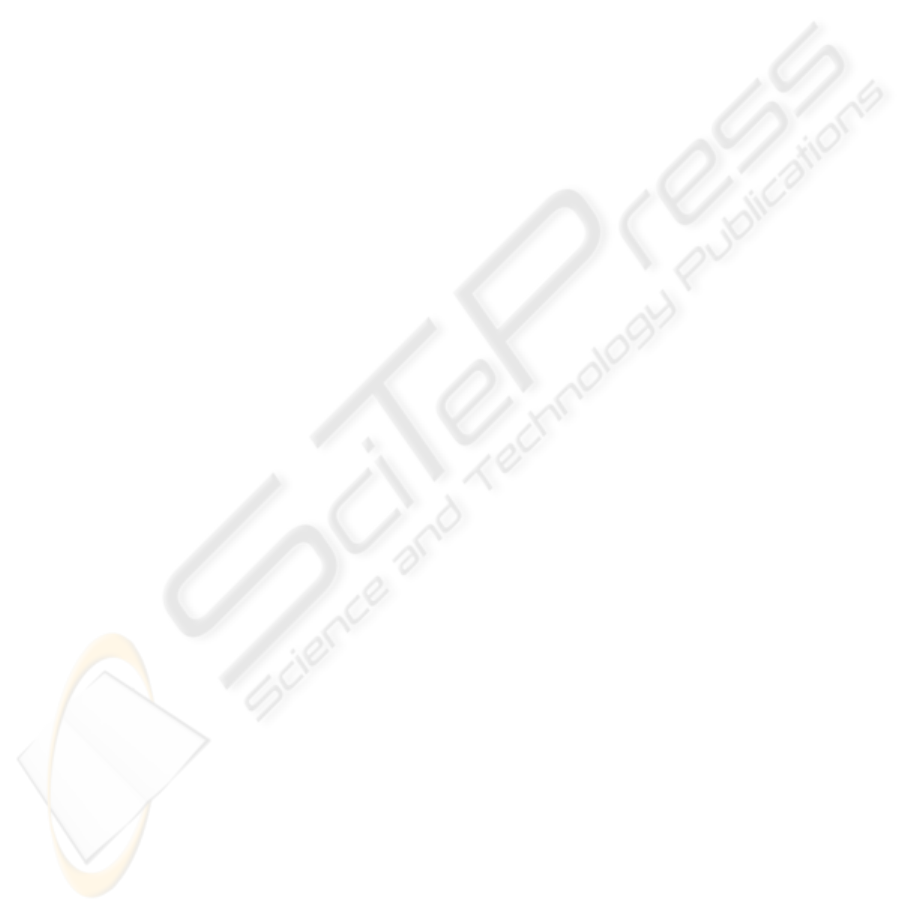
GLOBAL ASYMPTOTIC VELOCITY OBSERVATION OF
NONLINEAR SYSTEMS
Application to a Frictional Industrial Emulator
R. Guerra
‡
, C. Iurian
⋆
, L. Acho
‡⋆
‡
Centro de Investigaci
´
on y Desarollo de Technolog
´
ıa Digital (CITEDI-IPN), Mexico
⋆
Universitat Polit
`
ecnica de Catalunya, Matem
`
atica Aplicada III, EUETIB, Barcelona, Spain
F. Ikhouane
†
and J. Rodellar
§
†
Universitat Polit
`
ecnica de Catalunya, Matem
`
atica Aplicada III, EUETIB, Barcelona, Spain
§
Universitat Polit
`
ecnica de Catalunya, Matem
`
atica Aplicada III, Barcelona, Spain
Keywords:
Velocity observers, friction, mechanical systems.
Abstract:
Development of velocity observers for mechanical systems with friction deserves a special emphasis, because
as evidenced in numerical and experimental tests when a state-of-the-art observer is armed, friction can in-
duce high-frequency oscillations in the estimated signal. In this short paper, two new velocity-observation
algorithms are designed, based on this previously reported observer, that eliminate the high-frequency oscilla-
tions noted. Numerical and experimental performance comparisons are carried through making use of LuGre
model and a mechanical PID control system that incorporates the estimated velocity into the feedback loop.
1 INTRODUCTION
Velocity-dependent control laws such as PD, PID, and
most robust control laws, among many others, the-
oretically require direct access to velocity. In reality,
there are many applications in which this is not availa-
ble either due to considerable manufacturing savings
in cost, weight, and volume, or because the velocity
measurements are highly contaminated with noise. In
the latter case, for instance when measuring robot
joint velocities, it may not even be desirable to do
so (Arteaga and Kelly, 2004). Consequently, if the
full-state information is missing, it is necessary to
estimate the unmeasurable velocity through the use
of an observer and feed it back into the controller.
Such is the case with the frictional industrial emula-
tor ECP model 220 used in our experiments. It has
been documented when studying mechanical closed-
loop control systems, that friction causes tracking
errors, limit-cycles, and stick-slip motions, among
other difficulties and usually unwanted phenomena
(Armstrong-H
´
etlouvry et al., 1994). As evidenced
in (Canudas de Wit and Fixot, 1991), (Canudas de
Wit and Fixot, 1992), (Berghuis and Nijmeijer, 1993),
and (Arteaga and Kelly, 2004) velocity observer de-
sign is a topic that has been and continues to be ex-
tensively studied. State observation of nonlinear ine-
xact plants has been treated by utilizing discontinu-
ous observers (Choi et al., 1999), (Xiong and Saif,
2001), and (Xian et al., 2004). However, little re-
search focused on velocity observation of mechan-
ical systems with friction at low velocities which,
when incorporating existing observers, exhibit high-
frequency oscillations in the velocity-estimation sig-
nal. A state-of-the-art, globally asymptotic, discon-
tinuous velocity-estimation scheme for second-order
mechanical systems has been presented in (Xian et al.,
2004). Though very reliable, this observer is not spe-
cialized for mechanical systems in the presence of
friction. Thus, a high-frequency component of the ve-
locity observation is detected when numerical simu-
lations and experimental testing are performed. The
two newly proposed observers claimed here are an
attempt to alleviate this unwanted oscillatory effect
and try offer an increase in the observation reliability.
The remainder of this document proceeds as fo-
llows: Section 2 postulates two modified observers
based on the velocity estimator stated in (Xian et al.,
2004). The next section presents numerical simu-
lations evidencing the performance of the observers.
Section 4 begins with a description of the frictional
experimental testbed, the ECP industrial emulator
85
Guerra R., Iurian C., Acho L., Ikhouane F. and Rodellar J. (2007).
GLOBAL ASYMPTOTIC VELOCITY OBSERVATION OF NONLINEAR SYSTEMS - Application to a Frictional Industrial Emulator.
In Proceedings of the Fourth International Conference on Informatics in Control, Automation and Robotics, pages 85-91
DOI: 10.5220/0001621100850091
Copyright
c
SciTePress