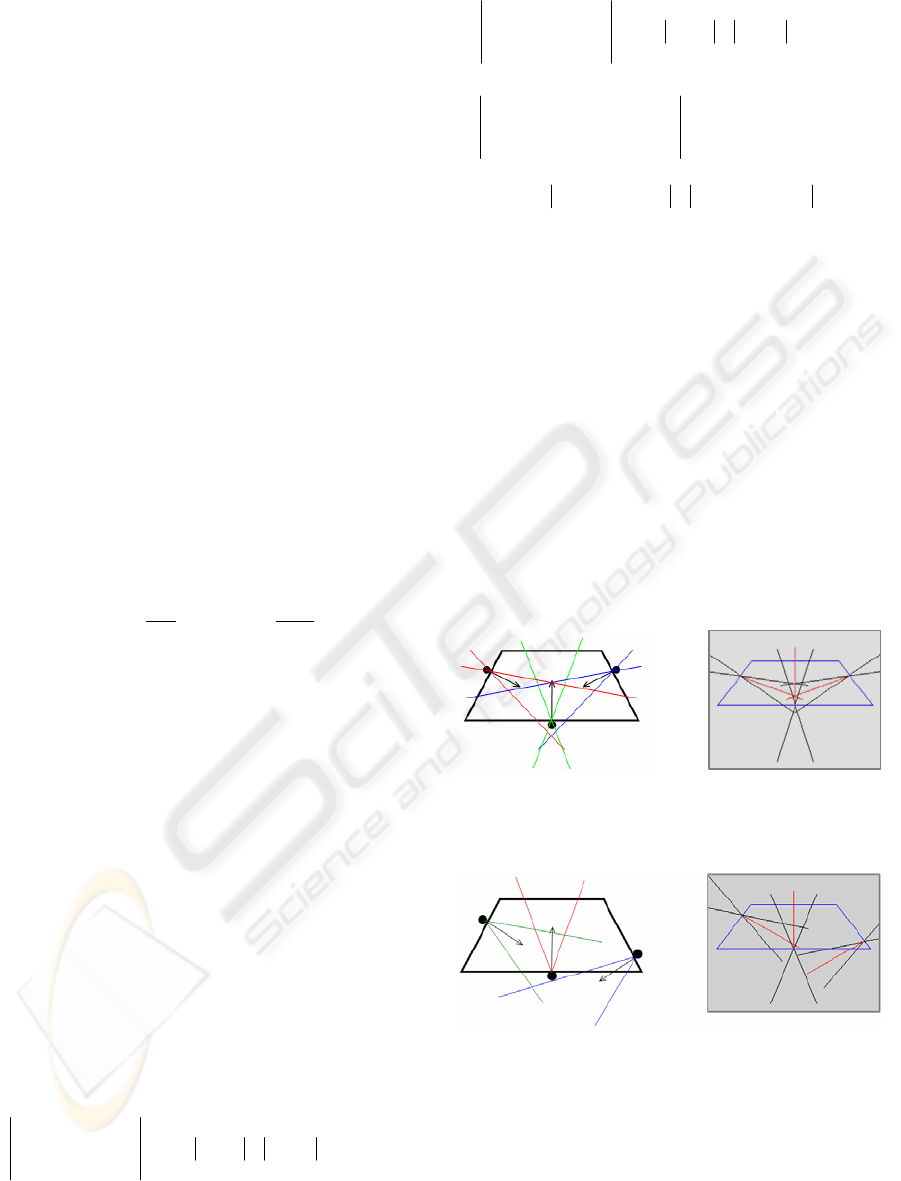
Using force-closure condition in definition 2, we
can derive this definition
Using force-closure condition in definition 2, we
can derive this definition
Definition 4: A grasp is force closed, if and only if
it is in equilibrium for any arbitrary wrench (Bicchi
A., Kumar V. 2000, Nguyen, V.D. 1988). Thus,
force closure implies, fingers contact wrenches can
balance any external task wrenches.
Definition 4: A grasp is force closed, if and only if
it is in equilibrium for any arbitrary wrench (Bicchi
A., Kumar V. 2000, Nguyen, V.D. 1988). Thus,
force closure implies, fingers contact wrenches can
balance any external task wrenches.
According to proposition 1 and definition 4, we
propose a new force-closure necessary and sufficient
condition.
According to proposition 1 and definition 4, we
propose a new force-closure necessary and sufficient
condition.
Proposition 2: A multifingred grasp of 2D objects
is said to achieve force-closure if and only if the
central axis of the fingers contact wrenches can
sweep the grasp plan at any direction.
Proposition 2: A multifingred grasp of 2D objects
is said to achieve force-closure if and only if the
central axis of the fingers contact wrenches can
sweep the grasp plan at any direction.
4.3 Force-Closure Test Algorithm 4.3 Force-Closure Test Algorithm
According to the proposition 2, we present a new
algorithm for computing 2D multi-fingers grasps of
arbitrary object.
According to the proposition 2, we present a new
algorithm for computing 2D multi-fingers grasps of
arbitrary object.
Based on the central axis equation defined in
relation (10), this central line can sweep the plan in
all directions if
Based on the central axis equation defined in
relation (10), this central line can sweep the plan in
all directions if
()
c
,k,k Δ
2
21
∃ℜ∈∀
Satisfy Satisfy
21
kxky
(a) (b)
(a)
(b)
()
c
,k,k Δ
2
21
∃ℜ∈∀
21
kxky
⋅=
Where
⎟
⎟
⎠
⎞
⎜
⎜
⎝
⎛
=
⎟
⎟
⎠
⎞
⎜
⎜
⎝
⎛
=
cx
o/z
cx
cy
F
τ
k;
F
F
k
11
In other word, for any axis on the plan or
along the vertical , this axis must be one of the
grasp wrench central axes.
(
YX,
)
Z
This condition implies that the quantities and
must take all real number, therefore
1
k
2
k
[]
[]
[]
⎪
⎩
⎪
⎨
⎧
∀+∞∞−∈
+∞∞−∈
+∞∞−∈
O,τ
,F
,F
o/c
cy
cx
(21)
The third sub-condition is function of the reduced
point of the torque, to cover the entire grasp plan; we
test this condition at all the vertices of the
intersection of the m double-side friction cones
(named ). In general case of m contact points, the
number of intersection points is given by
k
B
(
∑
−
=
−⋅=
1
1
4
m
k
B
kmN
k
)
(22)
Hence, a multifingred 2D grasp is said to achieve
force-closure if each of these inequalities are true.
()
()
∑∑
==
⋅+⋅<+⋅
m
i
ii
m
i
ii
1
21
1
21
nXnXnnX (23-1)
()
()
∑∑
==
⋅+⋅<+⋅
m
i
ii
m
i
ii
1
21
1
21
nYnYnnY (23-2)
()()
()()
()
∑
∑
=
=
∧⋅+∧⋅
<+∧⋅
m
i
iikiik
m
i
iiik
1
21
1
21
nCBZnCBZ
nnCBZ
(23-3)
From mechanical viewpoint, inequality (23-1)
implies that fingers can generate forces
along and
X X
, (23-2) means that fingers can exert
force on the object along and . If the last
inequality (23-3) is true
Y Y−
k
B
N...kfor 1=
then the
finger can exert torque on object about the vertical
axis in both directions.
Z
5 EXAMPLES
We present bellow some grasp examples using three,
four and five fingers. In both cases (force-closure
and no force-closure), we show the distribution of
grasp wrench central axes.
a) Three-finger grasps
Figure 6: a) a three-finger force-closure 2D grasp, b)
central axes of grasp wrenches ( ).
°=15α
Figure 7: a) a three-finger force-closure 2D grasp, b)
central axes of grasp wrenches ( ).
°= 20α
ON COMPUTING MULTI-FINGER FORCE-CLOSURE GRASPS OF 2D OBJECTS
257