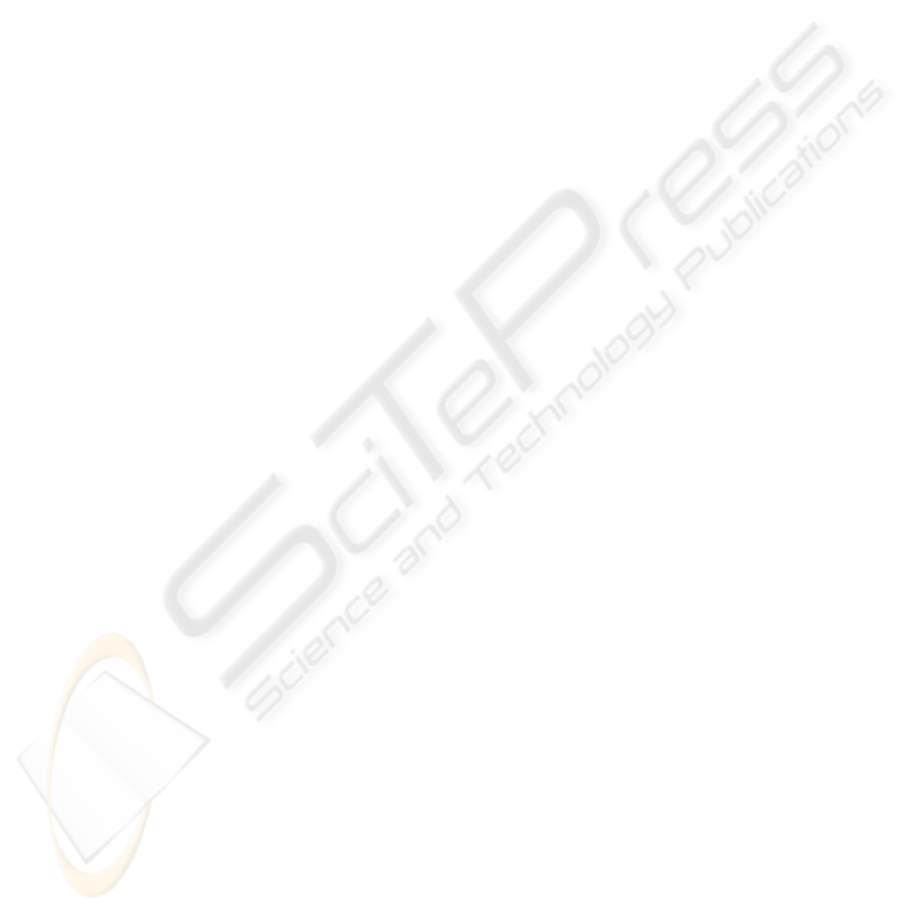
measurement noise during identification. As a result,
CR can be employed to verify estimation validity,
thereby increasing the overall reliability of other
characterisation methods.
The computational complexity of CR, due to the
inefficient grid based search used in this study,
means that it is most appropriate for offline sensor
characterisation. Further investigations include ways
to speed up the computation and reduce the
estimation bias.
ACKNOWLEDGEMENTS
The authors wish to acknowledge the financial
support of the Virtual Engineering Centre, Queen’s
University Belfast, http://www.vec.qub.ac.uk.
REFERENCES
Forney, L. J., Fralick G. C., 1994. Two wire
thermocouple: Frequency response in constant flow.
Rev. Sci. Instrum., 65, pp 3252-3257.
Hung, P., McLoone, S., Irwin G., Kee, R., 2003. A Total
Least Squares Approach to Sensor Characterisations.
Proc. 13th IFAC Symposium on Sys. Id., Rotterdam,
The Netherlands, pp 337-342.
Hung, P. C., McLoone, S., Irwin G., Kee, R., 2005a. A
difference equation approach to two-thermocouple
sensor characterisation in constant velocity flow
environments. Rev. Sci. Instrum., 76, Paper No.
024902.
Hung, P. C., McLoone, S., Irwin G., Kee, R., 2005b.
Unbiased thermocouple sensor characterisation in
variable flow environments. Proc. 16th IFAC World
Congress, Prague, Czech Republic.
Isermann, R., 2005. Mechatronic Systems – Innovative
Products with Embedded Control. Proc. 16th IFAC
World Congress, Prague, Czech Republic.
Kee, R. J., Blair, G. P., 1994. Acceleration test method for
a high performance two-stroke racing engine. Proc.
SAE Motorsports Conference, Detroit, MI, Paper No.
942478.
Kee, R. J, O'Reilly, P. G., Fleck, R., McEntee, P. T., 1999.
Measurement of Exhaust Gas Temperature in a High
Performance Two-Stroke Engine. SAE Trans. J.
Engines, 107, Paper No. 983072.
Kee, J. K., Hung, P., Fleck, B., Irwin, G., Kenny, R.,
Gaynor, J., McLoone, S., 2006. Fast response exhaust
gas temperature measurement in IC Engines. SAE
2006 World Congress, Detroit, MI, Paper No. 2006-
01-1319.
Liu, H., Xu, G., Tong, L., 1993. A deterministic approach
to blind identification of multichannel FIR systems.
Proc. 27th Asilomar Conference on Signals, Systems
and Computers, Asilomar, CA, pp. 581-584.
McLoone, S., Hung, P., Irwin, G., Kee, R., 2006.
Exploiting A Priori Time Constant Ratio Information
in Difference Equation Two-Thermocouple Sensor
Characterisation. IEEE Sensors J., 6, pp. 1627-1637.
Pfriem, H., 1936. Zue messung verandelisher
temperaturen von ogasen und flussigkeiten. Forsch.
Geb. Ingenieurwes, 7, pp. 85-92.
Petit, C., Gajan, P., Lecordier, J. C., Paranthoen, P., 1982.
Frequency response of fine wire thermocouple. J.
Physics Part E, 15, pp. 760-764.
Sato, Y., 1975. A method of self-recovering equalization
for multilevel amplitude modulation systems. IEEE
Trans. in Communications, 23, pp. 679-682.
Tagawa, M., Ohta, Y., 1997. Two-Thermocouple Probe
for Fluctuating Temperature Measurement in
Combustion – Rational Estimation of Mean and
Fluctuating Time Constants. Combustion and Flame,
109, pp 549-560.
Xu, G., Liu, H., Tong, L., Kailath, T., 1995. A least-
squares approach to blind channel identification. IEEE
Trans. on Signal Processing, 43, pp. 2982-2993.
Van Huffel S., Vandewalle, J., 1991. The Total Least
Squares Problem: Computational Aspects and
Analysis, SIAM, Philadelphia, 1
st
edition.
ICINCO 2007 - International Conference on Informatics in Control, Automation and Robotics
16