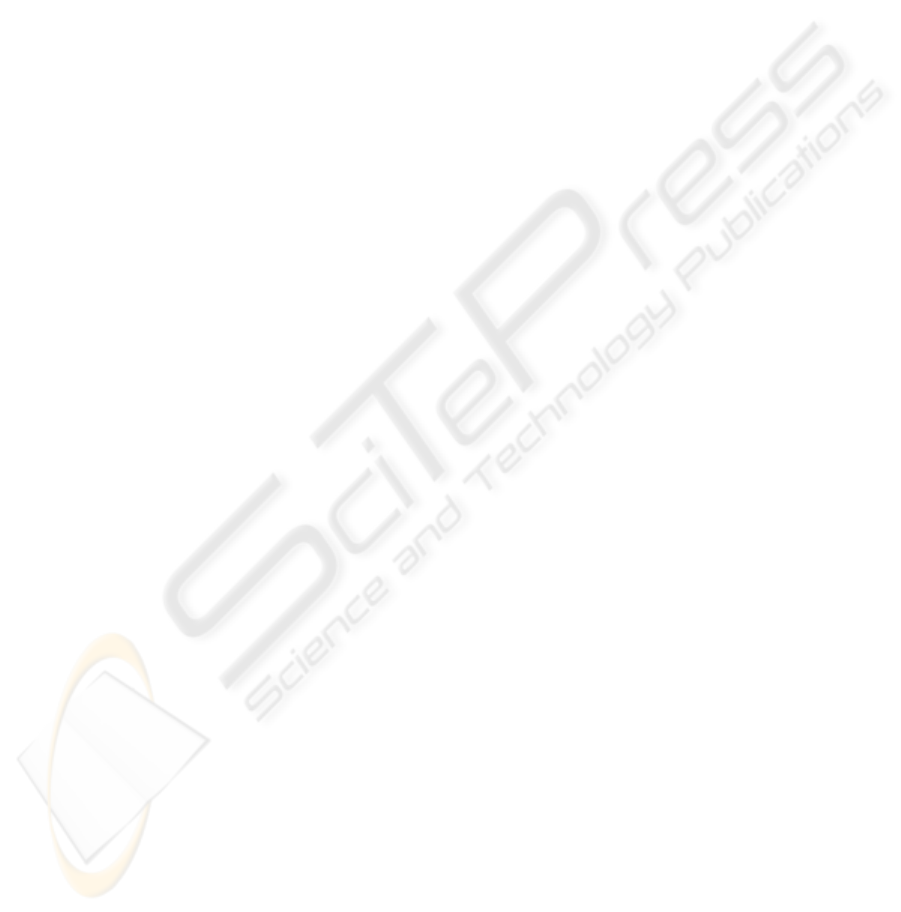
tasks that cannot be performed efficiently by a sin-
gle robot or operator, but require the cooperation of
number of them. The cooperation of multiple robots
and/or operators is particularly beneficial in cases
when robots must operate in unknown and dynamic
environments. Teleoperation of multiple robots by
multiple operators over Internet has been extensively
studied for couple of years. A good survey can be
found in (Lo et al., 2004).
In this paper we present a teleoperation system
that consists of two mobile robots, where one of them
serves as Scout and the other one as Manipulator.
Scout explores the remote site and with its sensory
information assists the operator controlling the Ma-
nipulator, which executes tasks of direct interaction
with working environment by using the robot arm
mounted on it. In order to guarantee safe robots
navigation in dynamic environments and/or at high-
speeds, it is desirable to provide a sensor-based col-
lision avoidance scheme on-board the robots. By
having this competence, the robots can react with-
out delay on changes in its surrounding. Usually used
methods for obstacle prevention are based on virtual
forces creation between the robot and the closest ob-
stacle, see e.g. (Borenstein and Koren, 1990) and
(Lee et al., 2006), where the force is inversely pro-
portional to the distance between them. In this pa-
per, we propose a new obstacle avoidance algorithm
based on the dynamic window (DW) approach pre-
sented in (Fox et al., 1997). Main advantage of our
algorithm is that it takes robot dynamic constraints
directly into account, which is particularly beneficial
for safe navigation at high-speeds as the safety mar-
gin depends not only on distances between the robot
and the nearby obstacles, but also on the velocity of
robot motion. The algorithm is implemented on both
robots and each robot considers the other one as the
moving obstacle.
The paper is structured as follows. In Section 2,
we present overview of developed mobile robot tele-
operation system. Force feedback loops implementa-
tions are described in section 3. Section 4 describes
experimental results. We conclude with a summary
and a discussion of future work.
2 OVERVIEW OF THE SYSTEM
The teleoperation system considered in this paper is
schematically illustrated in Fig. 1. It consists of two
mobile robots (Scout and Manipulator) operating in
a remote environment and two operator stations with
PCs and force feedback joysticks. While the opera-
tors’ PCs (clients) are directly connected to the Inter-
net, robots’ on-board PCs (servers) are connected to
Internet via wireless LAN. Each operator controls a
single robot and receives visual and other data from
both robots.
Mobile robots that we use are PIONEER 2DX
(Scout) and PIONEER 3DX (Manipulator) manufac-
tured by ActivMedia Robotics. Scout is equipped with
an on-board PC, a ring with sixteen sonar sensors,
laser distance sensor and a Sony EVI-D30 PTZ cam-
era. Manipulator carries an external laptop computer,
a ring with sixteen sonars and a Cannon VC-C50i PTZ
camera. Additionally, a Pioneer arm with five degrees
of freedom and a gripper is mounted on the Manipu-
lator. Sonars on each robot are used for obstacle de-
tection.
Any personal computer with an adequate Inter-
net connection, a force feedback joystick and devel-
oped client application can serve as an operator sta-
tion. The client application has graphical user inter-
face (GUI) that enables the operator to preset the oper-
ation mode (driving, manipulation, observation) and
to supervise both mobile robot actions.
Logitech WingMan Force 3D Joystick used in our
experiments has two axes on which it can read inputs
and generate force: x (stick up-down) and y (stick left-
right) and two additional axes that can only read in-
puts: z (stick twist) and throttle. GUI provides ad-
ditional operator input, e.g. when switching between
operating modes. Both joystick references and GUI
input are collectively referred to as commands. When
client application is actively connected with the mo-
bile robot and driving operating mode is chosen on
the GUI, joystick x and y axes are used to input de-
sired translational and rotational velocities, respec-
tively. Force feedback is applied on the same two
axis, defying commands that would lead robot toward
detected obstacles. If manipulation operating mode is
chosen two joystick buttons are used to chose one of
arm’s 6 joints, third button sends the arm in its home
position and y axis is used to input chosen joint veloc-
ity and to display reflected force. In observation oper-
ating mode joystick x axis is used to tilt the camera, y
axis to pan it, throttle is used for adjusting zoom, and
one joystick button sends camera to its home position.
Communication between server applications run-
ning on the mobile robots’ on-board PCs and client
applications running on the operators’ PCs is initial-
ized and terminated by client applications. In spe-
cial cases, e.g. when robot is turned off or malfunc-
tioning or in case of communication failure, a server
application can refuse or terminate the connection.
Communication is implemented using three indepen-
dent communication modules: control module, im-
age transfer module and info module. Modules are
TELEOPERATION OF COLLABORATIVE MOBILE ROBOTS WITH FORCE FEEDBACK OVER INTERNET
431