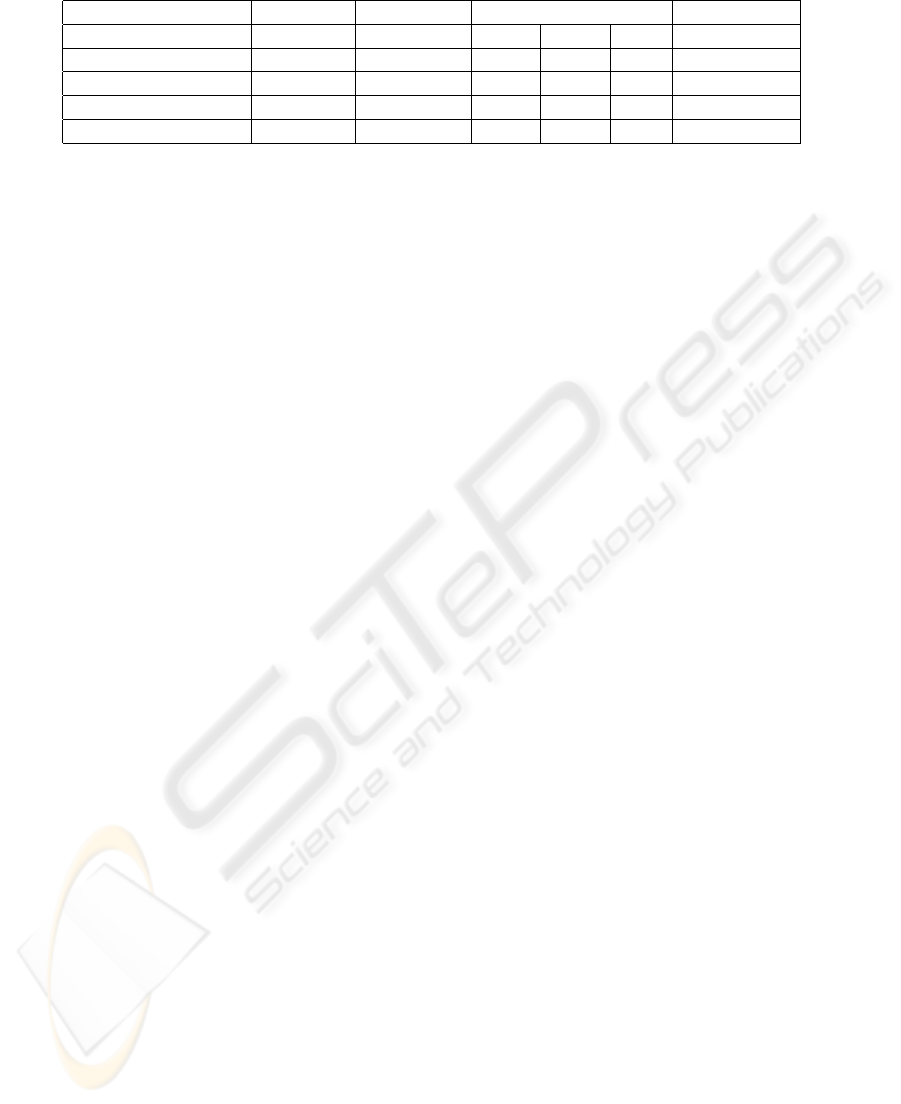
Table 1: Computational results.
First solution Best solution
Reduction technique Total time Total nodes time nodes C
max
C
max
None 58.832 493167 0.032 1875 100 98
NL
ordinary
2.104 37483 0.048 2157 98 98
SSM
strict
0.476 13374 0.120 6492 131 128
SSM + NL
ordinary
1.084 28583 0.040 681 102 98
compute the first feasible solution when different re-
duction techniques were used. The test with nor-
mal sleep set method which compares and removes
only time persistent pairs of transitions in combina-
tion with ordinary non-lazy runs was performed. This
is represented as SSM + NL
ordinary
in the table 1. The
combination of SSM + NL
ordinary
found the optimal
solution. This is due to the fact that only time per-
sistent transitions were pruned. No solutions could
be found for the strict non-laziness setting when ap-
plied alone or in combination with the strict sleep-set
method and the normal sleep-set method. It should
be noted that the reduction techniques ordinary non-
lazy runs and the normal sleep-set method are the
only combinations which theoretically guaranty that
the optimal solution is not pruned. The strict sleep set
method in general should only be used as a heuristic.
6 CONCLUSION
A new and a straightforward approach to model
scheduling problems in multi-product batch plants
and to derive production schedules based on symbolic
reachability analysis of TA has been introduced. The
experimental results show that the method can solve
scheduling problems in process industries efficiently
within a limited computation time. The main aspect
to be considered is the time required by the TA ap-
proach to specify and formulate the scheduling prob-
lem. It is relatively easy when compared to formulat-
ing it as MILP which are usually cumbersome. The
efficiency of the approach to derive solutions with re-
duced computational effort have been achieved with
different search space reduction techniques.
Future work on the TA based approach will focus
on online scheduling problems in which the arrival
time of jobs is not known in advance and subject to
random perturbations.
ACKNOWLEDGEMENTS
The authors gratefully acknowledge the financial sup-
port by the Graduate School of Production Engineer-
ing and Logistics at the University of Dortmund.
REFERENCES
Abdeddaim, Y. and Maler, O. (2001). Job-shop scheduling
using timed automata. Computer Aided Verification
(CAV), Springer, pages 478–492.
Alur, R. and Dill, D. (1994). A theory of timed automata.
Theor. Comp.Science, 126(2):183–235.
Barthomieu, B. and Diaz, M. (1991). Modeling and
verification of time dependent systems using timed
petri nets. IEEE Transactions Software Engineering,
126(2):259–273.
Bauer, N., Kowalewski, S., Sand, G., and Loehl, T. (2000).
A case study: Multi product batch plant for the
demonstration of scheduling and control problems.
In ADPM2000 Conference Proceedings-Hybrid Dy-
namic Systems, pages 383–388. Shaker.
Behrmann, G., Fehnker, A., Hune, T., Peterson, P., Larsen,
K., and Romjin, K. (2001). Efficient guiding to-
wards cost-optimality in UPPAAL. In Proceedings
TACAS’01, pages 174–188.
Godefroid, P. (1991). Using partial orders to improve auto-
matic verification methods. In Proc. 2nd Workshop on
Computer Aided Verification, 531 of LNCS:176–185.
Kallrath, J. (2002). Planning and scheduling in the process
industry. OR Spectrum, 24:219–250.
Panek, S., Engell, S., and Lessner, C. (2005). Scheduling
of a pipeless multi-product batch plant using mixed-
integer programming combined with heuristics. In Eu-
ropean Symposium on Computer Aided Process Engi-
neering, ESCAPE 15, pages 1033–1038.
Panek, S., Engell, S., and Stursberg, O. (2006). Efficient
synthesis of production schedules by optimization of
timed automata. Control Engineering Practice, pages
149–156.
Panek, S., Engell, S., Subbiah, S., and Stursberg, O. (2007).
Scheduling of multi-product batch plants based upon
timed automata models. Submitted to Comp. Chem.
Eng.
Pantelides, C. (1994). Unified frameworks for optimal pro-
cess planning and scheduling. In Proceedings 2nd
conference Foundations of Computer Aided Process
Operations, pages 253–274.
ICINCO 2007 - International Conference on Informatics in Control, Automation and Robotics
148