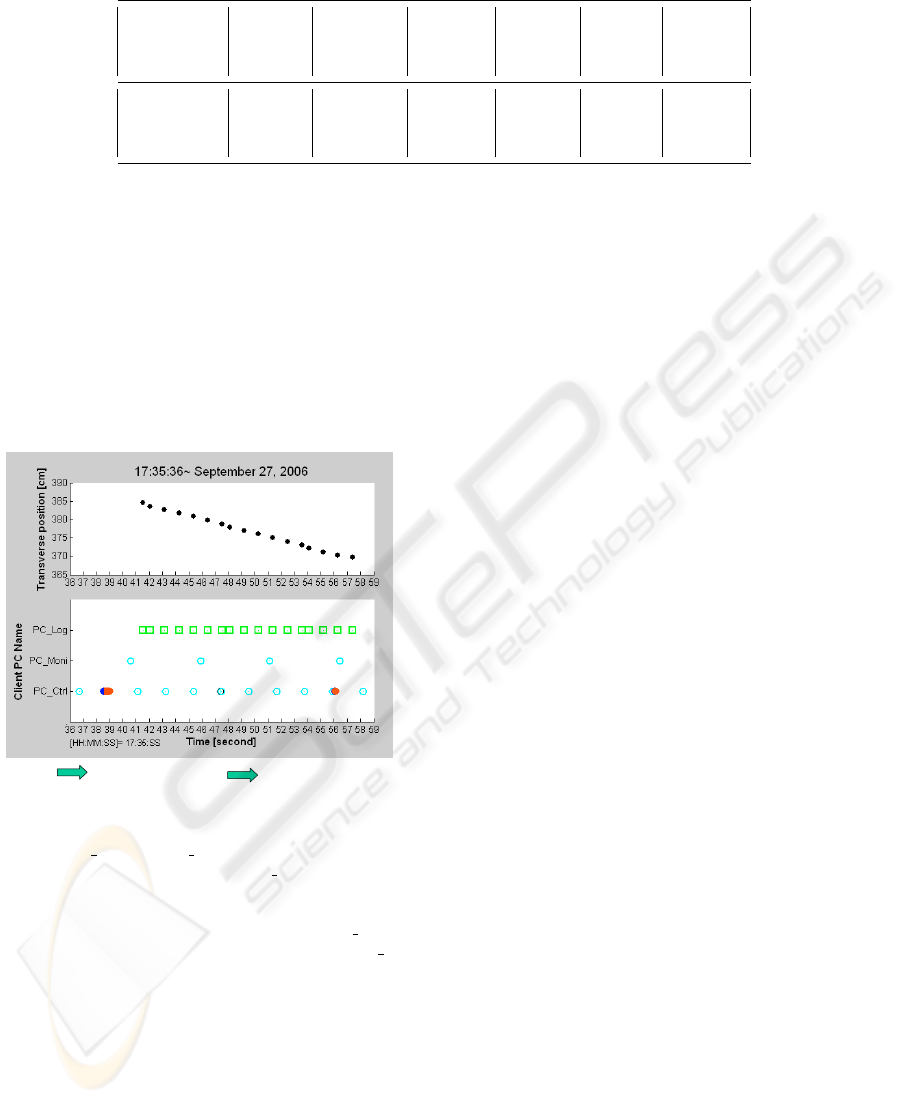
Table 1: Reply times for commands and needed times for position information.
Drive axis Priority $DRIVE First Priority $STOP Last
position position
ms ms sec. ms ms sec.
Transverse 6 32 2.5 6 31 1.6
Elevation 6 28 1.5 7 28 1.0
Rotation 7 30 3.2 7 27 1.2
architecture. Therefore retry of the selection is not
required. Consequently remote control by a WEB
Browser has been working well.
Residual issues are the following:
• A notebook PC lacks solidity.
• It takes longer time in a FORCED STOP oper-
ation on a wireless PC than in an operation by
an EMERGENCY STOP button on an operation
desk.
(a)
(b)
Waiting
$DRIVE
command
$STOP
command
Figure 4: Ordered accesses by three PCs to a main server
PC via LAN. The lower figure (b) shows access timing from
multi PCs. PC
Mon and PC Ctrl use WEB Brower with an
interval time of two or five seconds. PC
Log uses an exclu-
sive application program for logging positioning data with
an interval time of about one second. The upper figure (a)
shows positioning information acquisitioned by PC
Log. In
the lowest row, a transition of motion modes about PC
Ctrl
is shown.
5 CONCLUSION
The development of a remote operation system via a
wireless PC didn’t require editing of a complex se-
quencer program in the electric flatcar, so that this
system starts working well as soon as possible. Using
a function of PRESET DRIVE and a simple commu-
nication protocol that are implemented in the electric
flatcar, the server program for WEB pages that are
available for control and monitoring of a machine has
developed in a sever PC. Usage of a WEB browser
makes possible a flexible constitution of the remote
terminal system. Then it has a merit of a smaller task
to a terminal PC.
This system has been developed on the basis of
two contents such as a WEB direct-access model, and
a controller / multi-monitor system model. It was
clear by the above-described mission that the commu-
nication speed of the electric flatcar is applicable to
the model of WEB direct-access control and monitor-
ing, in the case of attainability of the electric flatcar.
An attachment of a probe is also available for in-
stallation of underwater cameras. The optical calibra-
tion of an underwater observation bench is scheduled
using an electric flatcar. It is hopeful that the wireless
operation on the spot instead of a push button opera-
tion on an operation desk is effective.
REFERENCES
Ishii, K., Abe, K., and Takao, Y. (2006). Positioning control
of the electric flatcar using web browser via wireless
lan. In Abstracts of 2006FY Autumn Annual Meeting.
AMSTEC.
Ishii, K. and Sawada, K. (2005). Network-integrated control
program for a transducer-rotating mechanism to mea-
sure target strength (ts) pattern of squid. In Journal
of Advanced Marine Science and Technology Society.
AMSTEC.
Ishii, K., Sawada, K., and Miyanohana, Y. (1999). Design
of transducer-positioning system scanning around an
aquatic target in a tank. In Collected Papers of FO-
RUM ACUSTICUM BERLIN 99. ASA and DEGA.
Ishii, K., Sawada, K., Takao, Y., Miyanohana, Y., and Oku-
mura, T. (1995). Control system of electric flat-car
equipped above an acoustic tank. In Proceeding of
the Annual Meeting. the Marine Acoustics Society of
Japan.
Ishii, K. and Takao, Y. (2000). Evaluation of transducer-
positioning system scanning around an aquatic target
in a tank. In Abstracts of 2000FY Spring Annual Meet-
ing. Advanced Marine Science and Technology Soci-
ety.
ICINCO 2007 - International Conference on Informatics in Control, Automation and Robotics
326