VMI and SMI
programs: How economic value added can help sell
the change. International Journal of Physical
Distribution & Logistics Management, volume 33,
number 7, pages 565 – 581.
SERVIISI-Project (In Finnish). Retrieved 17.10.2006,
from http://partnet.vtt.fi/serviisi/
Statistics Finland, Palvelualojen toimialakatsaus IV/2005
(in Finnish). Retrieved 20.10.2006, from
http://www.stat.fi/til/artikkelit/2006/art_2006-03-
28_004.html?s=0
Statistics Finland, Teollisuuden toimialakatsaus I/2006 (in
Finnish). Retrieved 20.10.2006, from
http://www.stat.fi/til/artikkelit/2006/art_2006-06-
28_001.html?s=0
TEMO-Project (In Finnish). Retrieved 10.10.2006, from
http://partnet.vtt.fi/temo/
Elvander, M.S., 2005. A theoretical mapping of the VMI
concept – A literature review. Report ISRN
LUTMDU/TMTD-4016--SE, Lund University. 40
pages.
WEBIST 2007 - International Conference on Web Information Systems and Technologies
162