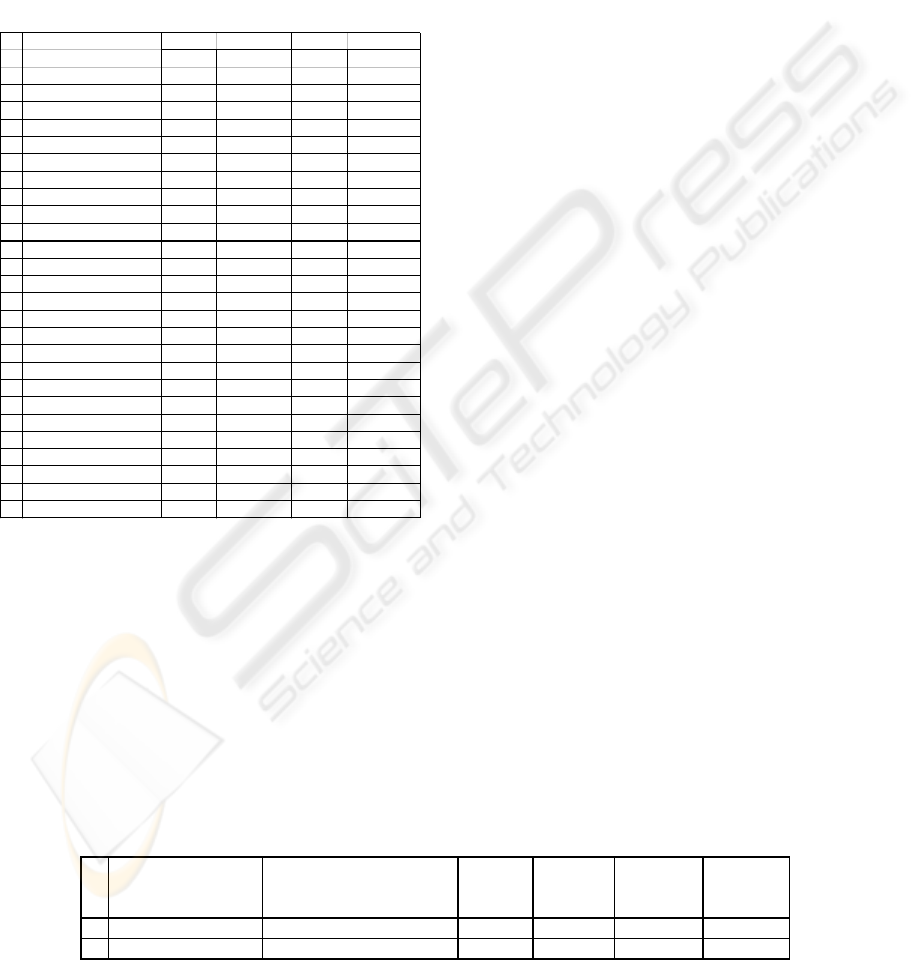
strategies are given in Table 2 by means of the
control vector variation.
The time gain of the optimal design strategy with
respect to the traditional strategy is equal to 285 for
the gradient method and 200 for the DFP method.
These data show good perspectives for proposed
approach. However the potential time gain is
realized only in case when we found the algorithm
for the optimal control vector construction.
Table 1: Data of some strategies.
5 CONCLUSIONS
The traditional approach for the analogue circuit
design is not time-optimal. The problem of the time-
optimum design algorithm can be solved adequately
on the basis of the control theory application. The
construction of the time-optimal design algorithm is
formulated as the problem of a functional
minimization of the control theory. This approach
can reduce considerably the total computer time for
the system design. Analysis of the different
electronic systems gives the possibility to conclude
that the potential computer time gain of the time-
optimal strategy increases when the size and
complexity of the system increase. The proposed
approach gives the possibility to find the time-
optimal algorithm as a solution of the typical
problem of the optimal control theory. The optimal
structure of the control vector can be finding by the
approximate methods of control theory.
ACKNOWLEDGEMENTS
This work was supported by the Mexican National
Council of Science and Technology – CONACYT,
under project SEP-2004-C01-46510.
REFERENCES
Osterby, O., Zlatev, Z., 1983. Direct Methods for Sparse
Matrices, Springer-Verlag, N.Y.
George, A., 1984. On Block Elimination for Sparse Linear
Systems, SIAM J. Numer. Anal. vol. 11, no.3, pp. 585-
603.
Wu, F.F., 1976. Solution of Large-Scale Networks by
Tearing”, IEEE Trans. Circuits Syst., vol. CAS-23, no.
12, pp. 706-713.
Sangiovanni-Vincentelli, A., Chen, L.K., Chua, L.O.,
1977. An Efficient Cluster Algorithm for Tearing
Large-Scale Networks, IEEE Trans. Circuits Syst.,
vol. CAS-24, no. 12, pp. 709-717.
Kashirsky, I.S., Trokhimenko, Y.K., 1979. The
Generalized Optimization of Electronic Circuits,
Tekhnika, Kiev.
Rizzoli, V., Costanzo, A., Cecchetti, C., 1990. Numerical
Optimization of Broadband Nonlinear Microwave
Circuits, IEEE MTT-S Int. Symp., vol. 1, pp. 335-338.
Ochotta, E.S., Rutenbar, R.A., Carley, L.R., 1996.
Synthesis of High-Performance Analog Circuits in
ASTRX/OBLX, IEEE Trans. on CAD, vol.15, no. 3,
pp. 273-294.
Zemliak, A., 2005. Generalization of Analog System
Design Methodology, In Proc. 5th WSEAS Int. Conf.
on Instrumentation, Measurement, Control, Circuits
and Syst., Cancun, Mexico, pp.114.119.
Table 2: Data of the optimal design strategies.
N Control functions Gradient method DFP method
vector Iterations Total design Iterations Total design
U (u1,u2,u3,u4,u5,u6,u7) number time (sec) number time (sec)
1 ( 0 0 0 0 0 0 0 ) 6379 321.09 854 64.47
2 ( 0 0 1 0 1 0 1 ) 922 54.53 764 52.29
3 ( 0 0 1 0 1 1 0 ) 1667 80.71 650 46.13
4 ( 0 0 1 0 1 1 1 ) 767 35.35 426 22.68
5 ( 0 0 1 1 1 0 0 ) 3024 159.67 940 52.71
6 ( 0 0 1 1 1 0 1 ) 823 37.73 177 7.71
7 ( 0 0 1 1 1 1 0 ) 3068 86.87 450 14.56
8 ( 0 0 1 1 1 1 1 ) 553 15.75 170 6.93
9 ( 0 1 1 0 1 0 1 ) 465 10.01 101 2.66
10 ( 0 1 1 0 1 1 0 ) 1157 31.92 111 3.85
11 ( 0 1 1 0 1 1 1 ) 501 8.82 124 2.66
12 ( 0 1 1 1 1 0 0 ) 2643 72.66 314 9.24
13 ( 0 1 1 1 1 0 1 ) 507 9.24 170 4.62
14 ( 0 1 1 1 1 1 0 ) 3070 67.27 423 12.25
15 ( 1 0 1 0 1 0 1 ) 1345 28.07 397 16.94
16 ( 1 0 1 0 1 1 1 ) 615 10.01 191 4.62
17 ( 1 0 1 1 1 0 1 ) 699 10.71 197 4.97
18 ( 1 0 1 1 1 1 1 ) 366 4.97 103 1.96
19 ( 1 1 1 0 1 0 1 ) 789 10.43 201 4.97
20 ( 1 1 1 0 1 1 0 ) 3893 61.53 1158 18.06
21 ( 1 1 1 0 1 1 1 ) 749 7.71 148 2.11
22 ( 1 1 1 1 1 0 0 ) 4325 90.72 945 19.18
23 ( 1 1 1 1 1 0 1 ) 796 8.47 133 2.31
24 ( 1 1 1 1 1 1 0 ) 2149 29.26 1104 13.44
25 ( 1 1 1 1 1 1 1 ) 2031 5.67 180 0.77
N Method Optimal control Iterations Switching Total Computer
functions vector number points design time gain
U (u1,u2,u3,u4,u5,u6,u7) time (sec)
1 Gradient method (1111111); (1111101) 363 350 1.127 285
2 DFP method (1111111); (1110111) 69 66 0.322 200
ICINCO 2007 - International Conference on Informatics in Control, Automation and Robotics
346