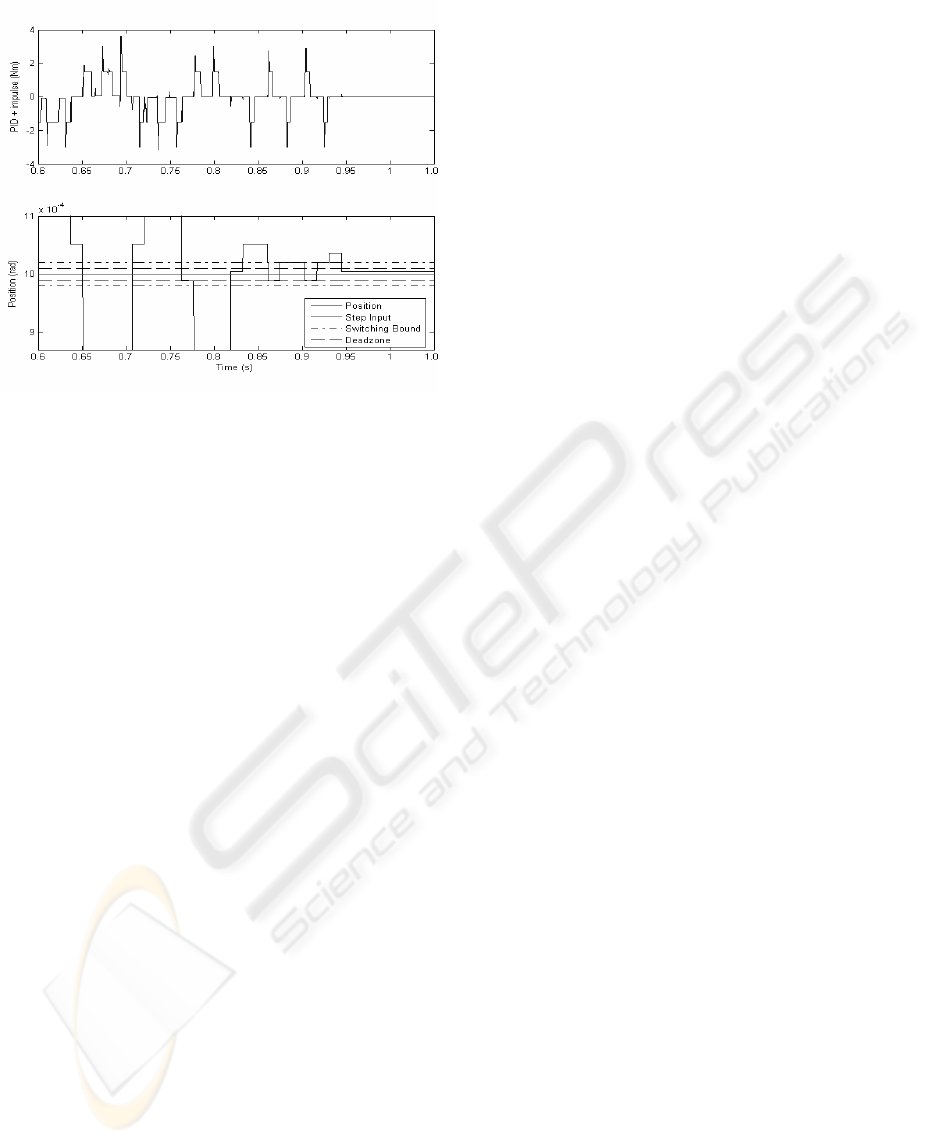
Figure 11: Using the ‘Limit Cycle Offset’ function to
reduce the final steady state error of the Hirata robot.
4.2 Discussion of Results
This set of results demonstrates the Limit Cycle
Offset function can be successfully applied to a
commercial robot manipulator having characteristics
of high non-linear friction. The results show that the
unmodified controller will cause the robot to limit
cycle near steady state position and that the peak to
peak displacement is equal to the displacement of
the smallest usable width pulse.
By using the Limit Cycle Offset function, the
limit cycle can be detected and the pulse width
adjusted so that at least one of the peaks of the limit
cycle is moved towards the reference set point.
Finally, the results show that the controller
recognises the limit cycle as being shifted into a
defined error dead-zone whereby the controller is
disabled. The steady state error is therefore
guaranteed to fall within a defined region so that the
steady state error is reduced. For the SCARA robot,
the improvement in accuracy demonstrated was
1.1e-4 radians in comparison to 4.5e-4 radians
achieved without the limit cycle offset.
5 CONCLUSION
Advances in digital control have allowed the power
electronics of servo amplifiers to be manipulated in
a way that will improve a servomechanism precision
without modification to the mechanical plant. This is
particularly useful for systems having highly non-
linear friction where conventional control schemes
alone under perform. A previously developed hybrid
PID + Impulse controller which does not require the
mechanism to come to a complete stop between
pulses has been modified to further improve
accuracy. This modification shifts the limit cycling
into a different position to provide substantial
additional improvement in the mechanism’s position
accuracy. This improvement has been demonstrated
both in simulations and in experimental results on a
SCARA robot arm. The mechanism does not have to
come to a complete stop between pulses, and no
mechanical modification has to be made to the robot.
REFERENCES
Armstrong-Hélouvry, B., 1991, “Control of Machines with
Friction” Kluwer Academic Publishers, 1991, Norwell
MA.
Armstrong-Hélouvry, B., Dupont, P., and Canudas de
Wit, C., 1994, “A survey of models, analysis tools and
compensation methods for the control of machines
with friction” Automatica, vol. 30(7), pp. 1083-1138.
Canudas de Wit, C., Olsson, H., Åström, K. J., 1995 ”A
new model for control of systems with friction” IEEE
Tansactions on Automatic Control, vol. 40 (3), pp.
419-425.
Dahl, P., 1968, “A solid friction model” Aerospace Corp.,
El Segundo, CA, Tech. Rep. TOR-0158(3107-18)-1.
Dahl, P, 1977, “Measurement of solid friction parameters
of ball bearings” Proc. of 6
th
annual Symp. on
Incremental Motion, Control Systems and Devices,
University of Illinois, ILO.
Hojjat, Y., and Higuchi, T., 1991 “Application of
electromagnetic impulsive force to precise
positioning” Int J. Japan Soc. Precision Engineering,
vol. 25 (1), pp. 39-44.
Johannes, V. I.., Green, M.A., and Brockley,C.A., 1973,
“The role of the rate of application of the tangential
force in determining the static friction coefficient”,
Wear, vol. 24, pp. 381-385.
Johnson, K.L., 1987, “Contact Mechanics” Cambridge
University Press, Cambridge.
Kato, S., Yamaguchi, K. and Matsubayashi, T., 1972,
“Some considerations of characteristics of static
friction of machine tool slideway” J. o Lubrication
Technology, vol. 94 (3), pp. 234-247.
Li, Z, and Cook, C.D., 1998, ”A PID controller for
Machines with Friction” Proc. Pacific Conference on
Manufacturing, Brisbane, Australia, 18-20
August,
1998, pp. 401-406.
Olsson, H., 1996, “Control Systems with Friction”
Department of Automatic Control, Lund University,
pp.46-48.
Popovic, M.R., Gorinevsky, D.M., Goldenberg, A.A.,
2000, “High precision positioning of a mechanism
with non linear friction using a fuzzy logic pulse
ICINCO 2007 - International Conference on Informatics in Control, Automation and Robotics
172