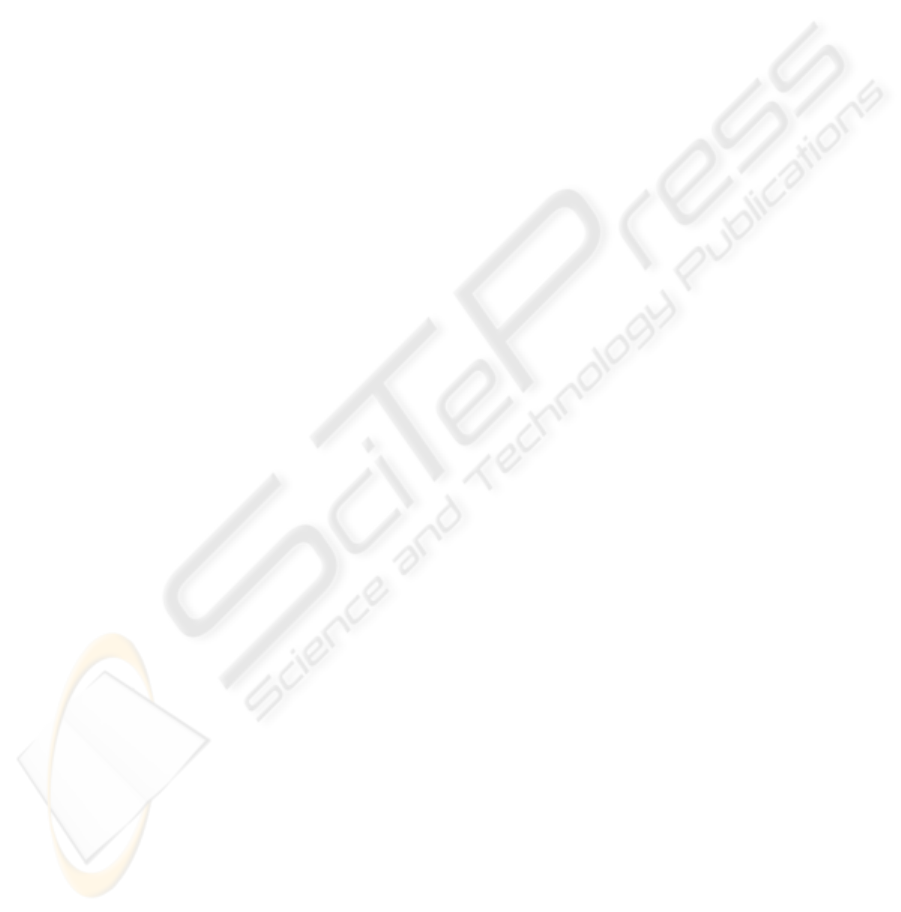
DEVELOPMENT OF THE CONNECTED CRAWLER ROBOT
FOR ROUGH TERRAIN
Realization of the Autonomous Motions
Sho Yokota, Yasuhiro Ohyama, Hiroshi Hashimoto and Jin-Hua She
School of Bionics, Tokyo University of Technology, 1404-1 Katakuramachi Hachioji, Tokyo, Japan
Kuniaki Kawabata
RIKEN, 2-1 Hirosawa Wako, Saitama, Japan
Pierre Blazevic
Institut des Sciences et Techniques des Yvelines, 7 rue Jean Hoet, Mantes, France
Hisato Kobayashi
Faculty of Eng., Hosei University, 2-17-1 Fujimi Chiyodaku, Tokyo, Japan
Keywords:
Crawler, Rough terrain, Step climbing, Autonomous motion, Connected crawler.
Abstract:
The purpose of this paper is to develop a rough terrain mobile system. Our mobile system adopts the connected
crawler mechanism. It had 3 connected stages with the motor-driven crawler tracks on each side. RC-servo
motors were used for driving joints between the stages. This system also has a high mobility. In this paper,
we showed the mechanical features, and proposed the operation strategies for autonomous motions. We have
also made verification experiment of proposed operation strategy. For this verification, we did 2 types of
experiment. One was that the robot passes over bumps with different heihgts. The other was stairs ascending.
Both experiments had a great success. There were remarkable points in these experiments. These experiments
showed that the robot can pass over the different height and different structual obstacles by using only (same)
strategy. Moreover the sensors which realize proposed strategy were very simple, and the number of sensor
was very small. Therefore it can be concluded that proposed strategy has extremely high usefulness.
1 INTRODUCTION
Since there is a great meaning to use crawler mecha-
nisms as a mobile function on rough terrain, the con-
struction machineries, the tanks, and a lot of rough
terrain mobile robots adopt a crawler mechanism. Es-
pecially many rescue robots use the crawler mech-
anisms. Because, in general, crawler mechanisms
can obtain big impulsion on rough terrain than the
leg mechanism and the wheel mechanisms. On the
contrary, it also has weak points as a poor stability
in complex geographical features. And the mobil-
ity on the area such as stairs is inferior to that of the
leg(Hirose, 2000).
Therefore, a lot of researches have tried to supple-
ment with these weak points. The main theme com-
mon to those researches is to improve the mobility
performance on rough terrain. Generally the variable
crawler structure is adopted as an approach for this
main theme. In order to realize this transformation,
many research proposed connected crawler mecha-
nisms which crawler stages were connected by active
joints. Lee et al (Lee, 2003) designs two stages one
active joint type resucue robot that uses tow triangu-
lar crawlers, and shows the high mobility by the com-
parison of climb-able step height between proposed
mechanism and a usual one track type. ”Souryu-
III” (Takayama, 2004) is the connected crawler robots
of 3 stages 2 joints type for resuce operations, and
it shows high mobility by some basic experiments
such as climbing up a step and passing over a gap.
”MOIRA”(Osuka, 2003) is also rescue robot which
is 4 stages 3 joints type connected crawler. As men-
tioned above, the mobility performance was improved
by using connected crawler mechanisms.
Although we can see such research, there are no
robots which can move autonomously. The one of the
most important reason to introducing rescue robots
to disaster places is to automate a sufferer search-
ing in place of the manpower searching. If many
396
Yokota S., Ohyama Y., Hashimoto H., She J., Kawabata K., Blazevic P. and Kobayashi H. (2007).
DEVELOPMENT OF THE CONNECTED CRAWLER ROBOT FOR ROUGH TERRAIN - Realization of the Autonomous Motions.
In Proceedings of the Four th International Conference on Informatics in Control, Automation and Robotics, pages 396-401
DOI: 10.5220/0001624203960401
Copyright
c
SciTePress