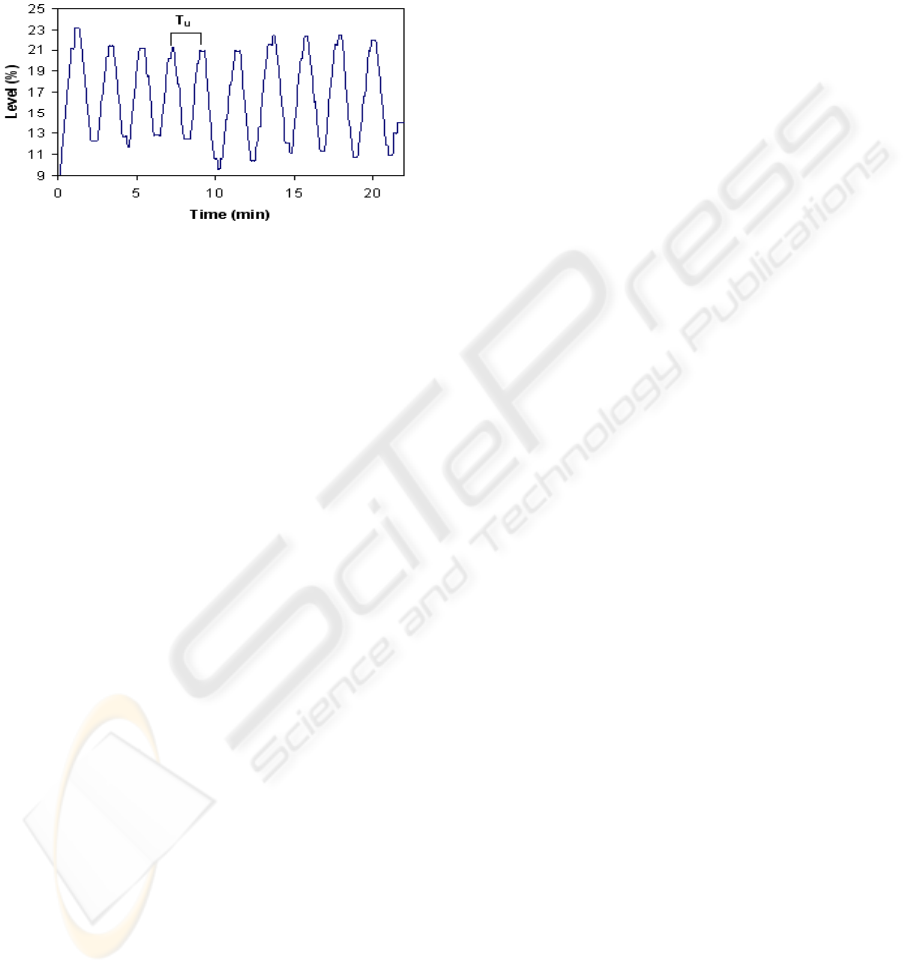
(a) Increase the proportional gain until the
system oscillates (Figure 3); that gain is the ultimate
gain K
u
.
(b) Read the time between peaks T
u
at this
setting.
(c) Approximate values for the controller
parameters are given in a table.
Figure 3: Ziegler-Nichols frequency response method.
The sample period may be related to the
derivative gain T
d
. In connection with the Ziegler-
Nichols rules, this implies that T
s
should
approximately be equal to 1 – 5 percent of the
ultimate period T
u
. Taking full advantage of this
method; we were able to adequately control the
reactor temperature and the liquid evacuation unit.
When the system reaches the steady state, the
controller allows us to maintain a constant liquid
level in the tank. Consequently, liquid flow can be
continuously evacuated at the system’s outlet.
4 HUMAN MACHINE
INTERFACE (HMI)
An operator’s graphical interface was developed
using the FIX MMI Intellution SCADA software
which combines high performance monitoring and
control with wide range of data acquisition on the
Windows NT/2000/9x operating systems. The FIX
application contains three sets of multithreaded
processes: the user process (HMI), the FIX engine
and the industrial automation device servers. These
processes interact through a client-server
relationship. The user process displays the user
interface and executes blocks of code that are
defined for control algorithms, supervisory control,
analysis and visual presentation. The event-driven
engine maintains a real time database, communicates
with device servers and performs a multitude of
tasks including engineering unit scaling, alarm
processing and historical data collection and
trending. Device servers are the applications that
communicate with Input/Output devices. The FIX
application establishes a communication with the
ISM112 intelligent sensor modules through the
deployment of a Modbus RTU server fully
compliant with the latest Modbus RTU protocol
definitions. Therefore, the ISM112 data registers can
be accessed and modified to the desired values
allowing thus the operator to have full control of the
process variables.
5 CONCLUSION
The aim of this work is to setup an oxidation process
that meets the conditions needed for the aqueous
destruction by oxygen or air of organic pollutants.
The aforementioned techniques and equipments
which in priority are based on regulation and
automation procedures, allowed us to design an
automated fixed bed reactor that fulfills the required
temperatures and pressures conditions (up to 300°C
and 25 bar) usually used for CWAO processes. The
developed monitoring interface allows the operator
to easily manage and control the process parameters.
Chemical runs allowing us to validate the system
efficacy during the oxidation of various types of
aqueous wastes, are in process of completion.
REFERENCES
Debellefontaine, H., Foussard, J.N.,Wet air oxidation for
the treatment of industrial wastes, Waste Manage., 20
(2000) 15.
Imamura, S., Fukuda, I., Ishida, S., Wet oxidation
catalyzed by ruthenium supported on cerium(IV)
oxide, Ind. Eng. Chem. Res., 27 (1988) 718.
Masende, Z.P.G., Kuster, B.F.M., Ptasinski, K.J., Janssen,
F.J.J.G., Katima, J.H.Y., and Scouten, J.C., Platinium
catalysed wet oxidation of phenol in a stirred slurry
reactor: A practical operation window, Appl. Catal. B,
41 (2003) 247.
Mishra, V.S., Mahajani,V.V., Joshi, B., Wet Air
Oxidation, Ind. Eng. Chem. Res., 34 (1995) 2.
Oliviero, L., Barbier Jr, J., Duprez, D., Guerrero-Ruiz, A.,
Bachiller-Baeza, B., Rodriguez-Ramoz, I., Catalytic
wet air oxidation of phenol and acrylic acid over Ru/C
and Ru–CeO
2
/C catalysts, Appl. Catal. B, 25 (2000)
267.
Pintar, A., Levec, J., Catalytic oxidation of organics in
aqueous solutions : I. Kinetics of phenol oxidation, J.
Catal., 135 (1992) 345.
Tan, W., Liu, J., Chen, T., and Marquez, H.J.,
Comparaison of some well-known PID formulas,
Comput. Chem. Eng., 30 (2006) 1416.
ICINCO 2007 - International Conference on Informatics in Control, Automation and Robotics
368